模架检测的重要性与核心指标
在模具制造与工业生产中,模架作为支撑模具结构的关键组件,其精度、稳定性和耐久性直接关系到产品质量、生产效率及设备安全性。模架检测是通过系统性评估框架尺寸、材料性能、装配精度等参数,确保其满足设计规范和工艺要求的必要环节。尤其在汽车制造、电子注塑、精密铸造等领域,微小偏差可能导致产品缺陷甚至生产线停机,因此模架检测已成为制造企业质量控制的核心内容。
模架检测的主要项目与技术要求
1. 尺寸精度检测
使用三坐标测量仪(CMM)或激光扫描设备对模架的长、宽、高、孔距等关键尺寸进行全尺寸测量,确保公差控制在±0.01mm以内。重点检查模板平面度、导柱导套同轴度以及定位环与注塑机的匹配精度。
2. 材料性能分析
通过光谱分析仪检测模架钢材的化学成分,验证是否达到S50C、P20等标准牌号要求。同时需进行硬度测试(洛氏HRC 28-32)、金相组织观察及冲击韧性试验,确保材料具备抗变形、耐磨损能力。
3. 结构强度与应力分布检测
应用有限元分析(FEA)模拟模架在高压注塑环境下的受力状态,结合应变片实测数据验证框架抗压强度。重点排查应力集中区域,防止长期使用后出现裂纹或塑性变形。
4. 表面处理与防腐性能测试
