机械零件检测的重要性与核心项目
在现代制造业中,机械零件的质量直接影响设备性能、使用寿命和安全性。机械零件检测作为质量控制的核心环节,通过系统化的测试与分析,确保零件符合设计标准、材料性能达标且满足实际工况需求。随着工业自动化与精密加工技术的飞速发展,检测手段已从传统人工测量逐步转向高精度仪器与智能化系统结合的模式,涵盖尺寸、形位公差、材料性能、表面质量等多个维度。
关键检测项目解析
1. 尺寸与几何精度检测
尺寸精度是机械零件功能匹配的基础,检测内容包括长度、直径、角度等关键参数,使用工具如三坐标测量机(CMM)、千分尺、投影仪等。几何精度则聚焦于形位公差,如同轴度、圆度、平面度等,通过激光扫描或精密传感器实现微米级误差分析。
2. 表面质量检测
表面粗糙度、划痕、裂纹及镀层厚度直接影响零件的耐磨性和抗疲劳能力。粗糙度仪通过触针法或光学干涉法量化Ra值,而工业内窥镜和电子显微镜可探测微观缺陷。特殊涂层零件需通过X射线荧光(XRF)进行成分验证。
3. 材料性能检测
材料的硬度、抗拉强度、冲击韧性等机械性能通过万能试验机、硬度计(如洛氏、维氏)等设备测试。化学成分分析采用光谱仪或质谱仪,确保材料牌号符合标准。金相显微镜用于观察微观组织,判断热处理工艺是否达标。
