金属材料及焊接检测的重要性
金属材料及其焊接质量是工业制造、建筑工程、航空航天等领域的核心要素。材料的力学性能、化学成分以及焊接接头的完整性直接影响设备的安全性、耐久性和可靠性。随着现代工业对材料性能要求的不断提高,金属材料及焊接检测成为保障产品质量的关键环节。通过科学系统的检测手段,能够有效发现材料缺陷、评估焊接工艺的合规性,并预防因材质或焊接问题引起的设备失效事故。
金属材料检测的关键项目
1. 化学成分分析:通过光谱分析、化学滴定等方法,测定金属材料中碳、硫、锰等元素的含量,确保其符合国家标准或行业规范,避免因成分偏差导致材料性能下降。
2. 力学性能测试:包括拉伸试验、冲击试验、硬度测试等,评估材料的抗拉强度、延展性、韧性及耐磨性,为材料选型提供数据支持。
3. 无损检测(NDT):利用超声波检测(UT)、射线检测(RT)、磁粉检测(MT)等技术,在不破坏材料的前提下识别内部裂纹、气孔、夹杂等缺陷。
焊接质量检测的核心内容
1. 焊缝外观检查:通过目视或放大镜观察焊缝的成形质量,检测咬边、未熔合、焊瘤等表面缺陷。
2. 焊接接头力学性能测试:对焊接试样进行弯曲试验、拉伸试验和冲击试验,验证接头的强度与韧性是否满足设计要求。
3. 金相分析:通过显微镜观察焊缝及热影响区的显微组织,评估焊接工艺对材料微观结构的影响,发现晶间腐蚀、过热等潜在问题。
4. 渗透检测(PT)与涡流检测(ET):用于检测焊缝表面及近表面的微小缺陷,尤其适用于非铁磁性材料的检验。
综合检测技术的应用趋势
随着智能化技术的普及,金属材料及焊接检测逐渐向自动化、数字化方向发展。例如,基于人工智能的缺陷识别系统可快速分析无损检测图像,提升检测效率;三维扫描技术能够精确测量焊接结构的尺寸与形位公差。未来,多技术融合的检测方案将成为行业主流,为复杂工况下的质量保障提供更全面的支持。
总结:金属材料及焊接检测通过多维度、多方法的综合评估,确保从原材料到成品全流程的质量可控。只有严格执行检测标准,才能有效降低工程风险,推动制造业的高质量发展。
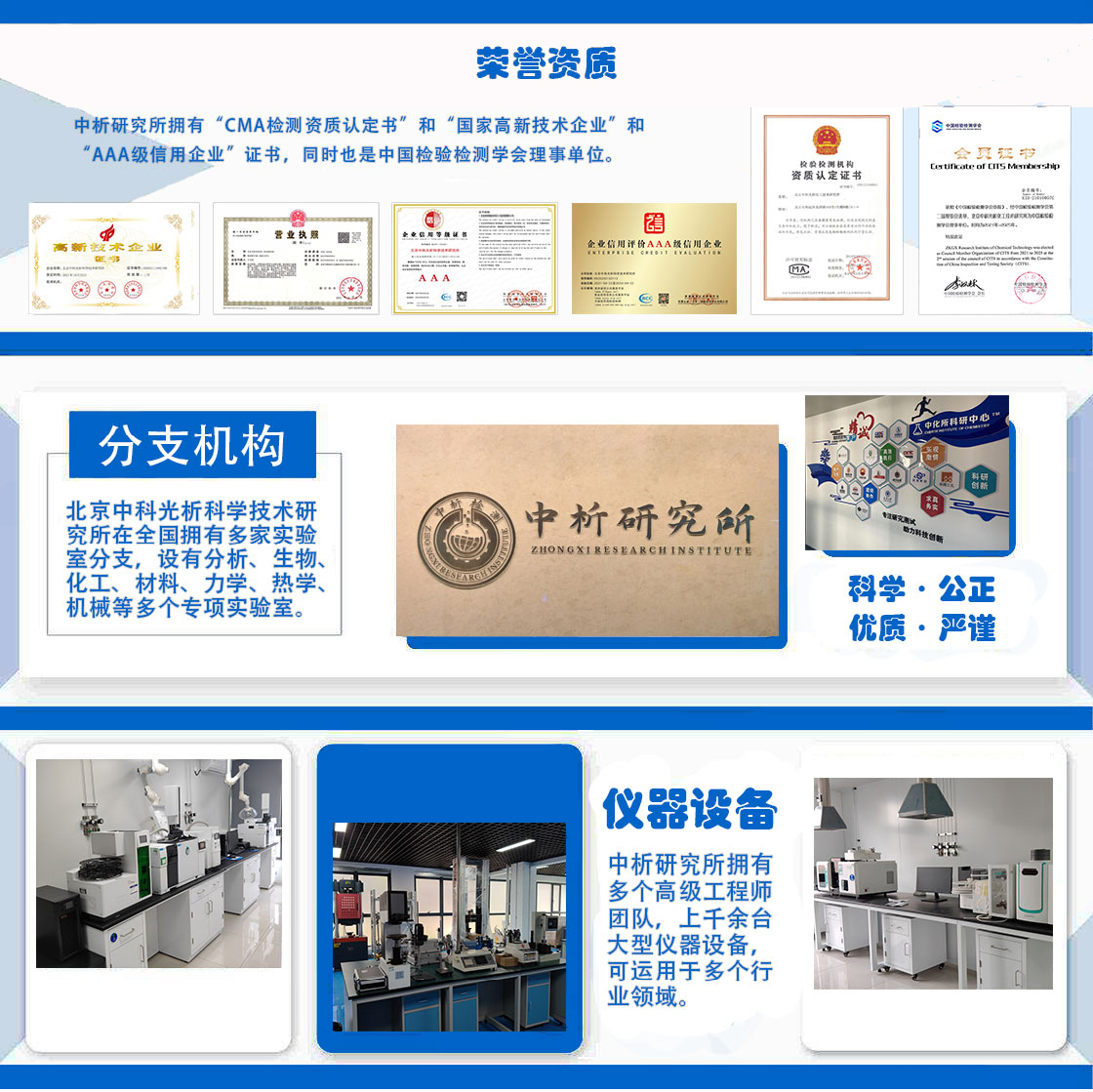
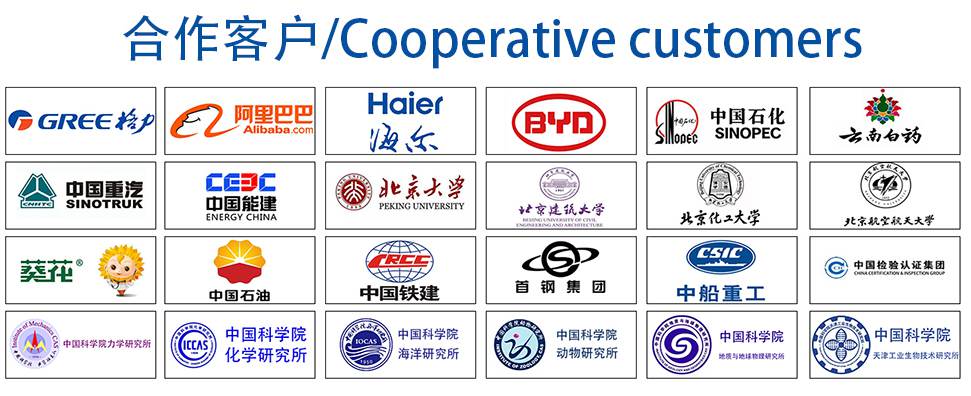