半导体材料检测:高精度制造的核心保障
在5G通信、人工智能和新能源技术的推动下,半导体材料已成为现代工业的"基础粮食"。从单晶硅到第三代半导体材料氮化镓(GaN)、碳化硅(SiC),这些材料的微观特性直接决定芯片性能、能耗和可靠性。半导体材料检测作为贯穿研发、生产到质量管控的核心环节,通过系统化的物理化学分析手段,可精确评估材料的晶体结构、电学特性及缺陷分布,为微纳级半导体器件的制造提供关键数据支撑。据统计,领先的芯片制造企业每年投入超过20%的研发预算用于材料检测技术升级,以确保材料参数波动控制在原子级精度范围内。
关键检测项目体系
1. 晶体结构分析
采用X射线衍射(XRD)和透射电子显微镜(TEM)检测晶格常数、晶向排列及多晶结构。例如在12英寸硅晶圆检测中,要求晶格畸变率低于0.01%,XRD的角分辨率需达到0.001°才能捕捉纳米级晶格缺陷。
2. 电学性能测试
通过四探针法、霍尔效应测试系统测量电阻率、载流子浓度和迁移率。针对宽禁带半导体材料,需要构建1000V以上的高压测试环境,配合低温恒温装置实现-196℃至300℃的全温域特性分析。
3. 表面污染物检测
运用飞行时间二次离子质谱(TOF-SIMS)和全反射X射线荧光光谱(TXRF)进行表面金属污染分析,检测灵敏度可达1E8 atoms/cm²级别。在齐全制程中,要求钠、铁等金属污染物浓度低于0.1ppb。
