数控机床检测:保障精密制造的核心环节
在齐全制造业中,数控机床作为精密加工的核心装备,其性能直接影响产品质量和生产效率。据统计,因机床精度偏差导致的废品率可高达15%,而定期进行系统化检测可将设备故障率降低60%以上。数控机床检测不仅是维护设备稳定运行的必要措施,更是确保加工精度、延长设备寿命的关键技术手段,涉及几何精度、动态性能、电气系统、控制软件等20余项关键指标的全面验证。
核心检测项目体系解析
1. 几何精度检测
通过激光干涉仪、球杆仪等专业设备,对机床的定位精度、重复定位精度进行微米级测量。重点检测X/Y/Z轴直线度、垂直度偏差,主轴径向跳动(需≤0.003mm),工作台平面度(应控制±0.01mm/m²)等基础几何参数。其中,反向间隙检测需采用双向循环测量法,确保各轴向传动系统间隙值符合ISO 230-2标准。
2. 动态性能检测
使用振动分析仪和加速度传感器,评估机床在高速加工状态下的稳定性。主要包括:主轴在12000rpm下的温升测试(温升应≤25℃)、各轴向加速度达0.8G时的振动频谱分析、快速移动速度30m/min时的动态跟踪误差监测。特别关注谐振频率点,避免发生切削颤振现象。
3. 电气系统检测
采用数字万用表和示波器对供电系统进行深度检测:三相电压平衡度(偏差≤3%)、伺服电机电流波动(峰峰值≤额定值10%)、电磁兼容性测试(辐射干扰≤30dBμV/m)。同时检测冷却系统压力(4-6bar)、液压站油温(40-60℃)等辅助参数,确保各子系统协调运行。
4. 数控系统功能验证
通过G代码模拟和实际加工测试,验证插补精度、刀具补偿、坐标系转换等关键功能。重点检测圆弧插补轮廓误差(需≤0.015mm)、刀具半径补偿响应延迟(应<2ms)、多轴同步精度(误差≤0.005°)。使用3D扫描仪对比加工件与CAD模型的偏差,建立精度补偿数据库。
智能化检测新趋势
当前行业正推动基于物联网的预测性检测技术,通过在机床关键部位部署200+个传感器,实时采集振动、温度、电流等数据,结合机器学习算法实现精度衰退预测。德国某机床厂应用该技术后,将计划外停机时间减少了75%,刀具寿命预测准确率达92%,标志着数控机床检测进入智能化新阶段。
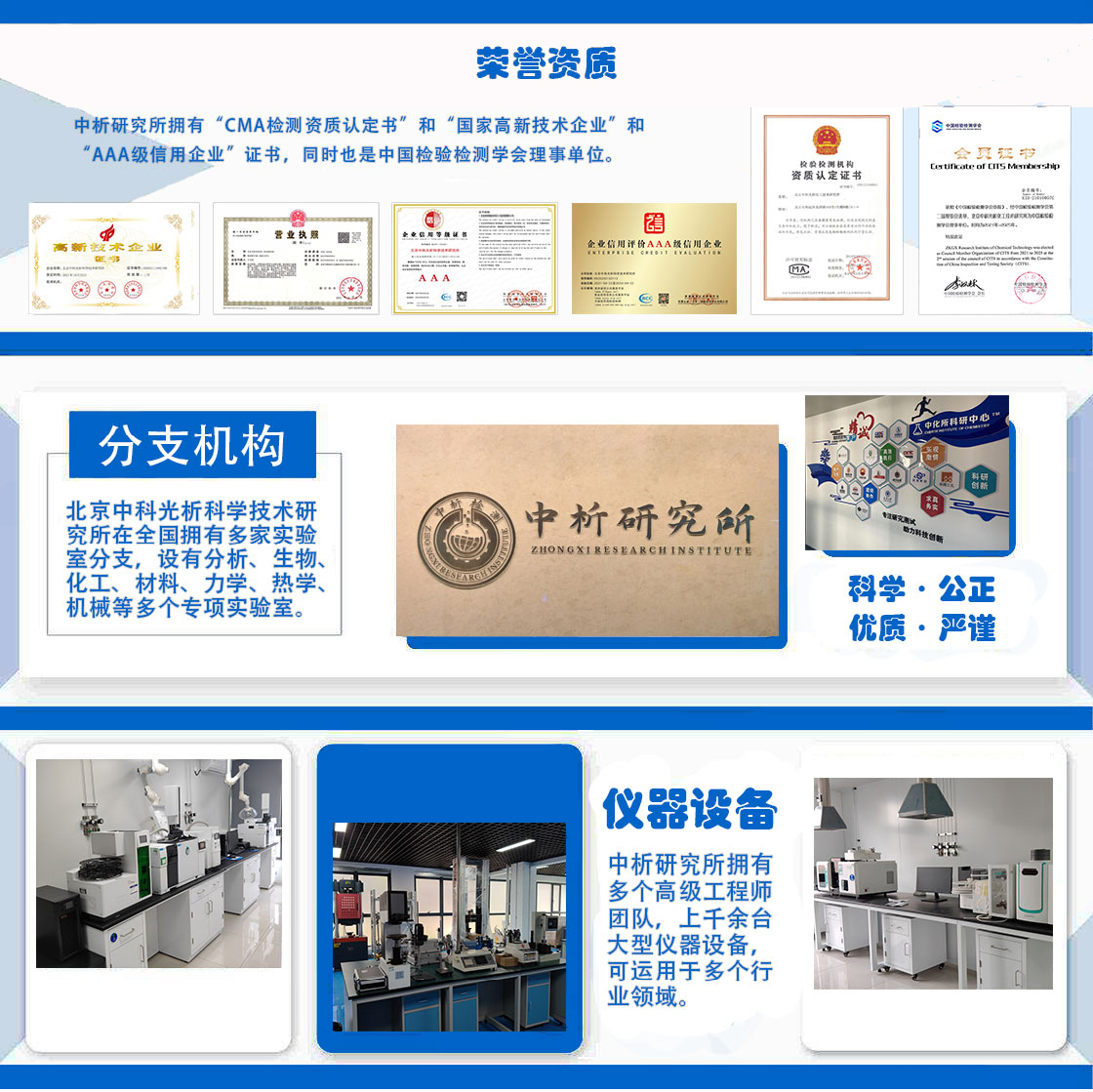
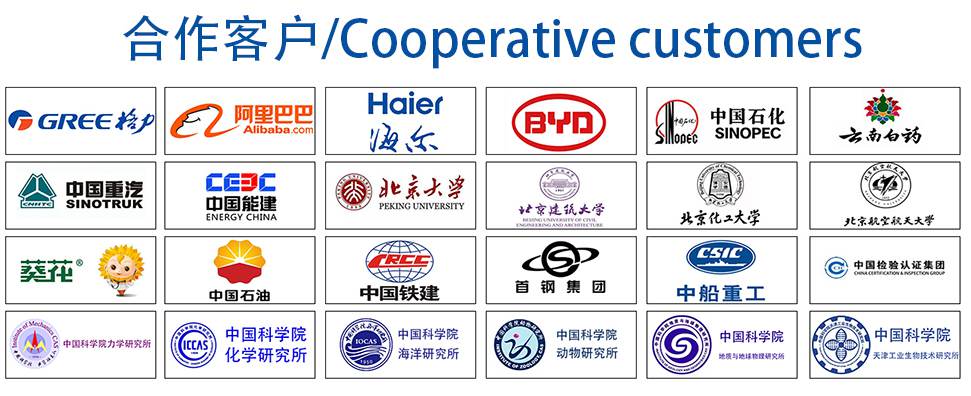