导向装置检测项目及技术要点解析
导向装置作为机械设备中确保运动部件精准定位的核心组件,其性能直接影响设备运行精度与稳定性。在航空航天、轨道交通、精密加工等领域,导向装置的检测已成为质量控制和设备维护的重要环节。根据GB/T 17421.1-2020《机床检验通则》和ISO 10791-7:2020《加工中心试验条件》等标准要求,导向装置的检测需覆盖几何精度、材料性能、动态特性等20余项专业指标,通过系统化检测可有效预防因导向失效导致的设备停机事故,确保生产安全与效率。
1. 几何尺寸与形位公差检测
采用三坐标测量机(CMM)与激光干涉仪,重点测量导轨的直线度(≤0.01mm/m)、平行度(≤0.015mm/全长)和垂直度(≤0.02mm/300mm)。滑动副配合间隙需控制在0.005-0.03mm范围内,并使用塞尺进行多点位验证。
2. 材料性能检测
通过洛氏硬度计检测导轨表面硬度(HRC58-62),拉伸试验验证抗拉强度(≥1200MPa),金相分析检验渗碳层深度(0.8-1.2mm)。振动频谱分析可发现材料内部缺陷,确保疲劳寿命>10^7次循环。
3. 表面质量检测
使用表面粗糙度仪测量Ra值(0.4-0.8μm),轮廓仪检测波纹度(Wt≤0.3μm)。荧光渗透检测可发现>5μm的表面裂纹,涂层测厚仪验证耐磨镀层厚度(20-30μm)。
4. 运动特性检测
动态测试时需监测摩擦系数(0.05-0.12)、爬行量(≤0.002mm)和温升(ΔT≤15℃)。激光多普勒测振仪可捕捉0.1μm级振动,噪声检测需满足≤75dB(A)的行业标准。
