汽车和挂车气压制动装置用储气筒检测的重要性
储气筒作为汽车和挂车气压制动系统的核心部件,承担着储存压缩空气、平衡气压波动、保障制动稳定性的关键作用。其性能直接关系到车辆的制动安全性和可靠性。由于储气筒长期处于高压、振动、腐蚀等复杂工况下,若出现泄漏、裂纹或结构失效,可能导致制动系统气压不足甚至完全失效,引发严重交通事故。因此,对储气筒进行定期检测和性能评估是车辆安全维护中不可忽视的环节。
储气筒检测的主要项目
1. 外观与结构完整性检测
通过目视检查、敲击检测或工业内窥镜等手段,确认储气筒表面是否存在裂纹、变形、锈蚀或焊接缺陷。重点检查筒体、焊接接头、安装支架等易损部位,确保无结构性损伤。
2. 密封性测试
采用气压试验法,将储气筒充入额定工作压力的1.2-1.5倍(通常为0.8-1.2MPa),保压5分钟后观察压力表数值变化。若单位时间内压降超过标准(如QC/T 200规定≤0.01MPa/min),则判定密封性不合格。
3. 耐压强度试验
通过液压或气压方式对储气筒施加2-3倍工作压力,持续3-5分钟,测试其抗爆裂能力。爆破压力需满足GB/T 19905或相关行业标准要求,且不得出现永久性变形或泄漏。
4. 内部清洁度检测
