汽油燃料内燃机燃油管路用橡胶软管和纯胶管的检测项目解析
在汽油燃料内燃机的燃油输送系统中,橡胶软管和纯胶管作为关键连接部件,承担着输送燃油、耐受高温高压及化学腐蚀的重要任务。其性能直接影响发动机的工作效率和安全性,因此必须通过严格的检测确保其符合行业标准(如ISO、SAE、GB等)。检测项目需覆盖物理性能、化学稳定性、耐候性及长期使用可靠性,以防止燃油泄漏、管路老化等安全隐患。
一、物理性能检测
1. 拉伸强度和断裂伸长率:通过万能材料试验机测试软管在拉伸至断裂时的最大载荷和形变程度,确保其在安装或振动条件下不易破损。
2. 硬度测试:使用邵氏硬度计测量橡胶材料的硬度,验证其柔韧性与耐压性的平衡。
3. 爆破压力试验:向软管内部施加递增压力直至破裂,检测其最高承压能力是否满足设计要求。
二、耐燃油介质性能检测
1. 体积变化率与质量变化率:将试样浸泡于标准燃油(如ASTM参考燃料C)中一定时间后,计算其体积和质量变化,评估橡胶抗溶胀和耐渗透能力。
2. 耐化学腐蚀测试:检测软管在含乙醇、甲醇等新型燃料成分中的抗腐蚀性能,适应新能源燃料需求。
三、耐温性与老化测试