5. 耐磨性能检测
通过往复式磨损试验机模拟工况,检测单位行程磨损量(≤0.5μm/km)。运用扫描电镜(SEM)分析磨损形貌,润滑油膜厚度应保持>3μm以确保边界润滑状态。
6. 安装精度验证
采用电子水平仪检测基础平面度(≤0.02mm/m²),预紧力需通过扭矩扳手控制在设计值的±5%范围内。热变形补偿检测需在20-50℃温差环境下验证位移变化量(≤0.05mm)。
7. 功能性试验
满载运行试验需持续72小时,检测速度波动(±2%)、定位重复性(±0.003mm)和反向间隙(≤0.005mm)。突发制动测试需在0.2秒内实现完全止动,冲击加速度≤3g。
8. 环境适应性检测
依据IEC 60068标准进行盐雾试验(96h)、高低温循环(-40℃~+85℃)和粉尘防护(IP65等级)测试。振动试验需模拟5-2000Hz随机振动,加速度谱密度不超过0.04g²/Hz。
现代检测技术已实现多参数同步采集与大数据分析,如采用数字孪生技术建立导向装置的全生命周期健康档案。建议企业建立包含预防性检测(每500小时)、预测性维护(基于状态监测)和纠正性维修的三级检测体系,通过规范化检测流程将导向系统故障率降低60%以上。
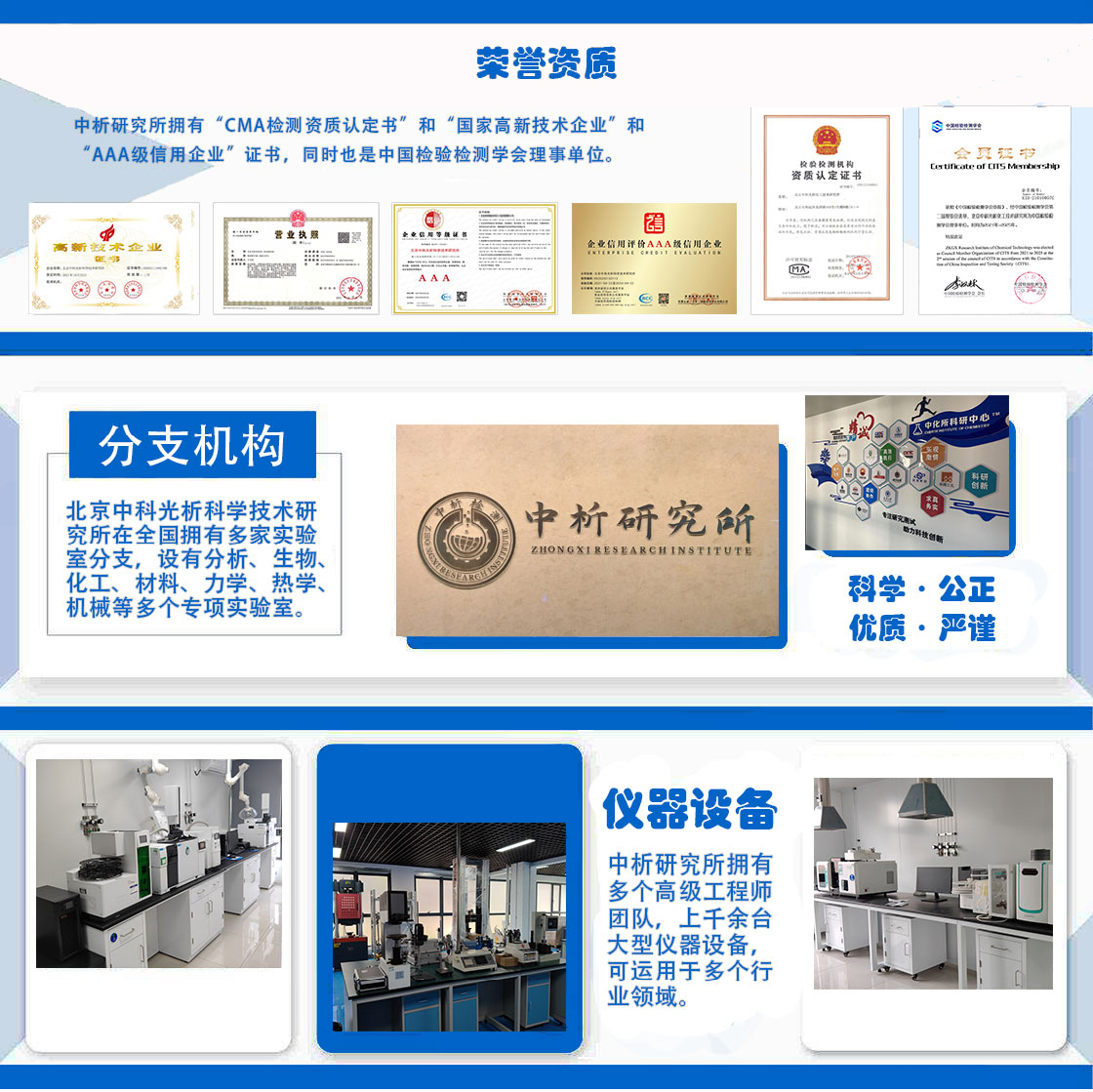
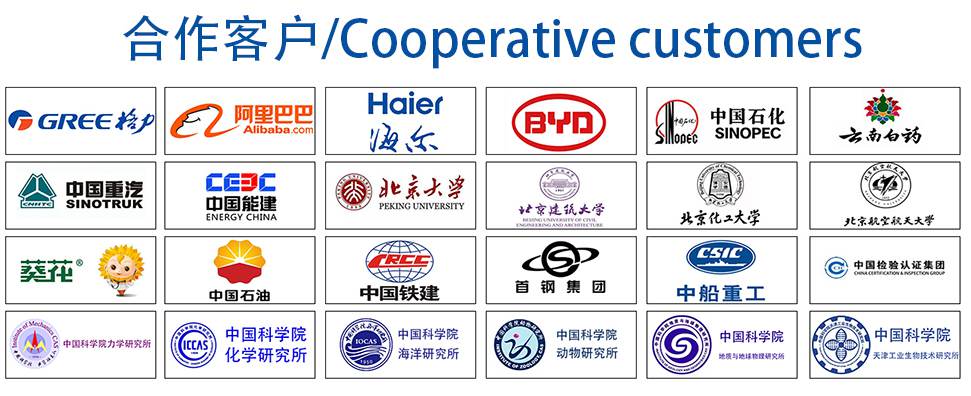