液态食品包装用吹塑聚丙烯容器检测的重要性
随着食品工业的快速发展,吹塑聚丙烯(PP)容器因其轻便、耐化学腐蚀、可高温灭菌等特性,成为液态食品(如牛奶、果汁、调味品等)的主流包装选择。然而,包装材料的性能直接关系到食品的安全性、保质期及运输稳定性。为确保产品符合国家标准《GB 4806.7-2016 食品安全国家标准 食品接触用塑料材料及制品》的要求,需对吹塑聚丙烯容器进行系统性检测,涵盖物理性能、化学安全性和微生物指标等多维度测试。
核心检测项目与技术要求
1. 物理性能检测
• 密封性测试:通过气密性检测仪模拟运输压力,验证容器封口处是否泄漏,确保内容物无污染风险。
• 抗压强度与跌落性能:评估容器在堆码运输或意外跌落时的抗变形能力,通常要求满载状态下1.2米高度自由跌落无破裂。
• 壁厚均匀性检测:利用超声波测厚仪检查容器各部位厚度,避免因局部过薄导致的渗漏或机械强度不足。
2. 化学安全性检测
• 总迁移量测试:模拟水、乙醇、酸性等食品环境下,容器中可迁移物质的总量是否超出标准限值(≤10mg/dm²)。
• 重金属及特定物质筛查:检测铅、镉等重金属含量,以及壬基酚、双酚A等环境激素残留。
