输送管道系统检测项目全解析
输送管道作为能源、化工、市政等领域的关键基础设施,其安全性与稳定性直接影响工业生产效率和公共安全。系统化的检测工作能够及时识别腐蚀、泄漏、结构损伤等隐患,避免因管道失效引发的环境灾害和经济损失。现代检测技术已形成包含物理检测、智能监测、数据分析的综合体系,覆盖从地面到地下、从静态到动态的全生命周期管理。
核心检测项目与技术手段
1. 泄漏与密封性检测
采用红外热成像技术定位温度异常区域,配合声波传感器捕捉管道内流体泄漏产生的声学信号。对于高压管道,需进行氦气示踪法密封测试,检测精度可达0.1cc/min。
2. 壁厚与腐蚀评估
通过超声波测厚仪(UT)进行定点测量,对弯头、焊缝等易损部位实施全覆盖扫描。针对埋地管道,应用交流电压梯度(ACVG)和直流电压梯度(DCVG)技术评估防腐层破损程度。
3. 智能内检测(ILI)
利用几何变形检测器(GP)、漏磁检测器(MFL)和电磁超声检测器(EMAT)等智能机器人,获取管道内壁三维形貌、裂纹深度及金属损失量数据,检测分辨率可达毫米级。
4. 应力与振动分析
布设光纤应变传感器网络,实时监测管道受外力挤压、地基沉降产生的形变。结合加速度传感器分析振动频谱,识别因流体脉动或机械共振引发的异常波动。
特种环境下的专项检测
海底管道检测
采用ROV(遥控无人潜水器)搭载多波束声呐和阴极保护电位测量仪,同步完成外防腐层状态评估与锚害风险排查,作业深度可达3000米。
高温高压管道检测
应用脉冲涡流(PEC)技术穿透保温层检测壁厚,结合X射线数字成像(DR)技术对焊缝进行无损探伤,确保检测过程不影响设备正常运行。
数字化检测管理系统
通过集成GIS地理信息系统与BIM模型,构建管道数字孪生体。检测数据实时上传至云平台后,AI算法可自动生成风险热力图并预测剩余寿命,实现从被动维修到主动预防的转变。
根据API 570、ASME B31.4等国际标准,建议油气输送管道每3-5年开展一次全面检测,城市燃气管网则需每年进行防腐层完整性评估。随着光纤传感、机器视觉等技术的突破,未来管道检测将向更高精度、更低成本和全天候监测方向持续发展。
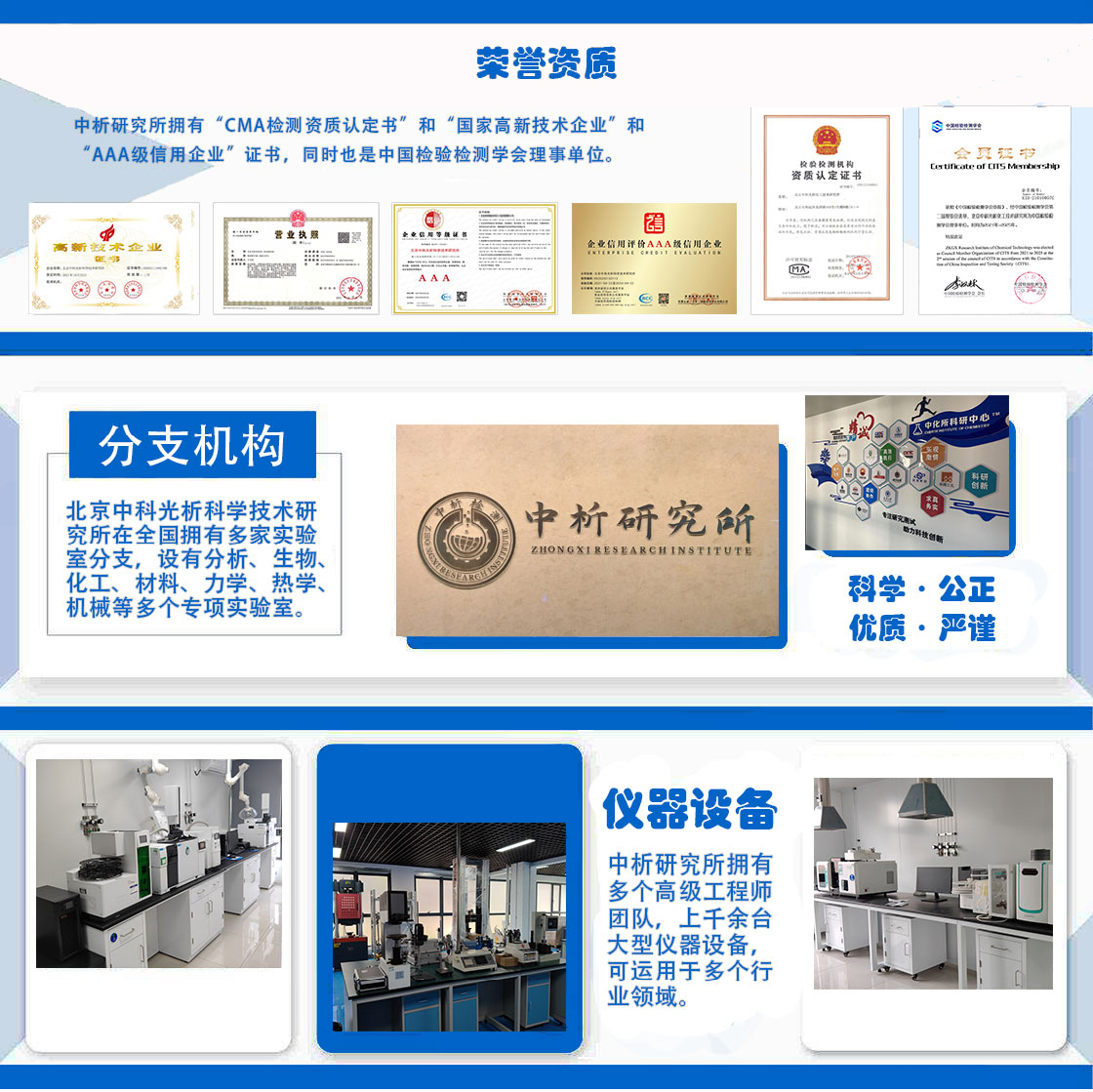
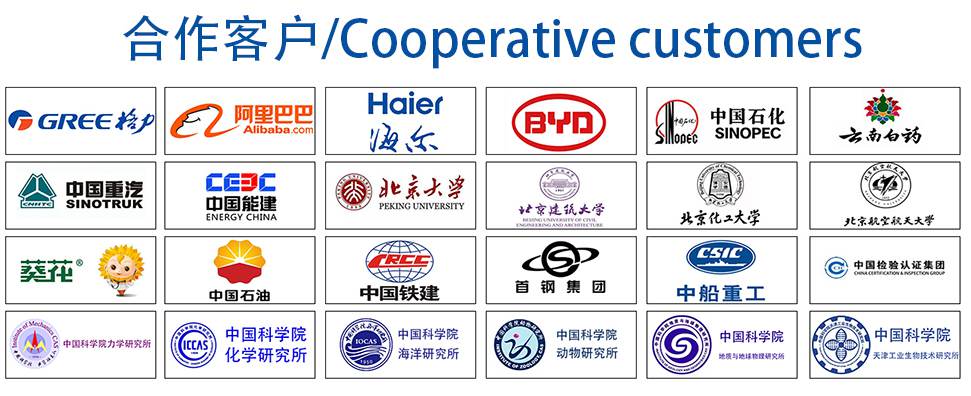