规格尺寸检测的核心价值与应用场景
规格尺寸检测是产品制造过程中质量管控的核心环节,通过精确测量零部件的几何参数验证其是否符合设计标准。在机械制造、汽车工业、航空航天、电子元件等精密加工领域,尺寸误差超过允许范围可能导致装配失效、性能下降甚至安全隐患。现代检测技术已实现从传统卡尺量具到三维光学扫描的全方位覆盖,检测项目包含长度、直径、角度、形位公差等20余项关键指标,部分高端设备检测精度可达0.001mm级。企业通过建立完整的尺寸检测体系,可有效降低产品不良率30%-50%,同时满足ISO9001、IATF16949等国际质量体系认证要求。
基础几何参数检测体系
常规检测项目包含外径、内径、长度、高度等基础尺寸测量,采用千分尺、高度规等精密量具完成。对于复杂曲面工件,需使用三坐标测量机(CMM)进行三维坐标采集,平均单件检测时间可缩短至5-8分钟。特殊行业如轴承制造需进行滚道曲率半径检测,误差需控制在±0.005mm范围内。
形位公差综合评估方案
平面度、圆度、圆柱度等形状公差检测采用激光干涉仪与电子水平仪组合方案,工业机器人搭载接触式测头可实现自动化测量。位置公差检测重点包含同轴度、对称度、位置度等项目,采用影像测量仪配合专业分析软件,可自动生成公差带分布图,检测效率较传统方式提升4倍。
三维尺寸逆向验证技术
针对复杂曲面产品,应用蓝光扫描仪或CT扫描技术获取完整三维点云数据,通过Geomagic等软件进行CAD模型对比分析。该技术可一次性完成5000+特征点比对,精确识别0.02mm级尺寸偏差,特别适用于模具修正和首件验证场景。
智能化检测系统集成
最新智能检测单元集成机器视觉与AI算法,通过深度学习自动识别测量特征点,检测速度可达120件/小时。系统配备SPC统计过程控制模块,实时监控尺寸波动趋势,当CPK值低于1.33时自动触发预警,帮助企业实现预防性质量管控。
检测报告与数据分析
专业检测机构出具的检测报告需包含实测数据、公差带分布、CP/CPK指标等核心要素。通过Minitab进行六西格玛分析,可准确识别工序能力瓶颈。典型案例如某汽车零部件企业通过优化检测流程,将转向节关键尺寸CPK值从0.89提升至1.67,年度质量成本降低280万元。
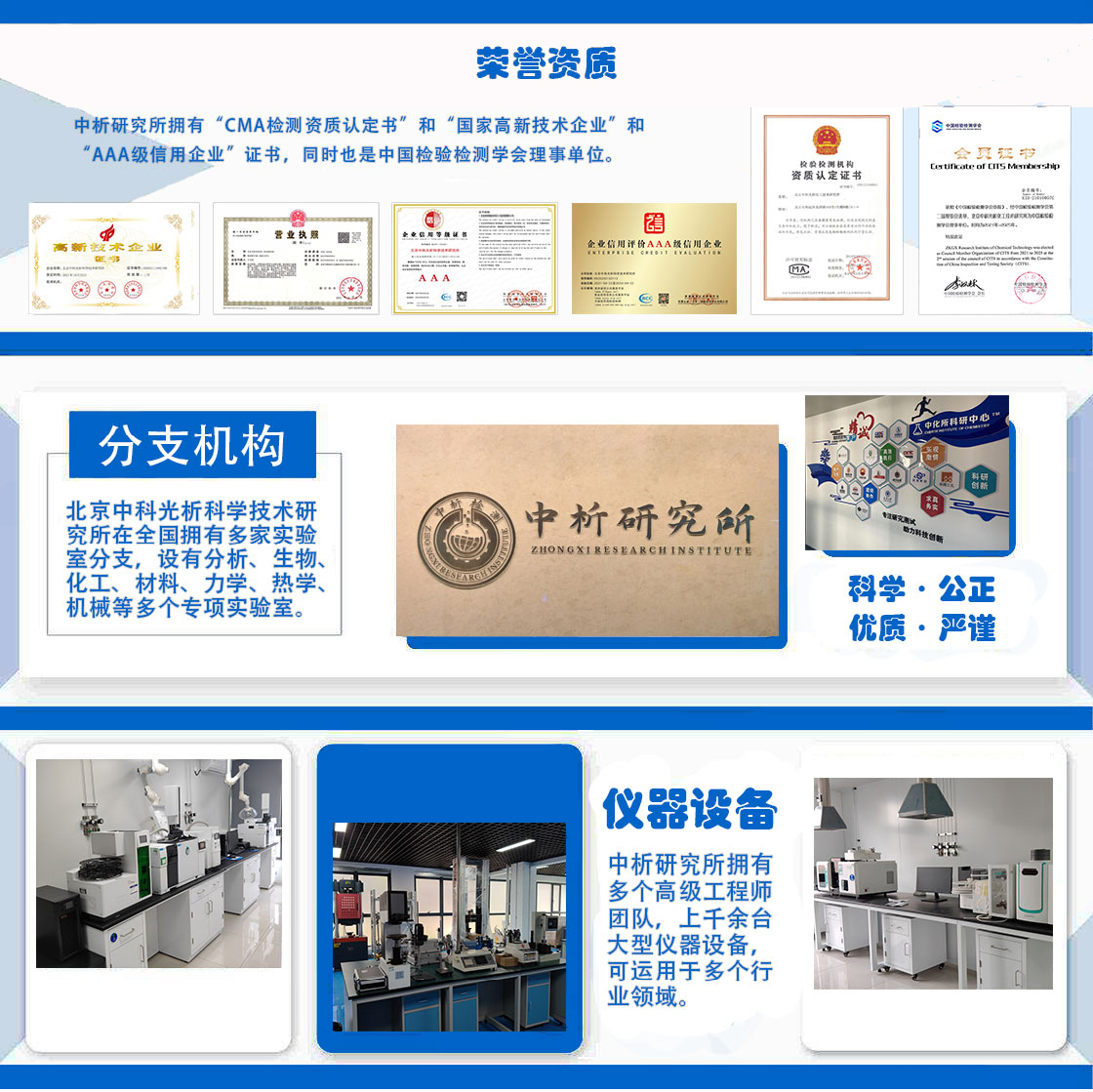
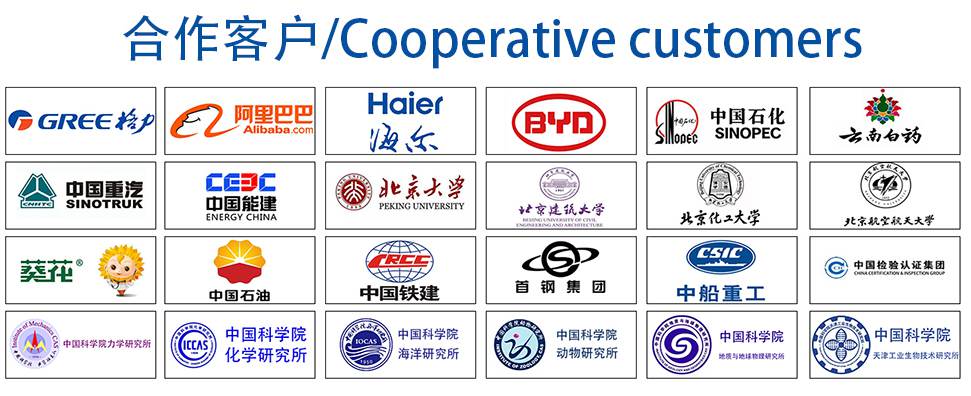