集成电路-数字集成电路检测的重要性与核心流程
随着电子技术的飞速发展,数字集成电路(Digital Integrated Circuit, DIC)已成为现代电子设备的核心组件,广泛应用于通信、计算机、汽车电子及工业控制等领域。其性能的稳定性与可靠性直接影响终端产品的质量。然而,复杂的制造工艺、设计缺陷或环境因素可能导致芯片出现功能异常、时序偏差或物理损伤。因此,数字集成电路检测成为研发、生产及质量控制中不可或缺的环节。通过系统化的检测流程,可精准定位故障点,优化设计参数,并确保芯片在极端条件下的长期稳定运行。
功能测试:逻辑行为的核心验证
功能测试是数字集成电路检测的基础环节,主要验证芯片的逻辑功能是否符合设计规范。通过输入预定义的测试向量(Test Vectors),检测输出信号是否与预期结果一致。测试中需覆盖所有可能的输入组合,包括边界条件和异常场景,例如使用自动测试设备(ATE)执行全真值表验证。对于复杂芯片(如CPU、FPGA),还需结合仿真工具(如ModelSim)进行动态时序仿真,确保逻辑行为的正确性。
电气特性测试:关键参数的定量分析
电气特性测试聚焦于芯片的物理性能指标,包括直流参数(如输入/输出电平、漏电流)与交流参数(如上升/下降时间、传播延迟)。通过高精度仪器(如示波器、参数分析仪)测量供电电压(VCC)波动对信号完整性的影响,以及最大工作频率下的功耗表现。例如,在低功耗芯片检测中,需量化静态电流(IDDQ)以识别潜在短路故障,确保芯片符合能效标准。
时序特性分析:信号同步的精密把控
数字电路对时序的高度敏感性使得时序分析成为检测重点。测试内容涵盖建立时间(Tsetup)、保持时间(Thold)以及时钟-数据偏移(Clock Skew)等关键指标。通过时域反射仪(TDR)和眼图分析仪,可评估信号在传输路径中的抖动(Jitter)和噪声容限。对于高速接口(如DDR、PCIe),需验证其是否符合JEDEC标准定义的时序裕量,避免因时序违例导致系统级失效。
