弯管检测的重要性与核心内容
弯管作为管道系统中的关键组件,广泛应用于石油化工、航空航天、船舶制造及建筑工程等领域。其制造质量直接影响管道系统的安全性、密封性和使用寿命。弯管检测的核心在于通过多维度手段验证其几何精度、材料性能及表面完整性,以满足设计规范和工况需求。由于弯管在加工过程中易受弯曲工艺、回弹效应、材料变形等因素影响,检测项目需覆盖尺寸精度、缺陷识别、力学性能等多个维度,确保其在实际应用中能够承受压力、温度变化及机械应力。
弯管检测的主要项目及方法
1. 几何尺寸检测
通过三维扫描仪、卡尺或模板比对法,检测弯管的曲率半径、弯曲角度、直线段长度等参数。重点关注弯曲部位与设计图纸的偏差值,例如弯曲角度误差需控制在±0.5°以内,曲率半径偏差不超过标称值的3%。对于复杂空间弯管,需采用激光跟踪仪进行三维坐标测量,验证空间轨迹的准确性。
2. 壁厚减薄率检测
使用超声波测厚仪或射线检测技术(如X射线),测量弯管外侧拉伸区与内侧压缩区的壁厚变化。根据GB/T 12459标准,碳钢弯管的最大减薄率不得超过原壁厚的12%,不锈钢等高强度材料需控制在8%以内。该检测可预防因过度减薄导致的强度下降或破裂风险。
3. 表面缺陷检测
