边部密封组件及镶嵌件检测的重要性
边部密封组件及镶嵌件作为工业装备、精密机械及高端设备中的核心零部件,其性能直接影响设备的密封性、耐用性与安全性。在航空航天、汽车制造、能源化工等领域,此类组件通常需要承受高温、高压、腐蚀性介质等复杂工况的长期考验。若密封或镶嵌结构存在缺陷,轻则导致介质泄漏、能效降低,重则引发设备故障甚至安全事故。因此,建立科学完善的检测体系,对组件尺寸精度、材料性能、密封效果进行系统性验证,已成为保障工业设备稳定运行的关键环节。
核心检测项目及方法
1. 几何尺寸与形位公差检测
采用三坐标测量仪、激光扫描仪等高精度设备,对密封面的平面度、镶嵌槽的深度/宽度公差、配合间隙等关键尺寸进行全尺寸检测。针对异形结构件,需结合三维建模数据进行对比分析,确保实际加工尺寸与设计图纸的偏差控制在±0.01mm以内。
2. 密封性能验证
通过气密性试验台实施分级压力测试,模拟实际工况进行氦质谱检漏或水压试验。重点检测密封圈压缩回弹率、界面接触应力分布,以及循环载荷下的密封持久性,要求泄漏率≤1×10⁻⁶ Pa·m³/s。
3. 材料特性分析