采用涂层测厚仪检测氮化、镀铬等表面处理层的厚度均匀性(通常要求≥0.05mm),并进行盐雾试验评估防腐等级。对于精密模架,还需检查抛光面的粗糙度(Ra≤0.2μm)以确保脱模顺畅性。
5. 动态装配精度验证
在模拟工况下测试顶针系统、滑块机构的运动顺畅度,测量复位偏差(≤0.02mm)和重复定位精度(±0.005mm)。使用红外热成像仪监测温升对模架变形的影响,优化冷却水路布局。
智能化检测技术的发展趋势
随着工业4.0的推进,模架检测正逐步向智能化转型。基于机器视觉的在线测量系统可实现实时数据采集,结合AI算法自动判定合格率;数字孪生技术则通过虚拟调试提前预测模架寿命,降低试模成本。未来,检测数据与MES系统的深度集成将进一步提升质量追溯效率。
结语
模架检测不仅是质量控制的关键环节,更是提升模具寿命和产品竞争力的重要保障。企业需建立周期性检测体系(建议每5000模次全面检测一次),结合预防性维护策略,最大限度降低生产风险。通过精准的检测数据和科学的分析手段,可为模架优化设计提供可靠依据,推动制造业向高精度、高效率方向持续发展。
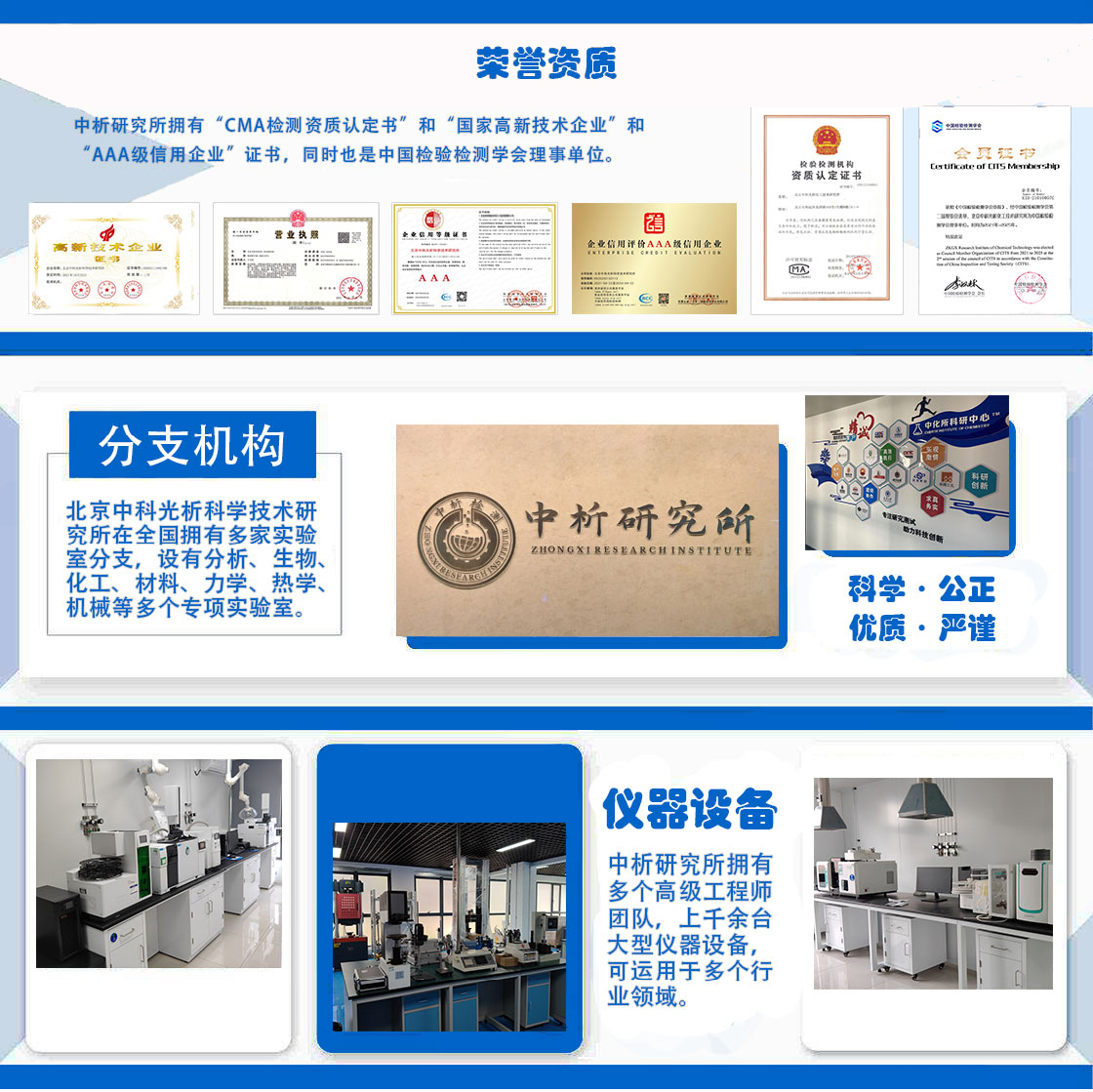
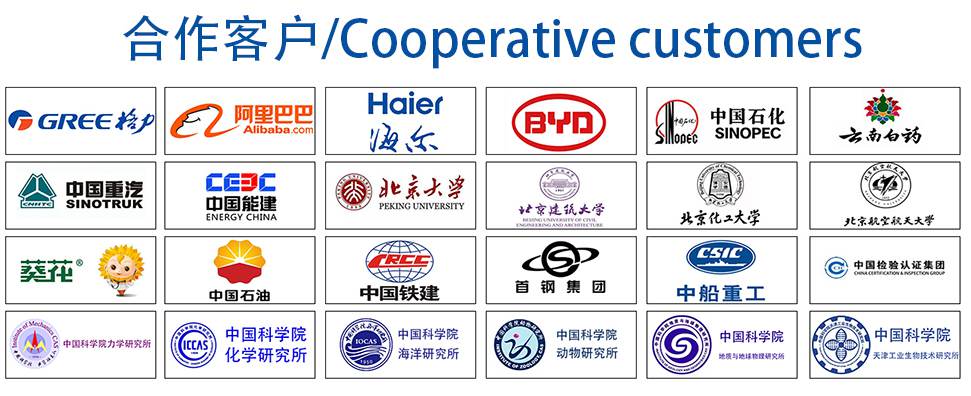