1. 高温耐久性:在120°C以上高温环境中进行长时间循环试验,观察软管是否出现硬化、龟裂或变形。
2. 低温脆性测试:将样品置于-40°C低温环境中,验证其在极端寒冷条件下的柔韧性。
3. 热空气老化与臭氧老化:通过加速老化试验模拟长期使用环境,评估材料抗臭氧龟裂和热氧老化能力。
四、结构与尺寸精度检测
1. 内径与壁厚测量:使用精密量具或激光扫描仪确保软管尺寸符合公差要求,避免安装不匹配或流量异常。
2. 层间粘合强度:针对多层复合软管,测试各层材料(如橡胶与增强纤维)的粘接牢固性,防止分层失效。
五、实际工况模拟测试
在动态脉冲试验台上模拟发动机燃油管路的工作状态,通过反复加压、泄压和振动测试,验证软管在真实环境中的疲劳寿命和密封性能。
总结
汽油燃料内燃机用橡胶软管和纯胶管的检测需多维覆盖材料特性、环境适应性和长期可靠性。只有通过系统化检测,才能确保其在复杂工况下的安全稳定运行,延长发动机使用寿命并降低故障风险。生产企业与检测机构需严格遵循国际标准,结合新型燃料发展趋势持续优化检测方案。
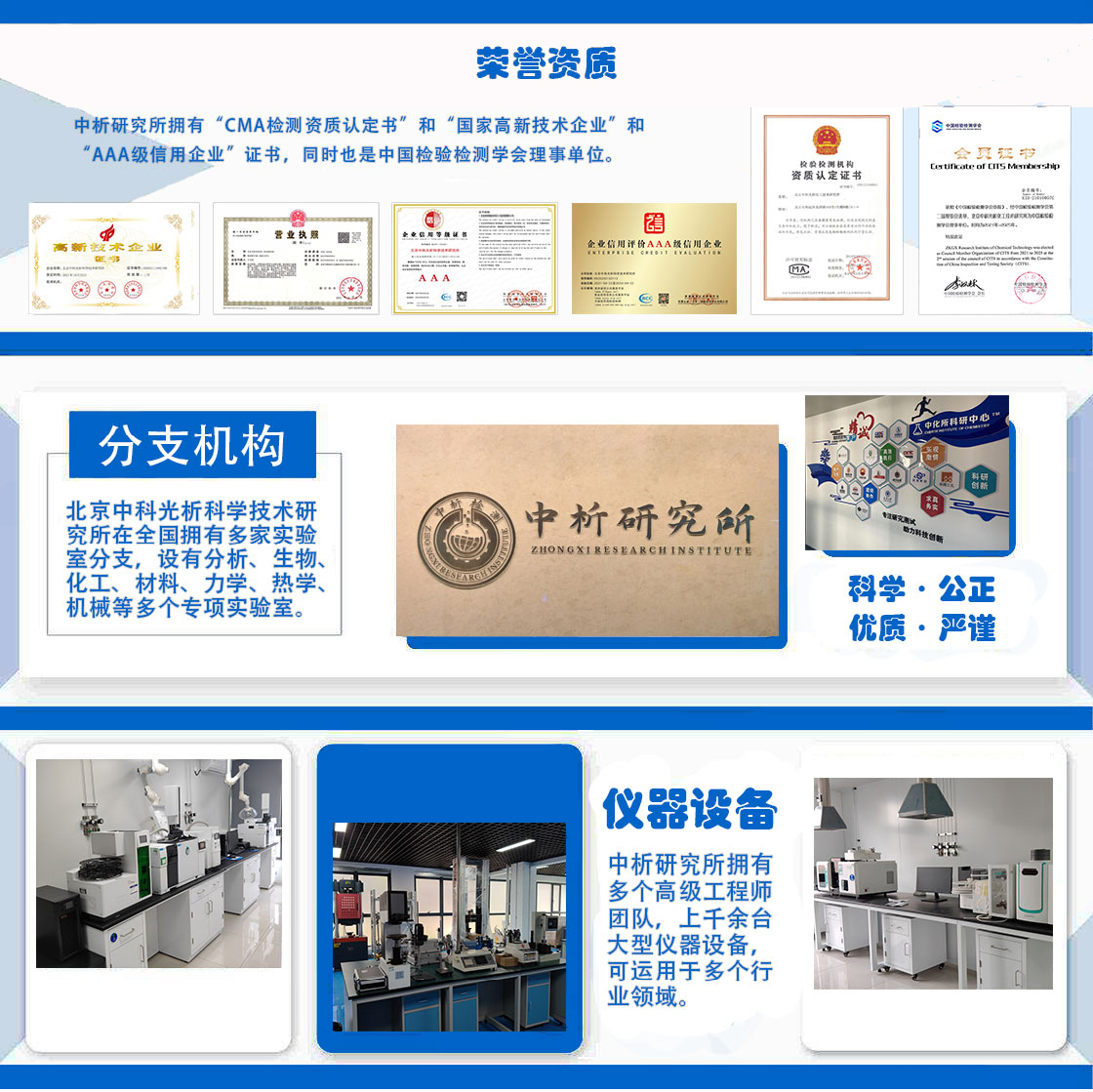
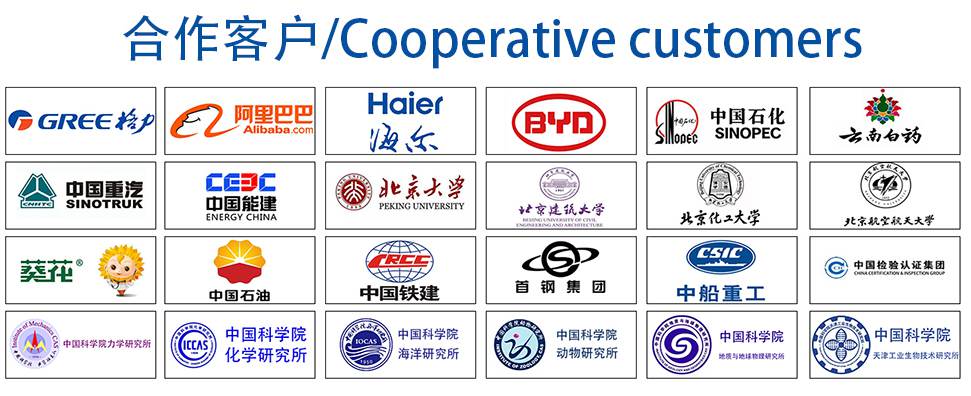