铸造焦炭检测的重要性及检测项目解析
铸造焦炭作为冶金铸造行业的重要原料,其质量直接影响冲天炉熔炼效率、铁水温度及铸件成品质量。根据GB/T 1996-2017《冶金焦炭》和GB/T 8729-2017《铸造焦炭》标准要求,专业检测机构需通过系统性检测项目对铸造焦炭的物理化学性能进行全面评估。完整的检测流程能够确保焦炭具备适宜的发热量、反应活性及机械强度,避免因原料不合格导致的铸件气孔、缩松缺陷或炉况异常,对降低生产成本、提升铸造工艺稳定性具有重要意义。
核心检测项目体系
1. 化学成分分析
采用电感耦合等离子体光谱仪(ICP)和碳硫分析仪进行检测,重点指标包括: - 固定碳含量(≥85%) - 挥发分(≤1.5%) - 硫分(≤0.6%) - 磷含量(≤0.03%) 其中硫磷元素的严格控制可避免铸件脆性增加,固定碳含量直接影响发热效率。
2. 物理性能检测
通过转鼓试验机和筛分系统完成关键测试: - 粒度分布(>80mm占比检测) - 抗碎强度(M40值≥85%) - 耐磨强度(M10值≤7%) - 真密度(1.8-2.1g/cm³) 合理的粒度配比可保证炉内透气性,机械强度指标关乎运输破碎率和炉内热态强度。
3. 反应特性检测
