工程机械轮胎检测的重要性与核心项目解析
工程机械轮胎作为挖掘机、装载机、推土机等重型设备的核心承载部件,其性能直接关系到设备作业效率与安全。由于长期承受高负荷、复杂地形及恶劣工况的考验,轮胎的磨损、老化、结构损伤等问题频发。专业的轮胎检测体系能有效预防爆胎事故,延长使用寿命,降低运营成本。根据GB/T 2983-2015《工程机械轮胎技术要求》等标准,现代检测技术已形成涵盖物理性能、材料特性、结构完整性等多维度的评价体系。
一、结构完整性检测
通过X射线探伤仪和超声波检测设备对轮胎内部进行无损检测,精准识别胎体帘线断裂、钢丝圈变形、气密层损伤等隐患。采用3D激光扫描技术建立轮胎三维模型,计算胎肩厚度偏差率(≤8%为合格),特别关注轮胎与轮辋接合部位的密封性能。
二、胎面磨损与抓地力测试
使用深度规测量花纹深度,当剩余深度低于新胎标准的30%时需强制更换。实验室通过转鼓试验机模拟不同工况,检测湿地摩擦系数(要求≥0.45)和抗滑水性能。针对矿山等特殊环境,还需进行岩石切割试验评估抗划伤能力。
三、动态负荷性能检测
