精密压力表检测的重要性与应用范围
精密压力表作为工业生产和实验室中测量压力参数的关键仪器,其准确性直接影响设备运行安全、产品质量及实验数据的可靠性。它广泛应用于石油化工、电力能源、制药、航空航天等领域,用于监测管道压力、设备承压能力以及工艺流程控制。由于长期使用、环境因素或机械振动可能导致仪表性能下降,定期开展精密压力表检测是确保其计量性能符合国家标准的必要手段,也是企业质量控制体系的重要环节。
精密压力表检测的核心项目
1. 外观与功能性检查
检测人员需检查表壳完整性、表盘清晰度、指针灵活性及标识完整性。重点关注玻璃表面是否划伤、刻度线是否模糊、指针是否存在卡顿现象。同时验证仪表附件(如接头、泄压阀)的密封性和连接可靠性。
2. 零点误差测试
在无压力输入状态下,观察指针是否准确指向零位。若偏离量超过JJG 49-2013《弹性元件式精密压力表和真空表检定规程》的允许范围(通常≤0.5%满量程),需通过机械调零装置进行校准。
3. 示值误差与线性度检测
使用压力标准器对仪表进行升压和降压测试,覆盖10%、25%、50%、75%、100%量程点。通过计算各点实测值与标准值的偏差,判断是否符合精度等级要求(如0.25级、0.4级)。同时分析数据线性度,确保全量程误差分布均匀。
4. 回程误差评估
