示功仪检测:核心项目与技术解析
示功仪作为工业设备性能检测的重要工具,通过实时采集压力、位移、功率等关键参数,能够直观反映机械系统的工作状态。在石油开采、内燃机测试、压缩机维护等领域,示功仪检测是评估设备效率、诊断故障隐患的核心手段。其检测结果以“示功图”形式呈现,通过曲线形态分析可精准判断设备的气密性、磨损程度及能量转换效率。随着智能化技术的应用,现代示功仪已实现高精度数据采集与自动化分析,但检测项目的完整性与标准化操作仍是确保结果可靠性的关键。
示功仪检测的七大核心项目
1. 压力-位移曲线动态检测
通过传感器同步记录活塞或气缸的压力变化与位移数据,构建完整的示功图。重点验证曲线的闭合性、峰值压力一致性,判断是否存在漏气、阀门异常或负载波动问题。
2. 功率输出效率分析
基于示功图计算有效功与理论功的比值,评估机械系统的能量转换效率。检测时需排除环境温度、润滑状态等干扰因素,确保计算模型的准确性。
3. 循环过程异常诊断
对比单次工作循环与标准循环的差异,识别压力骤降、位移延迟等异常现象。例如在抽油机检测中,可通过示功图判断气锁、砂卡或泵效不足问题。
4. 密封性能验证