使用压缩空气吹扫或内窥镜检查,确保筒内无积碳、油污、金属碎屑等污染物。残留物可能导致制动阀堵塞或加速密封件老化,影响系统响应速度。
5. 耐腐蚀性能测试
通过盐雾试验(GB/T 10125标准)模拟恶劣环境,评估储气筒涂层、镀层或材质的抗腐蚀能力。试验后需无起泡、剥落或基材腐蚀现象。
6. 安装稳定性验证
检查储气筒支架、紧固件的连接状态,进行振动台模拟试验(频率10-50Hz,加速度5-10m/s²),确保在持续振动下无松动、位移或共振现象。
检测标准与周期建议
储气筒检测应参照GB/T 19905《汽车制动系统用储气筒技术条件》、QC/T 200《汽车和挂车气压制动装置用储气筒性能要求及试验方法》等标准执行。建议车辆每行驶5万公里或每年进行一次常规检测,事故维修后或发现制动异常时需立即专项检测。
结语
储气筒的规范化检测不仅关乎法规符合性,更是保障道路安全的重要防线。通过系统化的检测流程与精准的设备支持,可有效预防制动失效风险,延长部件使用寿命,为车辆安全运营提供技术支撑。
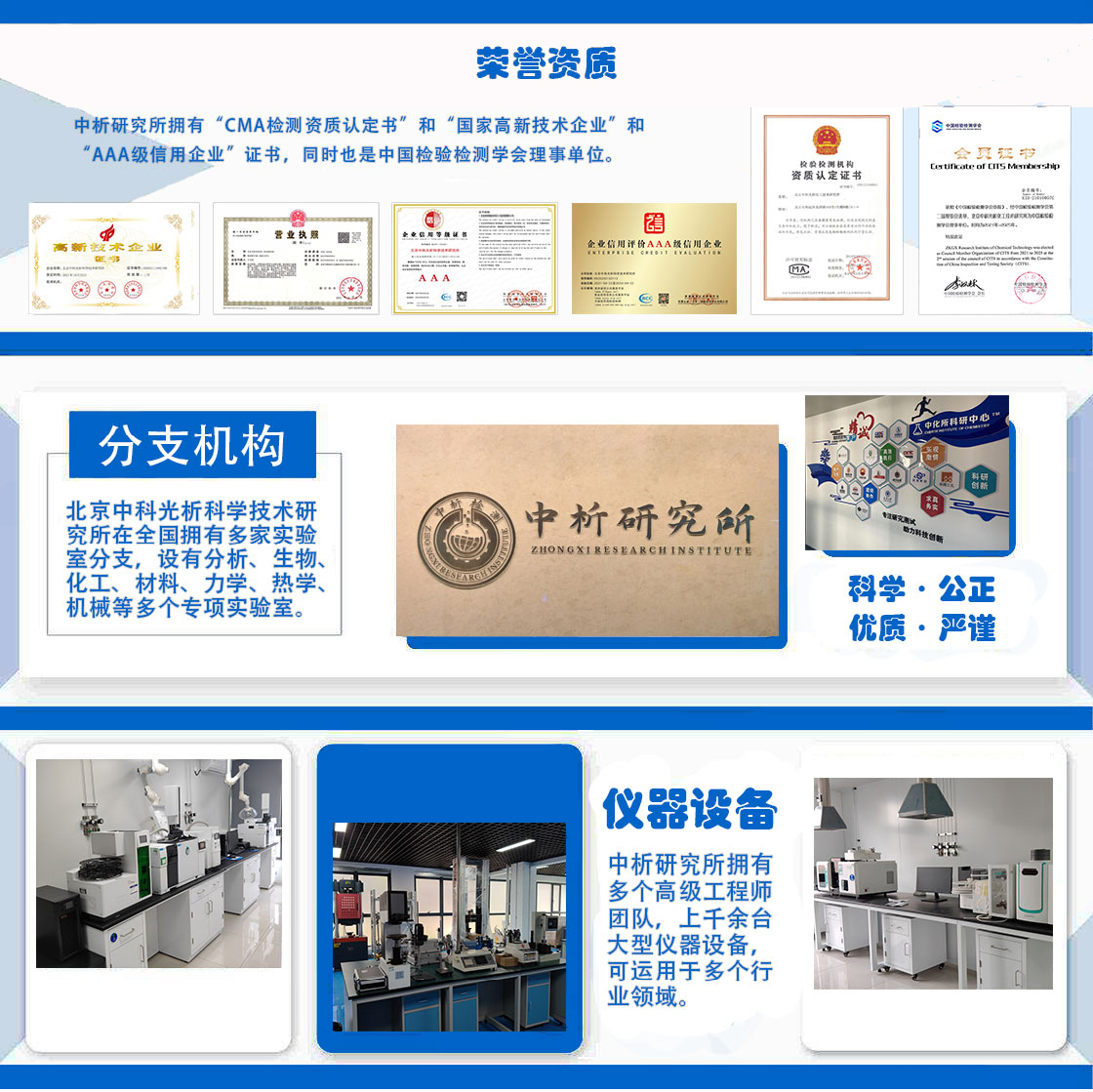
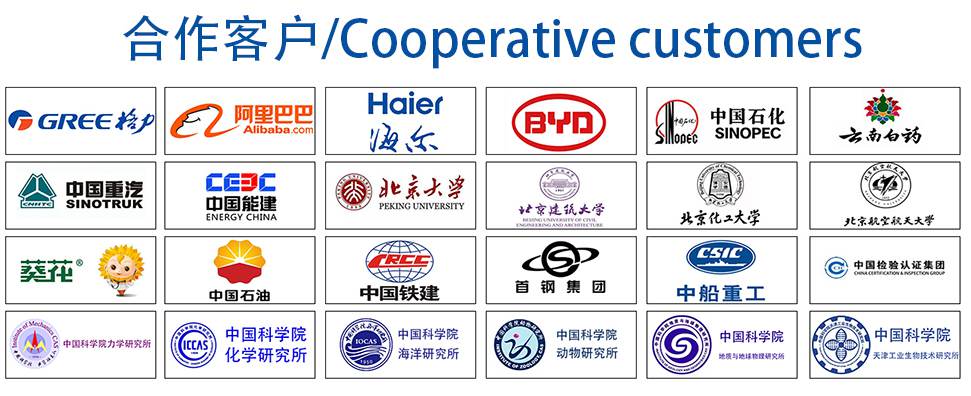