乘用车仪表板总成和副仪表板总成检测项目解析
随着汽车工业对安全性和用户体验要求的不断提升,乘用车仪表板总成(IP)和副仪表板总成(CNSL)的检测成为整车质量控制的重要环节。作为驾驶舱的核心部件,二者的功能性、耐久性及安全性直接影响车辆性能和用户满意度。检测过程需覆盖从原材料验证、装配精度到功能测试的全流程,并严格遵循ISO、GB(国标)及主机厂企业标准,以确保产品在复杂工况下的可靠性和合规性。
一、仪表板总成(IP)核心检测项目
1. 结构完整性检测:
通过3D扫描比对设计数据,验证仪表板骨架、安装孔位及面差尺寸精度(公差≤±0.5mm)。冲击试验模拟头部碰撞(ECE R21标准),检测安全气囊爆破区域弱化线精度及碎片防护性能。
2. 材料性能测试:
采用热老化箱(-40℃~120℃循环)验证表皮材料的耐温变形能力,光照氙灯试验评估抗紫外线老化特性。挥发性有机物(VOC)检测需满足GB/T 27630限值,甲醛释放量≤0.1mg/m³。
3. 功能可靠性验证:
组合仪表需通过EMC电磁兼容测试(ISO 11452系列),在50V/m场强下保持显示稳定性。出风口风量均匀性偏差≤15%,调节机构需完成5000次耐久循环无卡滞。
二、副仪表板总成(CNSL)专项检测内容
1. 人机交互测试:
