铝及铝合金微观结构检测的重要性与方法
铝及铝合金作为现代工业中广泛应用的重要材料,其性能直接受微观结构的影响。微观结构的检测是优化材料加工工艺、评估材料性能、保障产品质量的核心环节。通过对铝及铝合金的金相组织、晶粒尺寸、相分布等特征的精准分析,可揭示材料在强度、耐腐蚀性、塑性等方面的表现机制,同时为工艺改进和失效分析提供科学依据。
核心检测项目与技术要求
1. 金相组织分析
通过金相显微镜或扫描电子显微镜(SEM)观察材料的晶粒形态、第二相分布及缺陷(如气孔、裂纹)。需依据GB/T 3246.1-2012《铝及铝合金加工制品显微组织检验方法》进行样品制备与评级,重点关注α-Al基体与强化相的协调性。
2. 晶粒度测定
采用截点法或图像分析软件(如Image-Pro)统计晶粒尺寸,参照ASTM E112标准计算晶粒度级别(G值)。细晶组织可提升材料强度,粗晶可能导致疲劳性能下降。
3. 相组成分析
结合X射线衍射(XRD)和能谱仪(EDS)鉴定合金中的θ(Al₂Cu)、β(Mg₂Si)等强化相,定量分析相含量及分布均匀性。这对热处理工艺的优化至关重要。
4. 夹杂物检测
依据GB/T 10561-2005标准,使用高倍显微镜(500×以上)评估氧化物、碳化物等非金属夹杂物的类型、尺寸及分布密度,控制其在三级以内以保证材料纯净度。
齐全检测技术的应用
电子背散射衍射(EBSD)技术可解析晶粒取向和织构演变规律,同步辐射CT能三维重构微观缺陷。近年发展的原位高温显微技术,可实时观测热处理过程中微观结构的动态变化。
检测结果对性能的指导意义
例如,在6系铝合金中发现连续网状分布的β相,提示需要调整固溶处理温度;若7系铝合金晶粒尺寸超差(>100μm),需核查热轧工艺参数。微观结构数据与力学性能测试的关联分析,是制定工艺规范的关键依据。
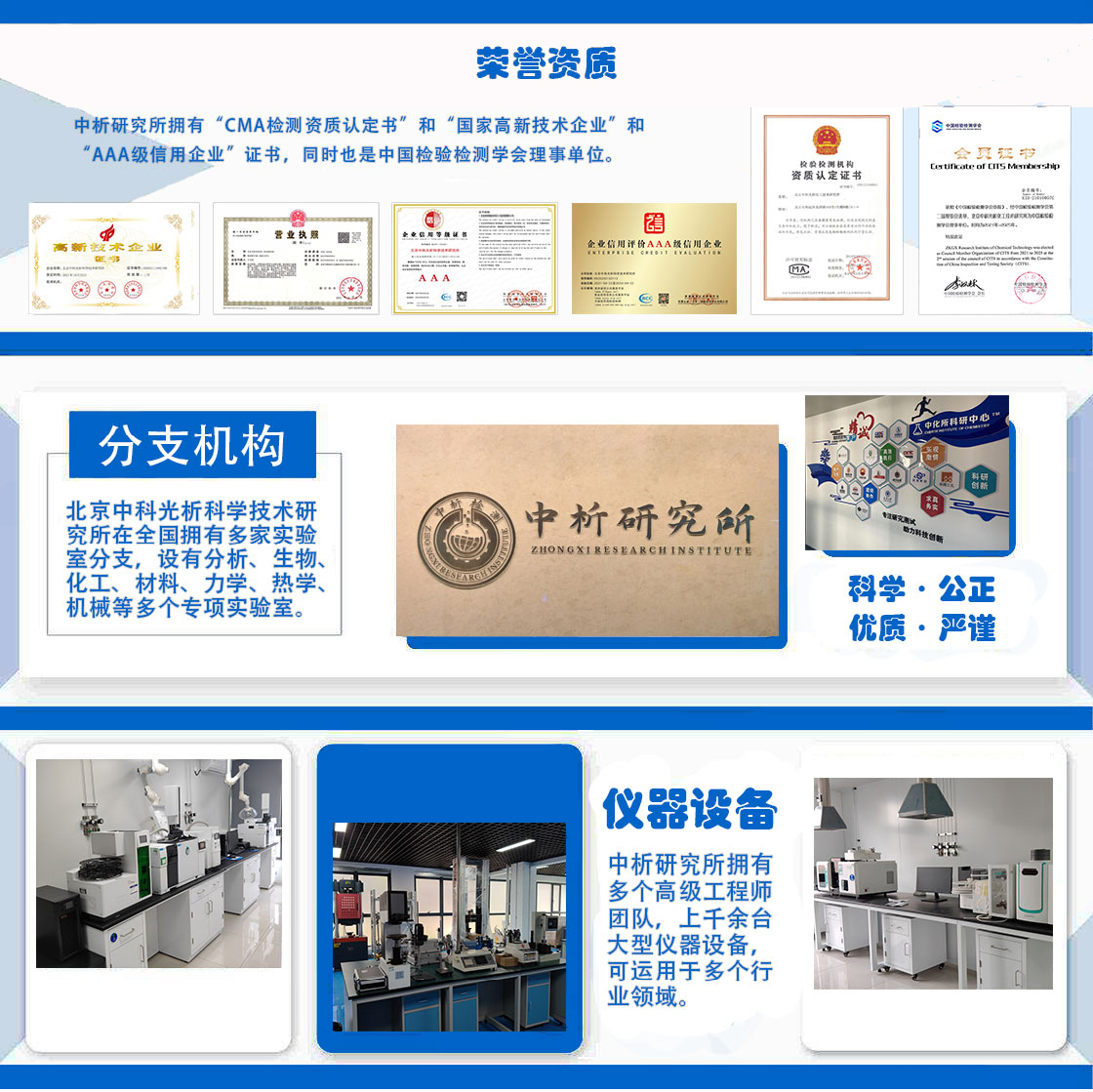
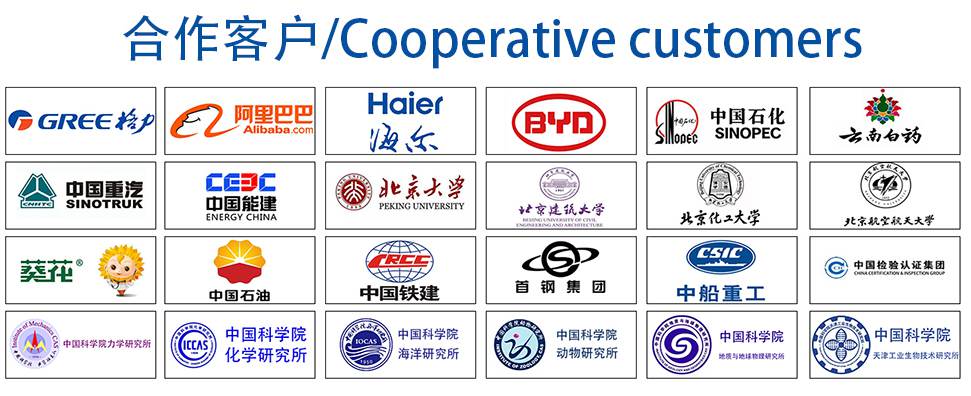