石油专用管材检测的重要性与核心内容
石油专用管材包括油管和套管,是石油天然气钻采过程中保障井筒完整性、实现油气输送的核心部件。由于长期承受高压、高温、腐蚀性介质及复杂机械载荷的极端工况,其质量直接关乎油气田开发安全与生产效率。据行业统计,约30%的井下事故与管材失效相关。因此,建立系统化的检测体系,覆盖出厂检验、服役前检测及周期性评估,成为石油工业质量控制的重点环节。
石油管材关键检测项目解析
针对油管和套管的检测内容主要分为以下几大模块:
1. 材料成分与力学性能检测
通过光谱分析仪检测合金元素含量(如Cr、Mo、Ni等),结合拉伸试验机完成抗拉强度、屈服强度、延伸率测试。采用夏比冲击试验评估低温韧性,维氏硬度计检测表面及截面硬度分布,确保满足API SPEC 5CT标准要求。
2. 几何尺寸与形位公差检测
使用激光测径仪精确测量外径、内径、壁厚等基础尺寸,采用三维轮廓扫描仪检测管体直线度、椭圆度及接箍端面垂直度。螺纹参数检测需运用专业量规,验证锥度、螺距、齿高等指标符合API 5B规范。
3. 无损检测技术应用
采用超声波探伤(UT)检测管体分层、夹杂等内部缺陷;漏磁检测(MFL)识别表面裂纹;涡流检测(ECT)发现微小表面缺陷。对于特殊工况管材,需进行全管体自动超声检测(AUT)及射线检测(RT)复合验证。
4. 螺纹密封性能试验
通过气密封试验台进行高压气密性测试,模拟井下压力条件下检测螺纹连接的泄漏率。采用扭矩-位置监测系统分析上卸扣过程的力学特性,结合接触应力分布测试验证螺纹结构设计的可靠性。
5. 腐蚀与服役性能评估
开展模拟工况的SSC(硫化物应力开裂)试验、HIC(氢致开裂)试验及CO₂腐蚀速率测试。利用高温高压反应釜进行动态腐蚀实验,结合金相显微镜分析微观组织变化,建立材料耐蚀性分级评价体系。
检测技术发展趋势
随着智能化检测设备的普及,在线自动检测系统可实现每分钟40米的高速检测,AI图像识别技术使缺陷检出率提升至99.5%。数字孪生技术的应用,可建立管材全生命周期数据库,为预防性维护提供数据支撑。未来检测将向多参数融合分析、智能预警方向发展,为油气田安全高效开发提供更强保障。
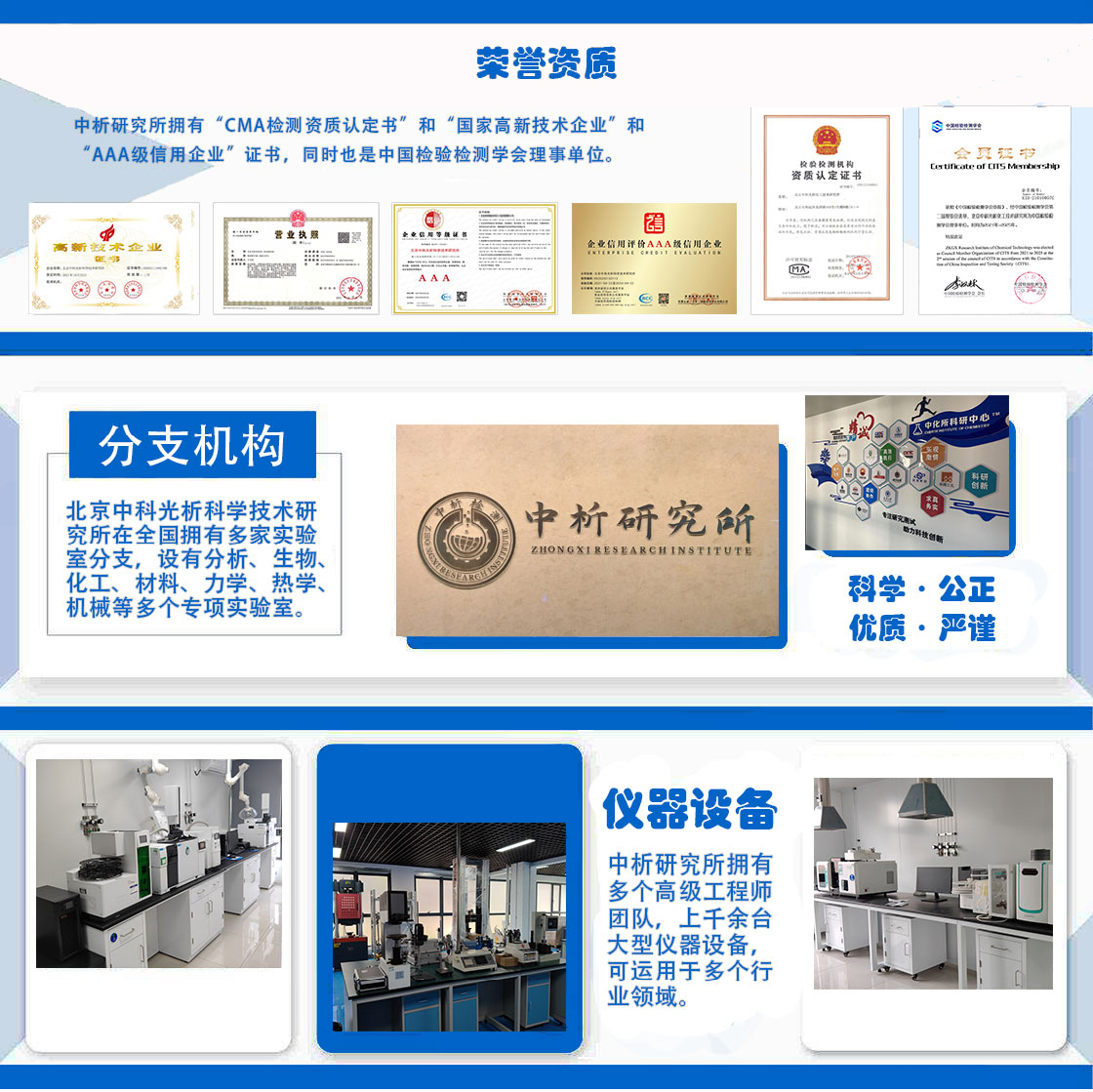
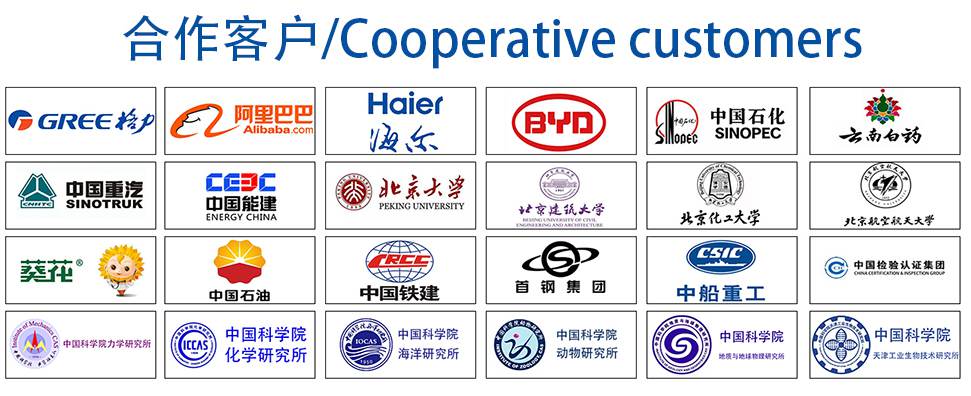