抓手位置及棺盖互换性检测的重要性
在自动化生产线及精密装配领域,抓手位置精度和棺盖互换性是保障产品密封性、安全性和生产效率的核心指标。抓手作为机械臂或自动化设备的关键执行部件,其定位准确性直接影响物料的抓取、搬运及装配质量;而棺盖互换性则决定了不同批次或型号的棺盖与棺体之间的适配程度,尤其在医疗、殡葬等行业中,严苛的密封要求使该检测项目尤为重要。通过系统化的检测流程,可有效避免因位置偏差或尺寸误差导致的装配失败、泄漏风险或设备磨损,从而提升产品合格率并降低生产成本。
抓手位置精度检测项目
抓手位置检测主要包括静态定位精度与动态重复定位精度两项核心内容。静态检测通过激光跟踪仪或高精度标定工具,测量抓手在指定坐标点的实际位置与理论值的偏差,通常要求误差小于±0.1mm。动态检测则模拟实际工作场景,连续多次执行抓取动作并记录位移数据,评估其重复定位稳定性。此外,还需检测抓手的夹持力均匀性、角度偏移及振动幅度,确保其在高速运行中仍能保持可靠性能。
棺盖互换性检测方法与标准
棺盖互换性检测需从尺寸公差、密封匹配度及材质兼容性三方面展开。首先使用三坐标测量仪(CMM)对棺盖与棺体的接口尺寸进行全尺寸扫描,比对设计图纸的公差范围;其次通过气密性测试仪施加压力,检测闭合状态下的泄漏率是否符合行业标准(如ISO认证要求)。针对不同材质(金属、木材、复合材料),还需进行环境模拟测试,验证温度、湿度变化对互换性的影响,避免因热胀冷缩导致的结构变形。
自动化检测技术的应用
现代检测体系中,机器视觉与物联网(IoT)技术已广泛应用于该项目。例如,采用高分辨率工业相机配合AI算法,实时分析抓手运动轨迹并自动校正偏移;通过RFID标签记录每批次棺盖的检测数据,实现全生命周期追溯。此外,力反馈传感器与自适应控制系统可动态调整夹持参数,确保不同型号棺盖的快速切换与精准适配,显著提升检测效率与一致性。
常见问题与解决方案
典型问题包括抓手导轨磨损导致的定位漂移、棺盖螺纹孔位加工误差引发的密封失效等。解决方案涵盖定期校准检测设备、采用耐磨涂层延长机械部件寿命,以及建立统计过程控制(SPC)体系提前预警生产异常。对于高精度要求的场景,推荐引入闭环反馈系统,实现实时纠偏与工艺参数优化。
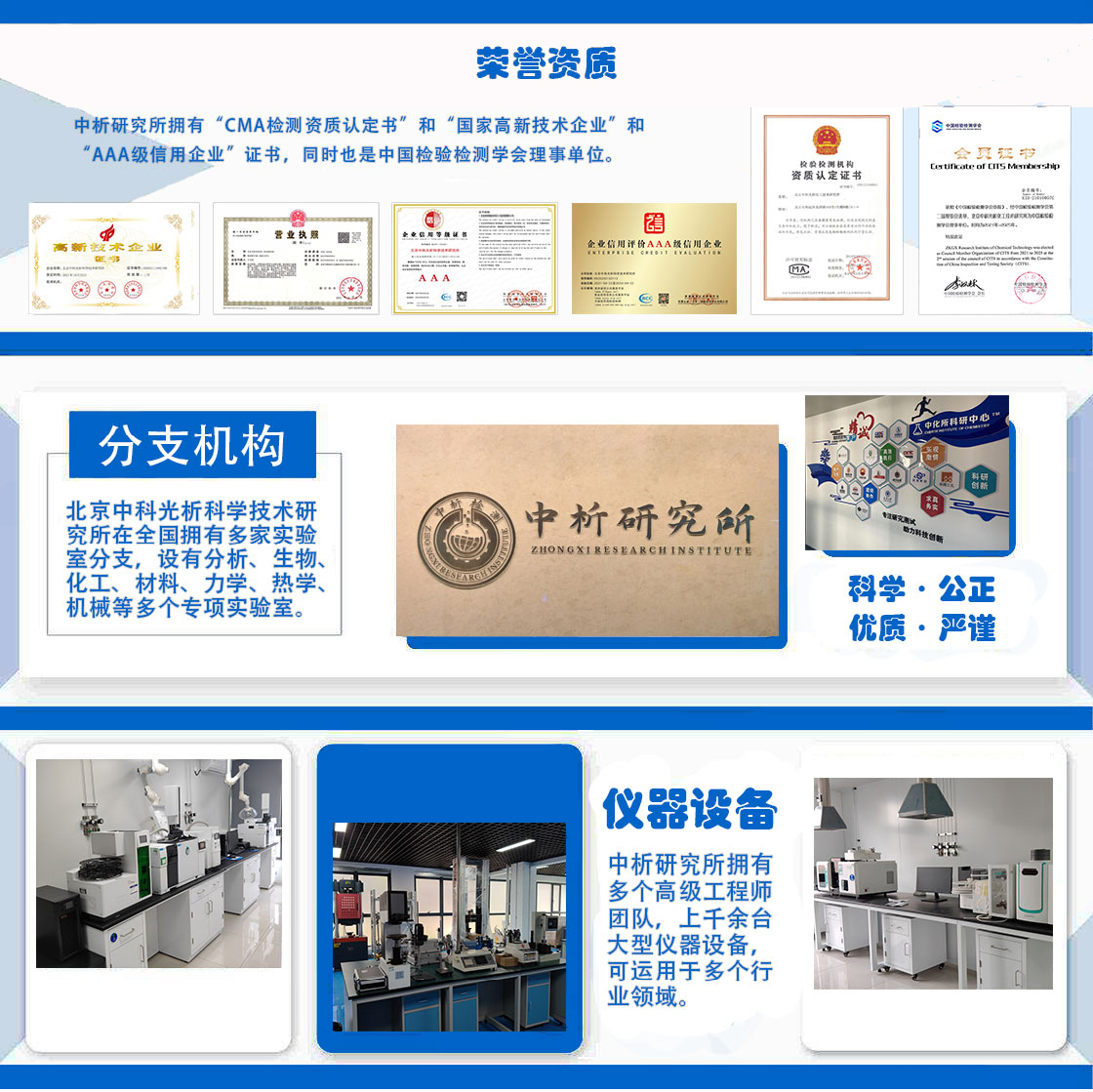
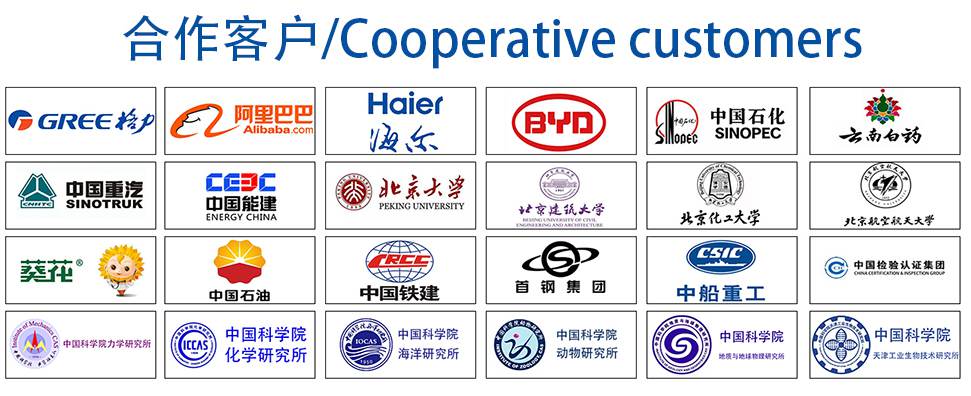