在相同压力点下,记录升压与降压过程中指示值的最大差值。精密压力表的回程误差需≤允许误差绝对值,若超标可能提示传动机构磨损或弹性元件老化。
5. 长期稳定性试验
将仪表持续加压至满量程的110%,保持4小时后恢复常压,观察零点漂移和量程变化。此测试可验证弹性元件的抗疲劳性能及材料的蠕变特性。
6. 温度影响量检测
在高低温试验箱中模拟-10℃至+50℃工作环境,检测温度变化对示值的影响。要求温度每变化10℃,示值误差变化不超过基本误差限的1/4。
检测流程与技术要求
标准检测流程包括:预处理(静置24小时消除残余应力)→目视检查→零点校准→逐点加压测试→数据记录与分析→密封性验证(1.5倍满量程保压试验)。检测环境需满足(20±5)℃、相对湿度≤85%的要求,标准器的扩展不确定度应≤被检表允许误差的1/4。
维护保养与周期建议
日常使用中应避免剧烈震动、过载冲击及腐蚀性介质接触。根据JJG 49规定,精密压力表检定周期一般为1年,在恶劣工况下需缩短至6个月。检测不合格的仪表应及时维修或更换,严禁通过调整量程范围强制使用。
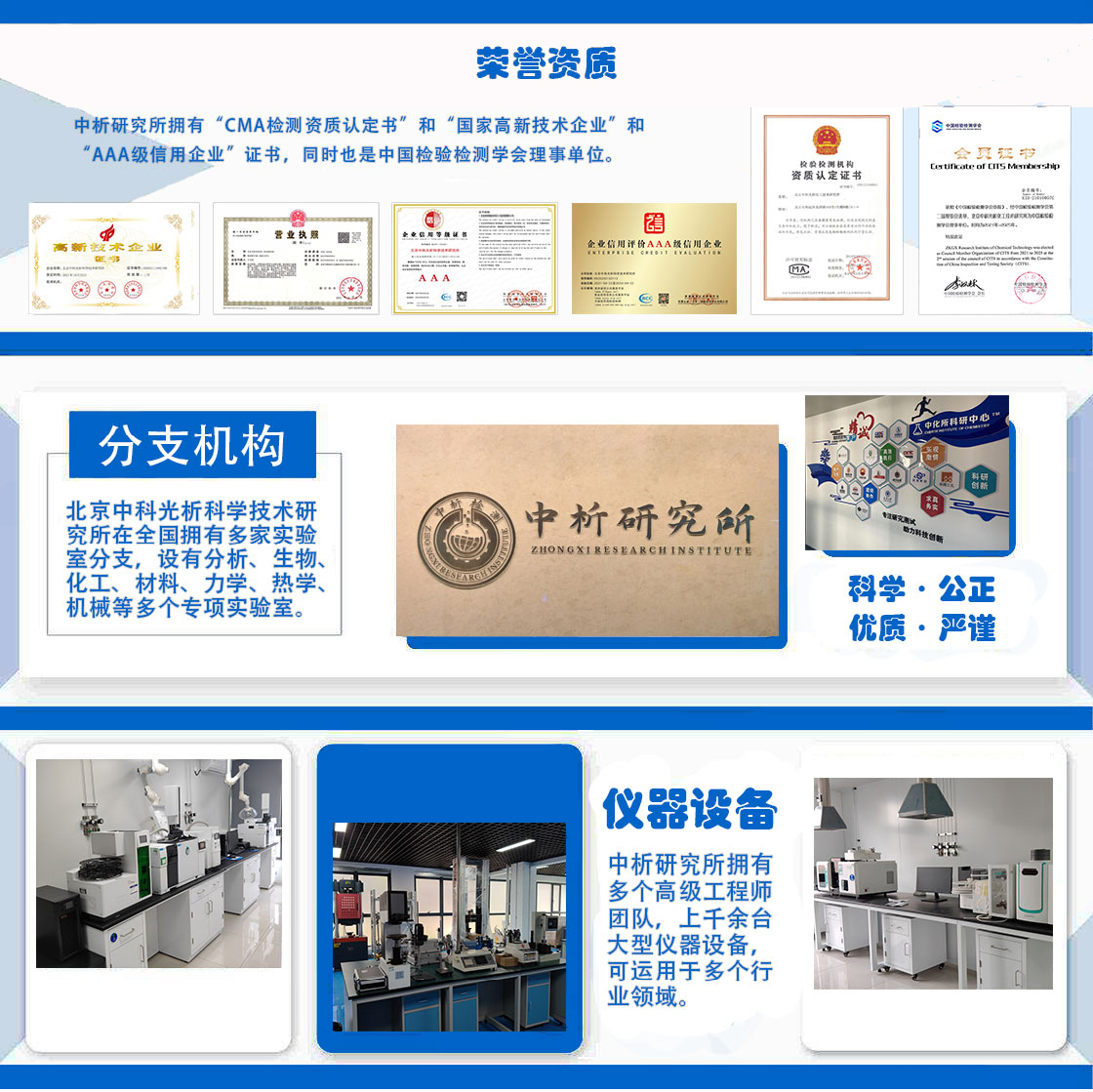
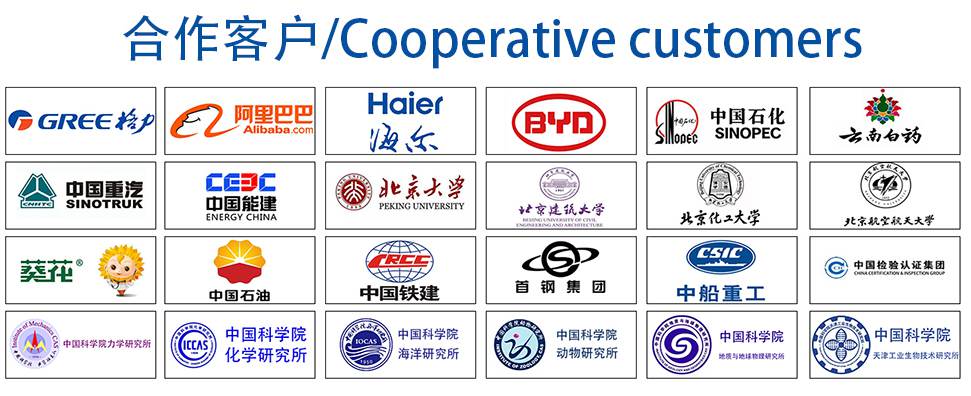