振动源及其周边结构检测的技术要点与实施流程
在现代工业设备维护和建筑结构健康监测领域,振动源及其周边结构的检测已成为保障系统安全运行的核心环节。随着机械系统复杂度提升和精密设备普及,振动问题可能导致轴承磨损、部件疲劳断裂甚至灾难性故障。据统计,约65%的机械故障可通过早期振动异常特征进行预判,这使得振动检测技术从传统的事后维修模式逐步转向预防性维护体系。
一、振动检测项目体系构成
完整的振动检测体系包含三大模块:振动源本体特征检测、传递路径分析和周边结构响应监测。检测项目需覆盖时域、频域和空间域三个维度,典型指标包括振动加速度、速度、位移、频率谱特征、相位关系及模态参数等。国际标准ISO 10816-1规定了不同设备类型的振动限值,为检测结果评价提供基准依据。
二、振动源核心检测项目
针对振动源本体的检测重点包括:
1. 基频振动分析:通过FFT频谱分析识别旋转部件的特征频率,诊断叶轮失衡、轴系不对中等问题
2. 谐波成分检测:发现齿轮啮合频率、轴承故障特征频率等高频振动分量
3. 瞬态冲击监测:捕捉轴承剥落、齿轮断齿等突发性冲击信号
4. 热-振耦合分析:结合红外热成像技术定位异常发热振动源
三、周边结构动态响应检测
周边结构的检测需重点关注:
• 结构共振特性测试:通过锤击法或激振器进行模态分析,识别固有频率和振型
• 振动传递率测量:在设备基座、连接管道等关键节点布置传感器,评估振动能量传递路径
• 应力分布监测:采用动态应变片检测焊缝、螺栓连接处等应力集中区域的动态响应