在压力试验机上实施静态负荷测试(达额定负荷的300%),同时使用红外热像仪监测温度分布,异常温升超过15℃即判定存在结构缺陷。动态耐久性测试需持续72小时以上,模拟实际作业中的交变应力,记录胎体分层、脱圈等失效模式。
四、气压与热老化评估
采用高精度数字胎压计(误差≤±1.5kPa)每日监测压力波动,结合胎温传感器数据构建压力-温度补偿模型。通过热重分析仪(TGA)检测橡胶材料的热分解温度,当质量损失达5%的温度点低于210℃时判定胶料老化严重。
五、翻新轮胎专项检测
对预翻新轮胎进行全息剪切干涉检测,基体损伤面积超过3cm²禁止翻新。翻新后需通过高速平衡试验(残余不平衡量≤120g·cm),并采用电子鼻技术检测硫化过程中产生的挥发性有机物(VOC)浓度,确保环保指标达标。
随着物联网技术的发展,智能轮胎监测系统(TPMS)已实现实时采集压力、温度、磨损量等18项参数,结合大数据分析可预测剩余使用寿命。建议企业建立三级检测体系:日常点检(8项基础指标)+月度专业检测(23项扩展参数)+年度全面评估(46项全指标),构建全生命周期管理体系。
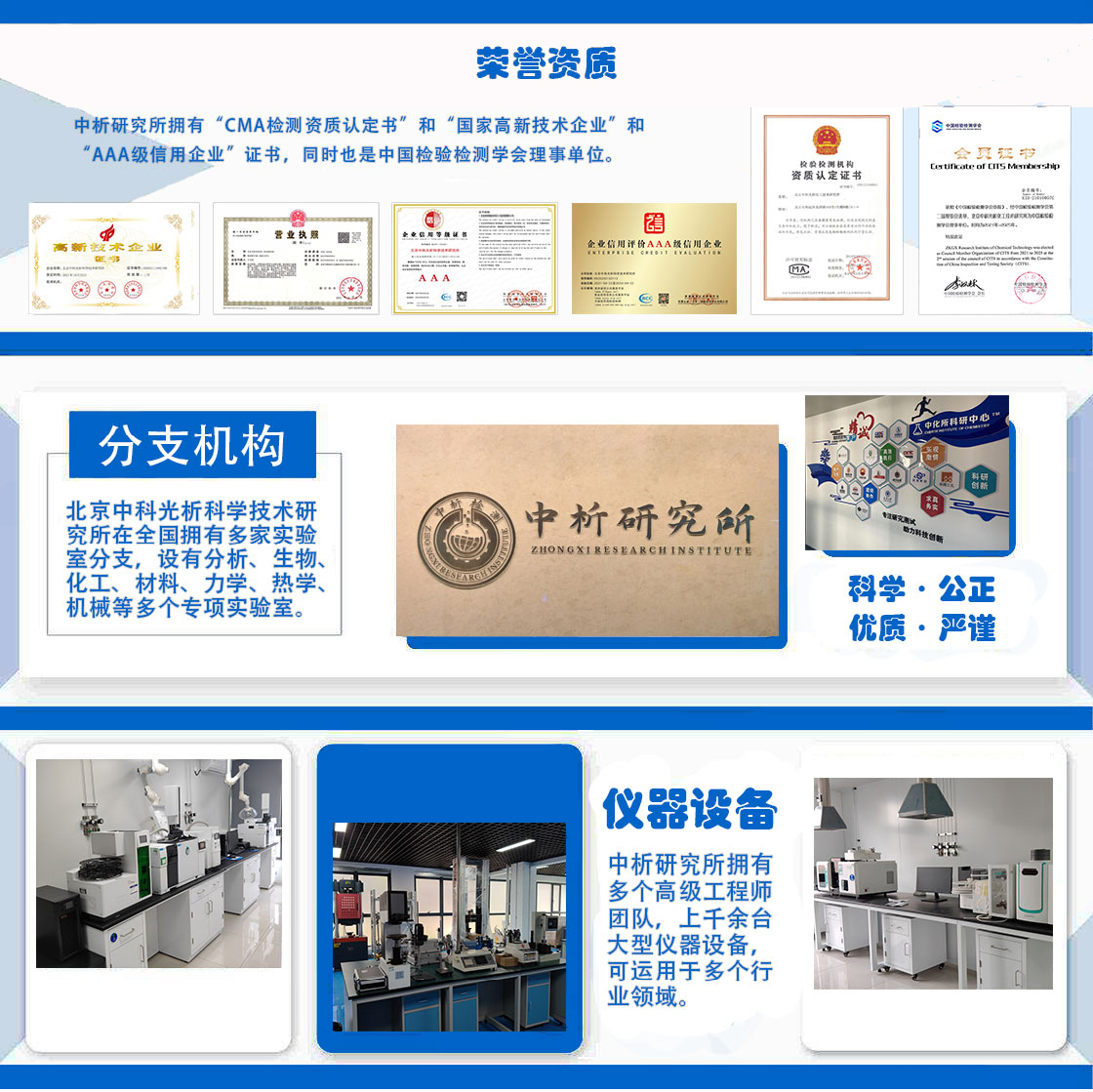
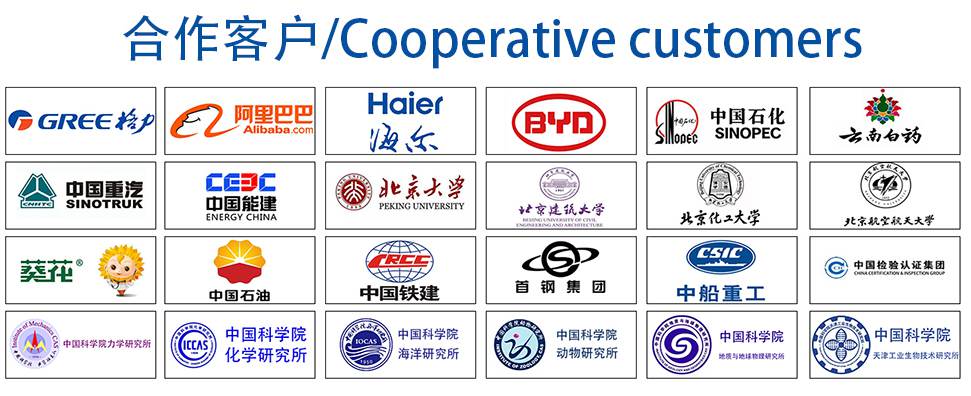