• 溶剂残留分析:通过气相色谱法测定甲苯、正己烷等生产过程中可能残留的挥发性有机物。
3. 微生物指标与灭菌验证
• 商业无菌检测:对灭菌后的容器进行培养实验,确保无致病菌及腐败微生物存活。
• 内表面微生物限度:对非灭菌型容器检测菌落总数及大肠菌群,防止二次污染。
生产工艺与检测标准的协同优化
企业需结合《GB/T 13508-2011 聚乙烯吹塑容器》及行业实际需求,建立从原料入厂到成品出厂的全流程质控体系。例如,通过红外光谱(FTIR)验证原料聚丙烯的纯度,并在吹塑成型环节监控温度、压力参数,避免因加工缺陷导致容器性能下降。定期比对国际标准(如FDA 21 CFR 177.1520)可进一步提升产品出口竞争力。
结语
液态食品包装的检测不仅是合规要求,更是企业履行社会责任的重要体现。通过科学严谨的检测手段,可有效降低食品安全风险,延长货架期,同时为消费者提供更高品质的消费保障。随着检测技术的智能化升级(如机器视觉缺陷检测),未来行业将实现更高效、精准的质量控制闭环。
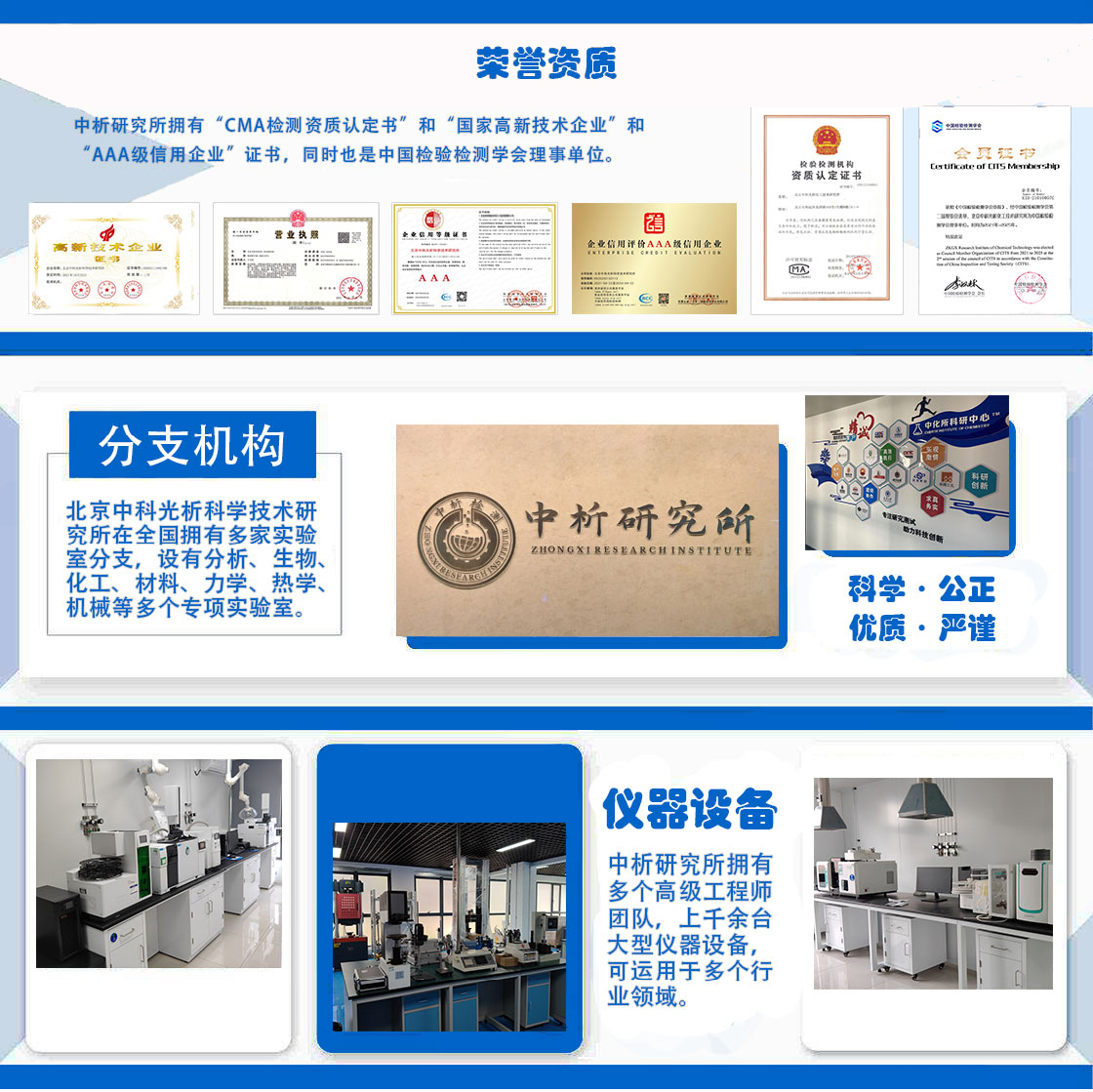
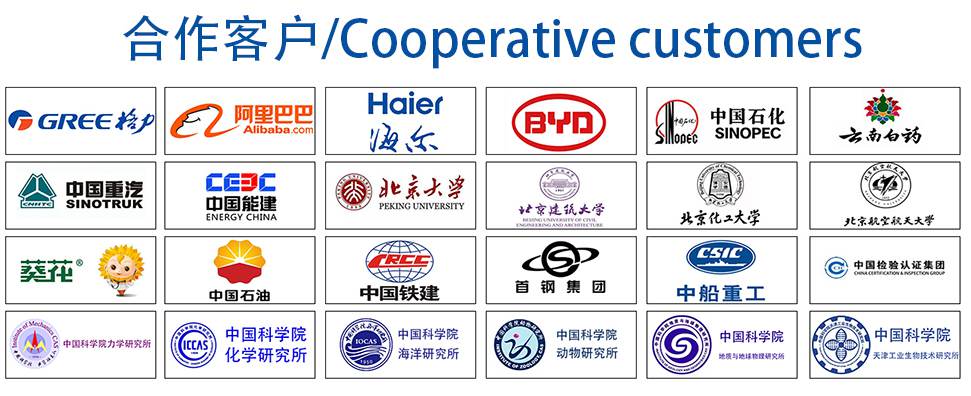