• 非线性特征识别:分析大振幅振动下的结构刚度变化和接触非线性现象
四、齐全检测技术的综合应用
现代检测系统结合多种技术手段提升诊断精度:
1. 多通道同步采集系统:实现32通道以上振动信号同步采样,相位精度达0.1°
2. 激光多普勒测振仪:非接触式测量分辨率达0.01μm,适用于微型精密器件检测
3. 无线传感器网络:采用LoRa或5G通信技术构建分布式监测系统
4. 数字孪生技术:建立结构动力学虚拟模型进行振动响应预测与验证
五、检测数据分析与决策支持
智能诊断平台通过以下流程实现数据价值转化:
1. 特征提取:采用小波包分解、经验模态分解等算法提取故障敏感特征
2. 状态识别:基于深度学习的卷积神经网络实现故障模式分类,准确率可达95%以上
3. 趋势预测:结合ARIMA时间序列模型预测振动参数演化趋势
4. 决策优化:根据剩余使用寿命预测制定维修策略,实现运维成本降低30%-50%
通过系统性实施振动源及周边结构检测,企业可建立完整的设备健康管理体系。某石化企业应用该技术后,关键机组的非计划停机率下降42%,备件库存成本降低28%,充分验证了振动检测技术的工程价值。未来随着边缘计算和数字孪生技术的深度融合,振动检测将向着智能化、预见性方向持续发展。
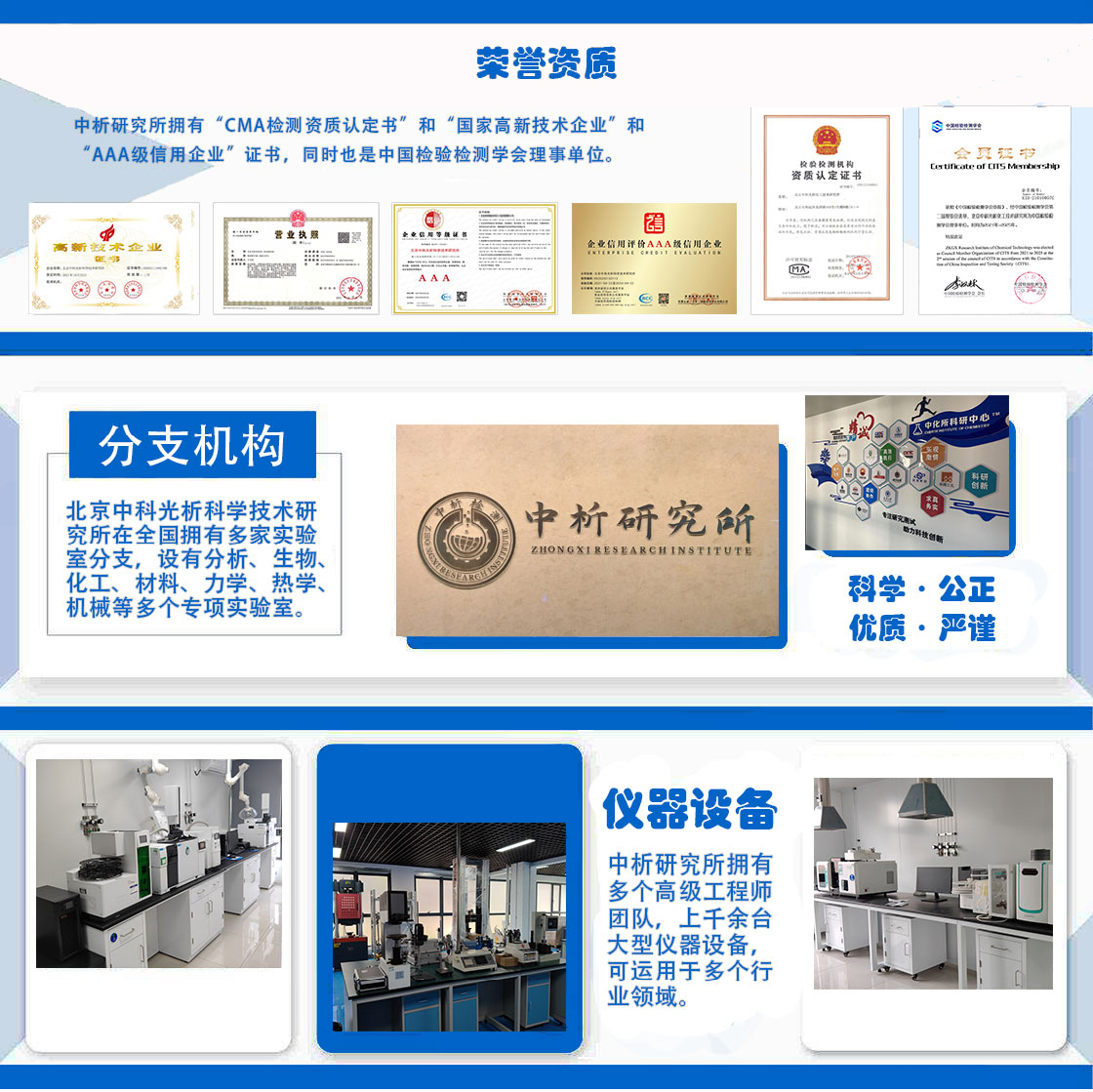
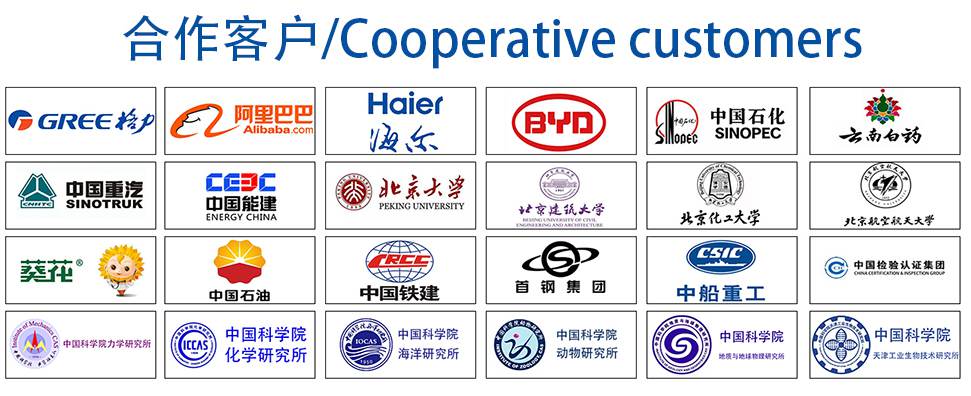