换挡机构操作力需控制在3-8N·m区间(SAE J1479标准),杯托夹持力经过2000次插拔试验后保持≥5N。无线充电模块需通过Qi协议认证,传输效率≥70%。
2. 动态疲劳试验:
模拟整车振动工况(频率5-500Hz,加速度5g),连续测试200小时后检查结构件裂纹及异响。储物盒盖板需承受10万次开合测试,铰链磨损量≤0.2mm。
3. 环境适应性验证:
高低温交变试验(-45℃~85℃)后检测电子挡位显示模块功能,湿热试验(40℃/95%RH)评估镀铬饰条72小时盐雾腐蚀等级。
三、系统集成检测要求
总成装配后需进行全尺寸CMM测量,关键配合面平面度≤0.3mm/m。整车NVH测试中,仪表板区域在120km/h时速下异响值需<45dB(A)。CAN总线通信需通过故障注入测试,确保仪表指示灯与ECU的同步误差≤50ms。
通过上述系统化检测流程,可有效控制仪表板总成与副仪表板总成的质量风险。据统计,严格的检测体系能使总成件售后故障率降低62%,同时提升用户对内饰感知质量的评分达28%。未来随着智能表面技术的普及,检测项目将进一步向触觉反馈精度、光学显示均匀性等新维度延伸。
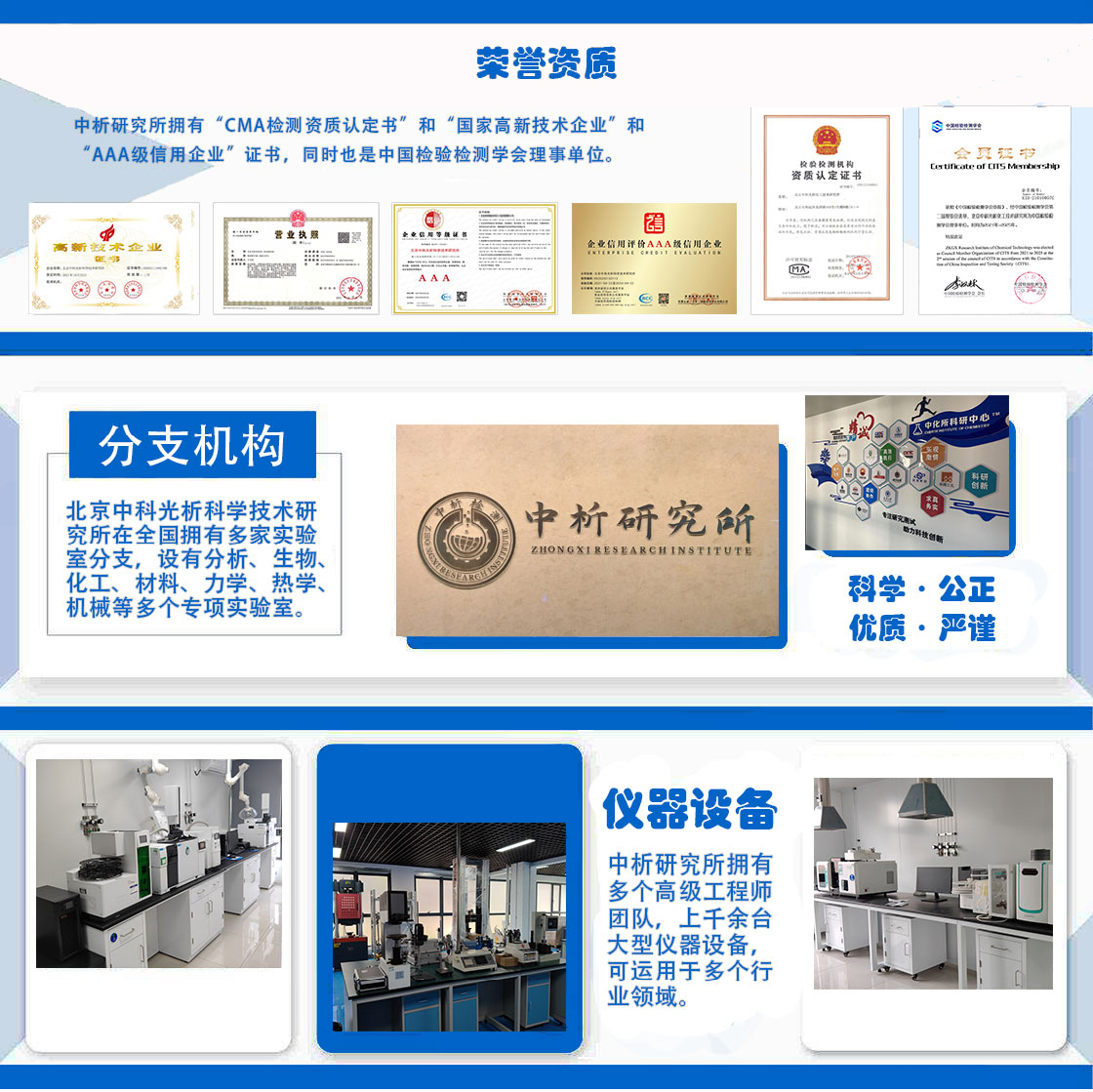
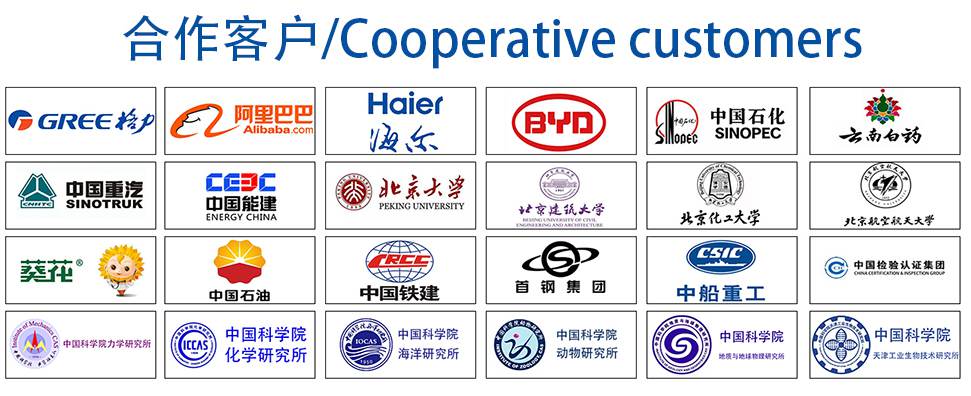