4. 配合公差与装配验证
关键配合面如轴孔间隙、螺纹啮合需通过极限量规或数字式游标卡尺检验。装配模拟测试则通过扭矩传感器监测螺栓预紧力,或使用3D扫描技术验证多零件组装的整体匹配度。
5. 无损检测(NDT)技术应用
针对内部缺陷,采用超声波探伤(UT)检测气孔、夹杂物,磁粉检测(MT)用于铁磁材料表面裂纹识别,渗透检测(PT)适用于非金属零件。工业CT扫描可三维重构复杂结构内部状态。
6. 动态性能与耐久性测试
高速旋转件如齿轮、轴承需进行动平衡测试以消除离心力偏差。疲劳试验机模拟长期交变载荷下的寿命表现,振动分析仪则监测零件在运行中的谐振频率与异常抖动。
结语
机械零件检测体系的科学构建,不仅需要精准的检测设备,还需结合数字化管理系统(如SPC统计过程控制)实现数据闭环。随着AI视觉识别与物联网技术的渗透,未来检测将向实时化、智能化方向深度演进,为高端装备制造提供更可靠的质量保障。
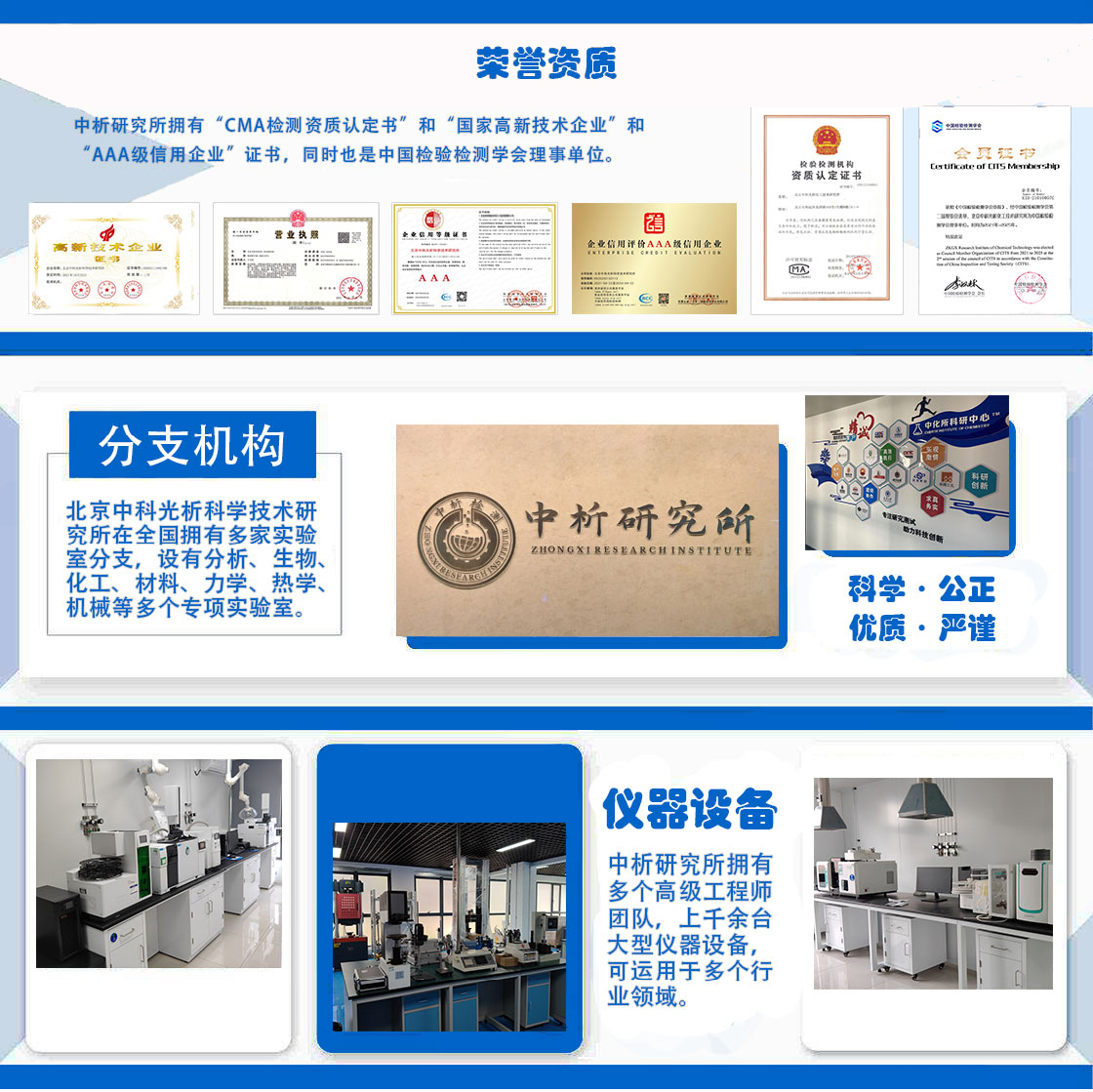
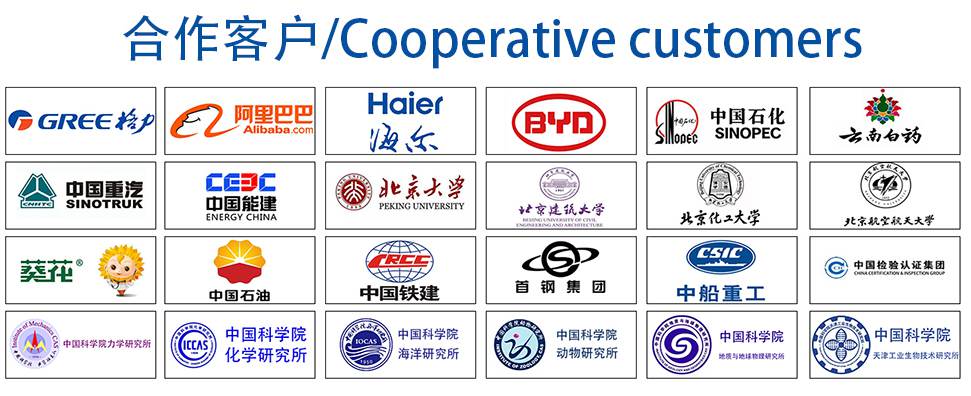