可靠性测试:极限环境下的生存能力
可靠性测试模拟芯片在极端环境下的长期稳定性,包括温度循环(-55°C至150°C)、湿热老化(85°C/85%RH)和高加速寿命试验(HALT)。通过热机械应力分析(TMA)检测封装材料的热膨胀系数是否匹配,预防焊点开裂。此外,静电放电(ESD)测试(如HBM、CDM模型)验证芯片的防静电能力,确保其满足IEC 61000-4-2标准要求。
结构与工艺缺陷检测:微观层面的质量保障
采用非破坏性检测技术(如X射线断层扫描、扫描电子显微镜)对芯片内部结构进行三维成像,识别金属层短路、通孔未对齐或钝化层裂纹等工艺缺陷。对于齐全制程芯片(7nm以下),需利用电子束探针(E-beam Probing)定位晶体管级故障。同时,红外热成像技术可快速定位过热点,辅助分析散热设计的合理性。
生产全流程质量控制:从晶圆到封装的闭环管理
在量产阶段,通过晶圆级测试(Wafer Sort)筛选不良芯片,结合自动光学检测(AOI)系统检查引线键合质量。封装后执行终测(Final Test),采用边界扫描(Boundary Scan)技术验证引脚连接性。测试数据通过统计过程控制(SPC)工具分析,实时监控工艺波动,优化良率。部分高端产线已引入机器学习算法,实现缺陷模式的智能分类与根因追溯。
数字集成电路检测技术的持续进步,正推动检测效率与精度的双重提升。随着AI驱动的自适应测试、量子传感技术的应用,未来检测将更加智能化,为芯片性能的极限突破提供坚实保障。
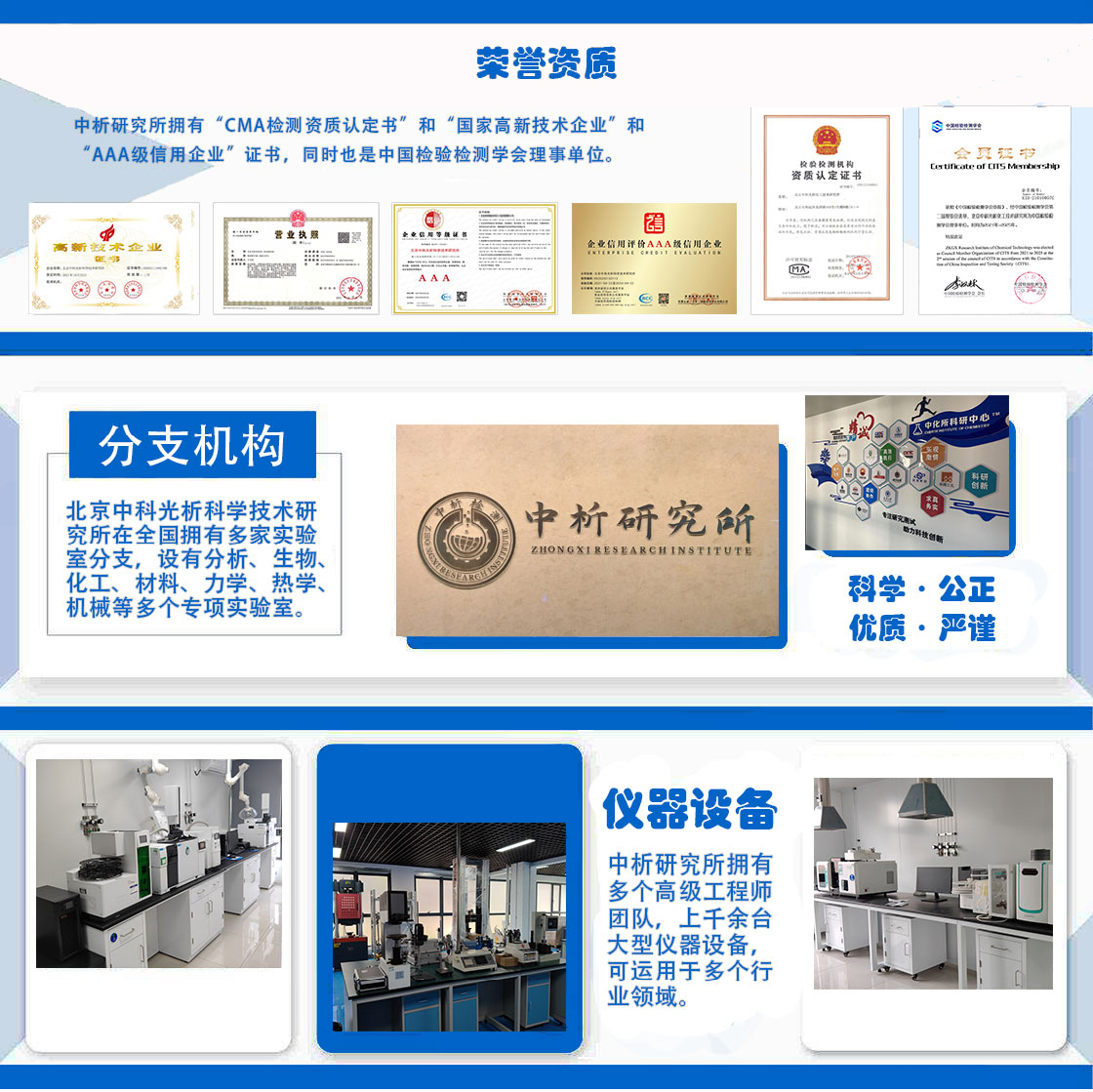
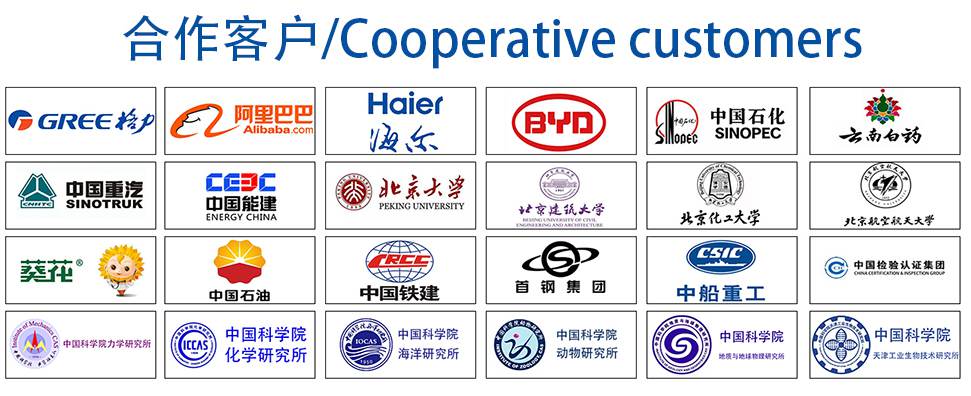