采用磁粉探伤(MT)或渗透探伤(PT)检测表面裂纹、折叠、划痕等缺陷,尤其关注弯制过程中因材料延展性不足产生的应力裂纹。对于大口径弯管,使用工业内窥镜对内部表面进行目视检查,确保无毛刺或氧化层剥落现象。
4. 力学性能测试
通过取样试验验证弯管的抗拉强度、硬度和延伸率,确保材料在冷弯或热弯加工后仍满足ASTM A234、ASME B16.9等标准要求。对于高压工况应用的弯管,需增加爆破压力试验,验证其耐压能力是否达到设计值的1.5倍以上。
5. 回弹量验证
在弯管成型后24小时内,使用角度尺复测弯曲角度,对比加工时的预补偿值与实际回弹量差异。回弹量过大会导致安装错位,需通过工艺参数优化(如调整芯棒压力、加热温度)减少误差。
检测技术的创新趋势
随着工业4.0的推进,弯管检测正逐步向智能化、数字化发展。光学三维测量系统可实现全尺寸自动比对并生成偏差云图;基于机器视觉的AI算法能快速识别表面微小缺陷;而在线监测技术则可在弯管机加工过程中实时反馈数据,实现闭环质量控制。这些技术革新显著提升了检测效率与精度,为复杂弯管的大规模生产提供了可靠保障。
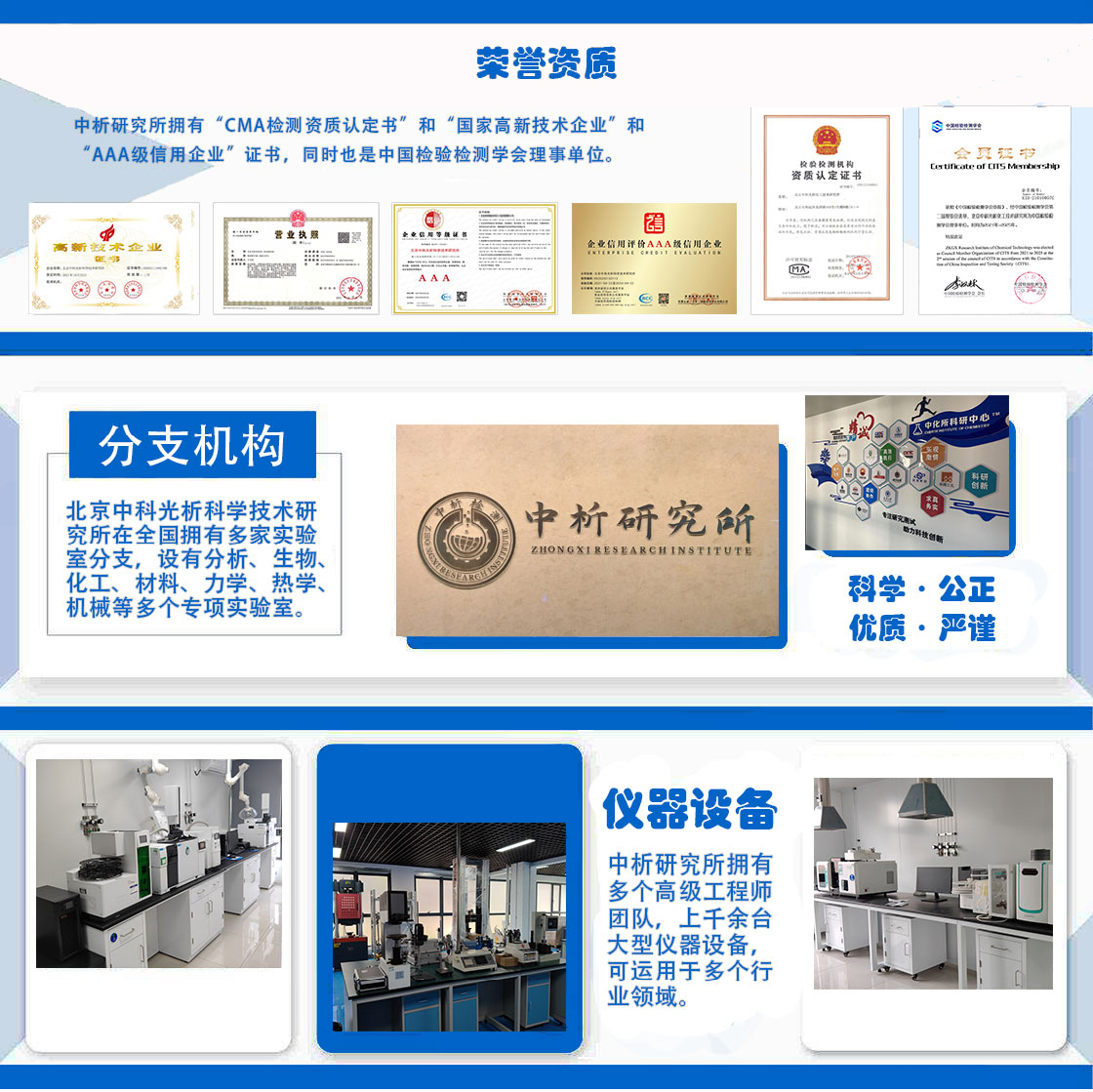
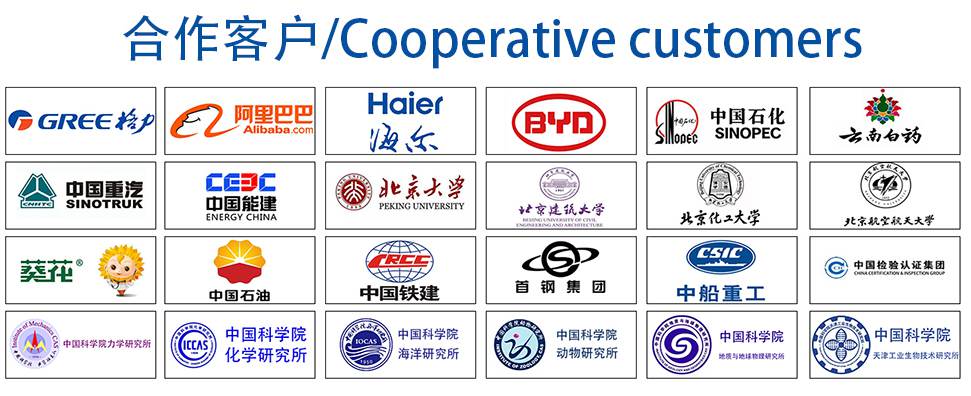