使用光谱仪、金相显微镜等设备进行材料成分验证,检测硬度(HV)、抗拉强度(≥800MPa)等机械性能。针对高温应用场景,需额外开展热膨胀系数测试(CTE≤12×10⁻⁶/℃)和高温蠕变试验。
4. 表面完整性评估
借助电子显微镜(SEM)和轮廓仪,对密封面的表面粗糙度(Ra≤0.8μm)、微观裂纹、镀层附着力进行检测。对陶瓷/金属复合镶嵌件需重点关注界面结合强度,采用划痕试验法评估镀层结合力(临界载荷≥50N)。
5. 耐环境试验
执行盐雾试验(1000h)、湿热循环试验(-40℃~150℃)等加速老化测试,评估组件在腐蚀性介质、温度交变等极端环境下的性能衰减情况,要求关键参数变化率≤15%。
检测标准与质量控制
检测过程需严格遵循ASME B16.20、ISO 3601-3等国际标准,结合企业自定义的QMS质量控制体系。建议采用SPC统计过程控制技术,对关键工序的CPK值进行动态监控,确保制程能力指数≥1.33。通过建立检测数据库,实现质量数据的可追溯性管理。
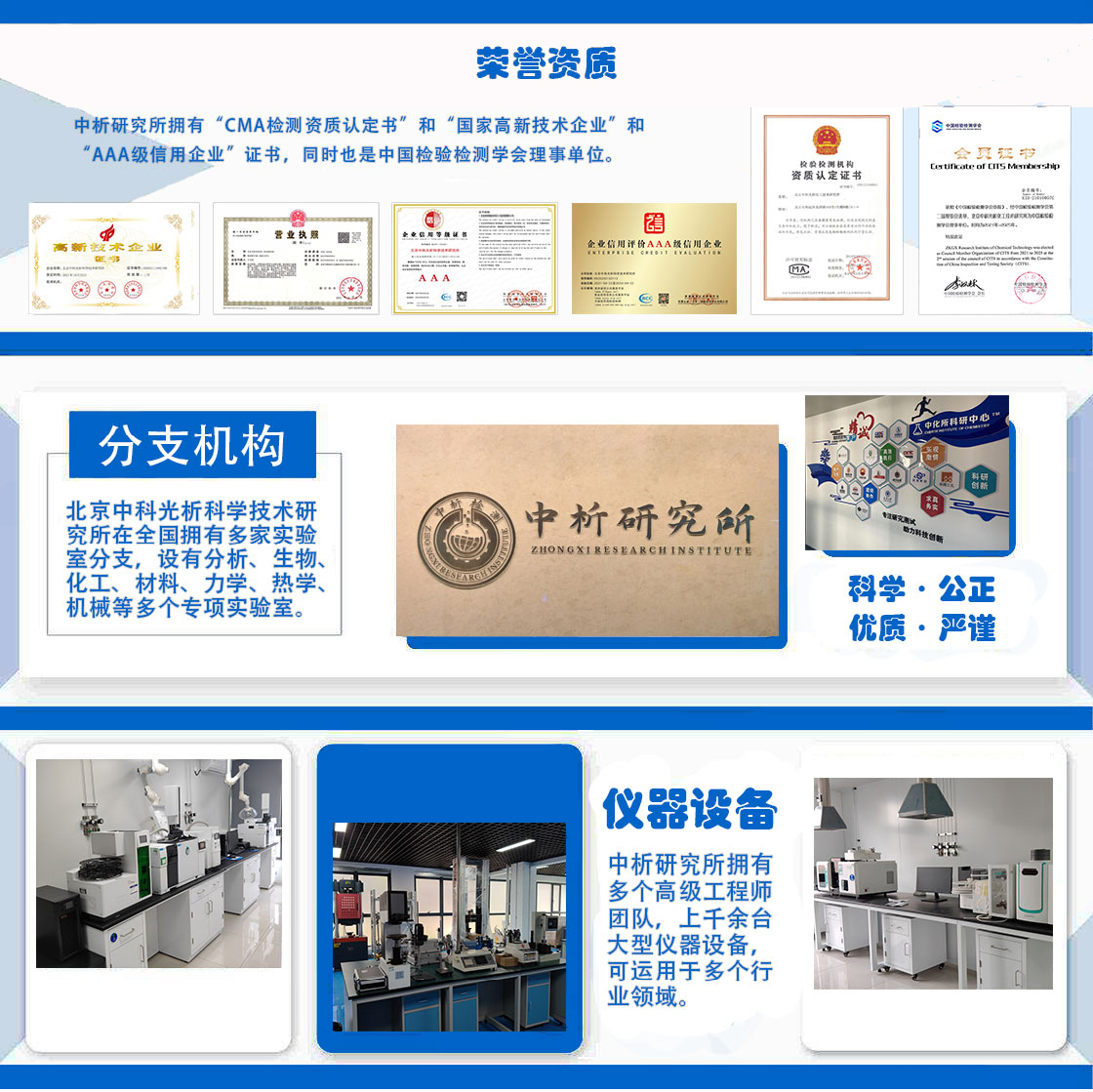
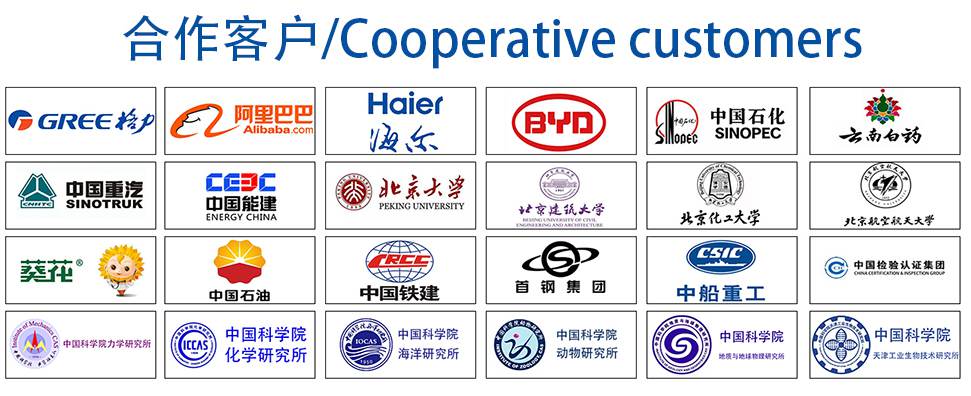