4. 缺陷表征技术
结合激光扫描共焦显微镜和阴极荧光(CL)光谱技术,实现位错、层错等晶体缺陷的三维定位。对于碳化硅功率器件,必须将微管缺陷密度控制在5个/cm²以下才能满足高压应用需求。
5. 薄膜特性评估
采用椭偏仪和X射线反射法(XRR)测量薄膜厚度与折射率,原子力显微镜(AFM)检测表面粗糙度。在7nm制程的High-K介质层检测中,要求厚度均匀性误差≤0.3Å,表面粗糙度Ra<0.2nm。
6. 热学性能测试
通过激光闪射法测量热导率,结合热机械分析仪(TMA)评估热膨胀系数。氮化铝陶瓷基板要求热导率≥170W/m·K,与芯片的热膨胀系数匹配度误差需控制在0.5ppm/℃以内。
检测技术发展趋势
随着半导体器件向三维堆叠结构发展,检测技术正朝着多参数联检方向突破。最新研发的等离子体质谱-俄歇电子能谱联用系统,可在真空环境下同步完成成分分析和深度剖析。人工智能算法的引入使缺陷识别准确率提升至99.7%,检测效率提高3倍以上。未来,基于量子传感的原子级表征技术和在线监测系统将重构半导体质量控制体系。
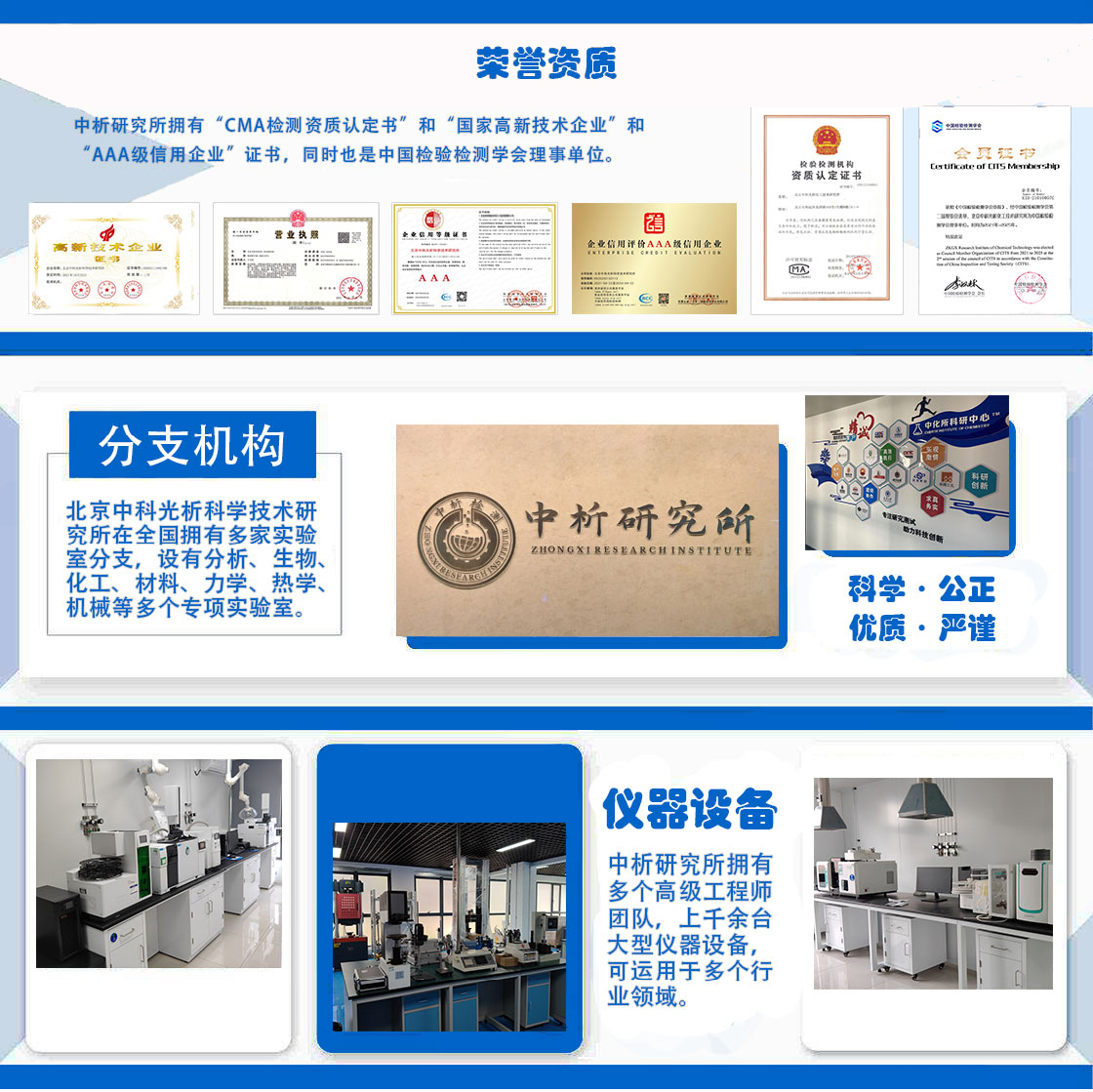
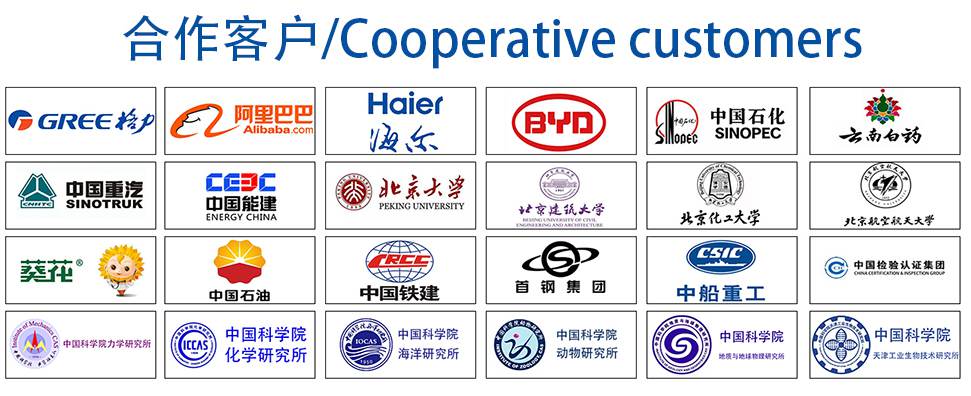