使用焦炭反应性测定装置,按照GB/T 4000-2017标准测试: - 反应性指数(CRI,控制范围20-30%) - 反应后强度(CSR,要求≥65%) 这两项指标反映焦炭在高炉内的抗溶损能力,直接影响炉况稳定性和燃料消耗率。
4. 热性能检测
包括: - 发热量(≥28MJ/kg) - 灰熔点(ST>1350℃) - 热膨胀系数 高热值保证熔炼效率,高灰熔点可防止结渣影响炉体寿命。
5. 微观结构检测
采用扫描电镜(SEM)和X射线衍射分析: - 气孔结构分布 - 显微组分构成 - 各向异性指数 微观结构直接影响焦炭的反应活性和热传导性能。
检测技术发展现状
现代检测结合了智能光谱分析、工业CT扫描和热重-质谱联用技术,实现了从宏观指标到微观结构的全面解析。第三方检测机构通过建立焦炭质量数据库,结合生产工艺参数进行大数据分析,可为铸造企业提供原料选型、配比优化等增值服务。定期检测建议每批次原料入库前实施基础检测,每季度开展全项检测,确保生产过程的持续可控。
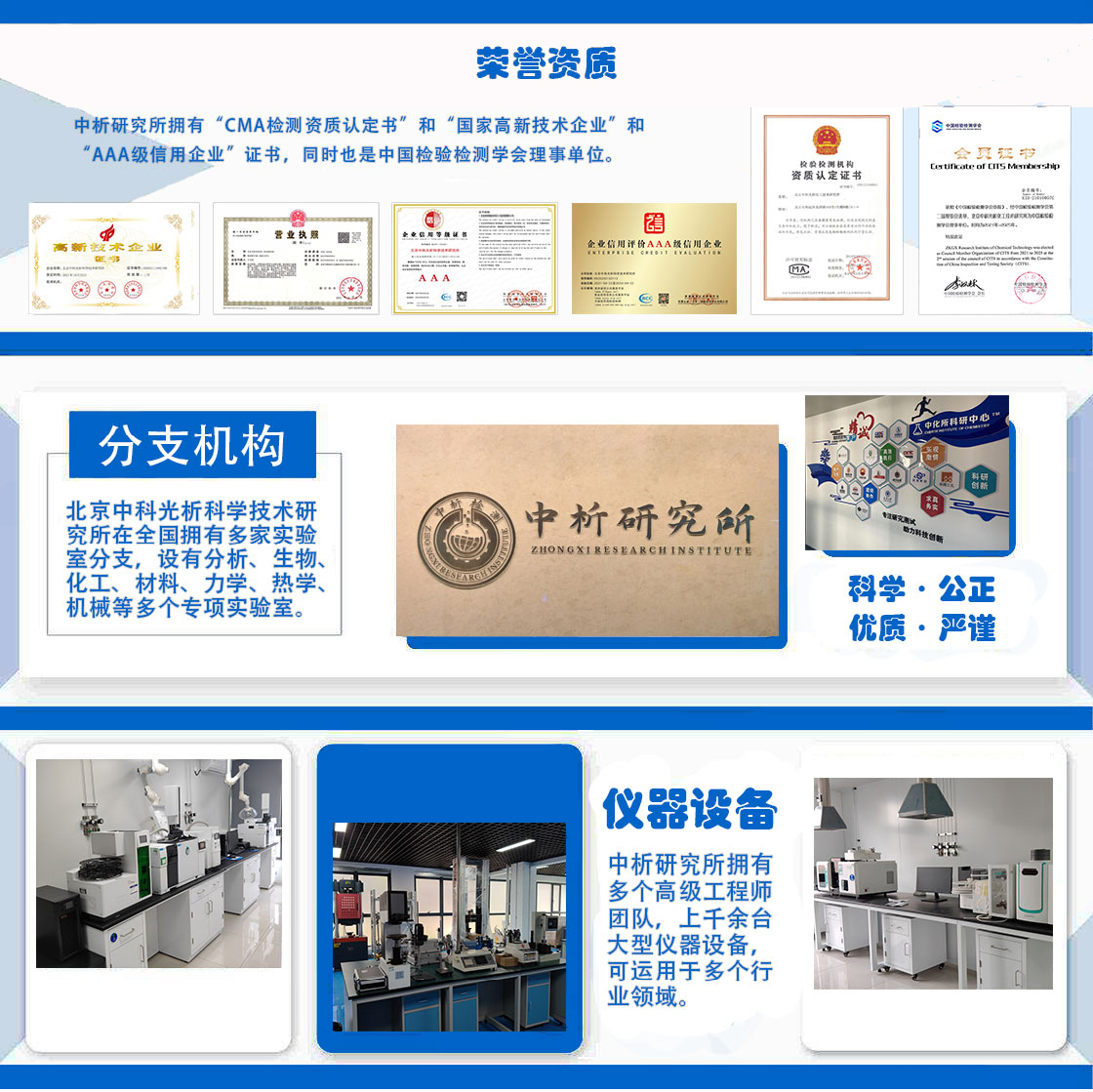
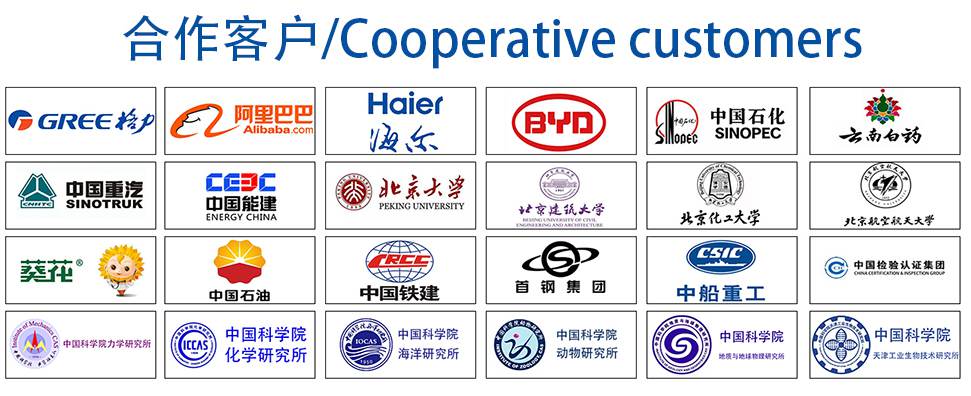