通过检测压缩/膨胀阶段的压力保持能力,评估气缸、阀门等部件的密封状态。检测中需关注压力曲线的衰减速率是否符合行业标准(如API 11PVT)。
5. 动态响应特性测试
模拟设备在不同转速、负载下的工况,检测示功仪对快速压力变化的捕捉能力。重点验证传感器的频率响应范围(通常需达到200Hz以上)和数据采集系统的实时性。
6. 温度漂移补偿检测
在-20℃至80℃环境温度范围内测试示功仪的测量稳定性,校准由于温度变化导致的零点漂移和灵敏度偏差,确保野外作业的数据可靠性。
7. 多系统同步校准
对压力传感器、位移传感器、数据采集模块进行联合标定,使用标准压力发生器(精度0.1级)和激光测距仪验证系统的整体误差是否低于1.5%FS。
检测流程的标准化实施
示功仪检测需遵循严格的流程规范:设备预热15分钟→环境参数记录→传感器安装与归零→三次空载测试→实际工况数据采集→异常数据复测→结果分析与报告生成。检测过程中必须使用经计量认证的标准器具,并定期参与实验室间比对(ILC)以保证检测一致性。
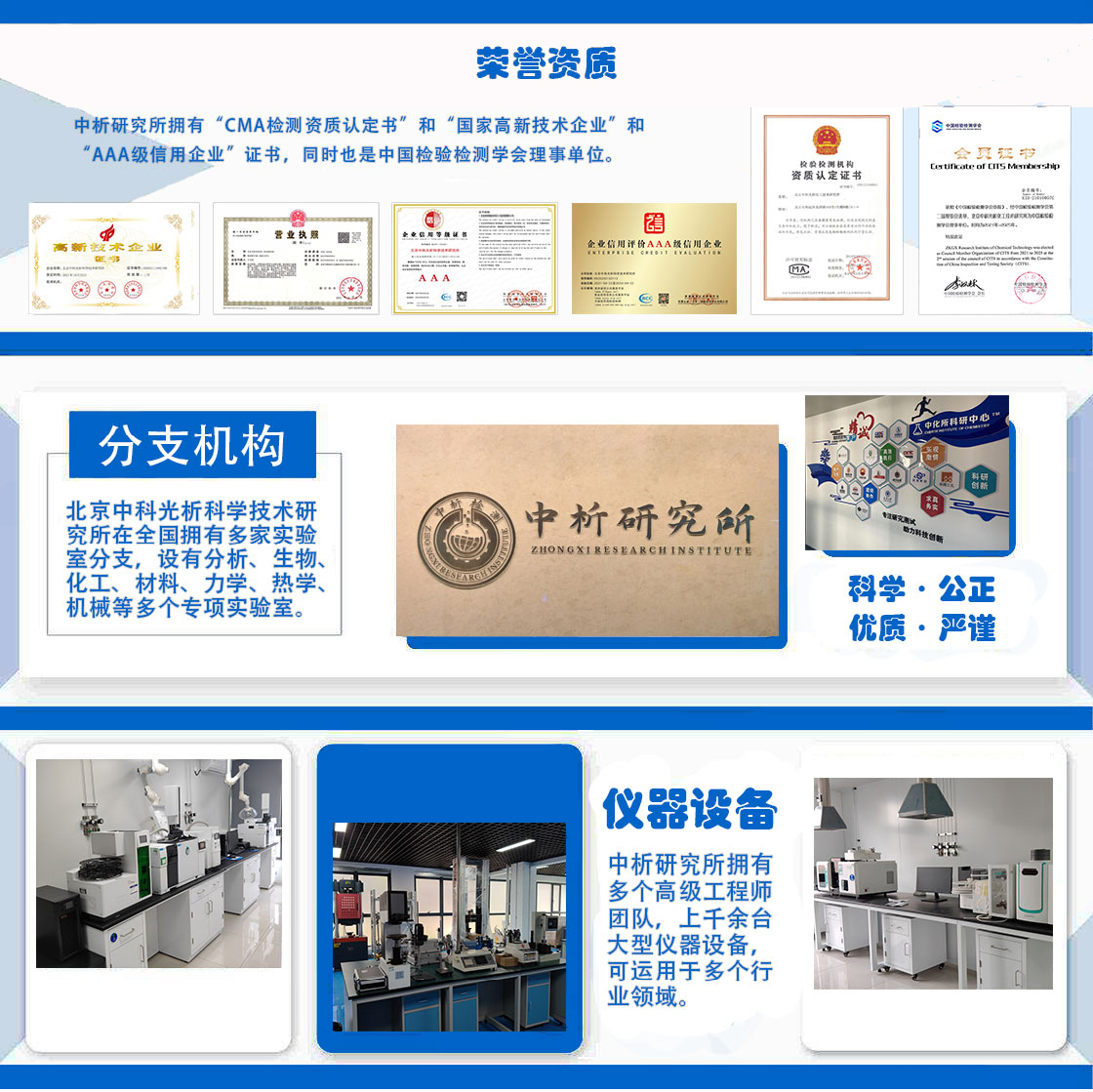
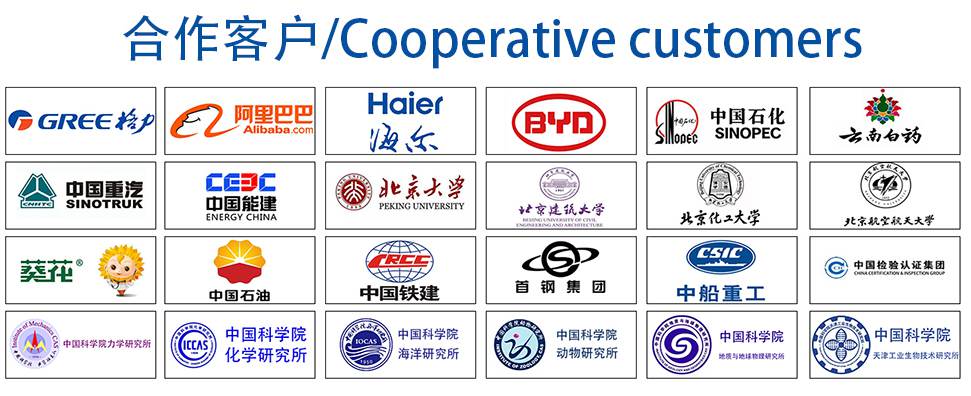