汽车液压比例阀检测的重要性与实施要点
液压比例阀作为汽车制动系统的核心控制元件,承担着动态分配前后轮制动液压力、保障车辆稳定性的重要功能。随着车辆行驶里程和使用年限的增加,阀体磨损、密封失效或电磁线圈故障等问题可能导致制动力分配异常,直接影响行车安全。因此,定期开展液压比例阀专项检测是车辆维护中不可忽视的环节。本文将系统解析液压比例阀的检测项目、技术指标及操作规范,为维修人员提供技术指导。
一、液压比例阀检测核心项目
1. 阀体外观与密封性检测
通过目视检查阀体表面是否存在裂纹、腐蚀或油液渗漏痕迹,重点检测密封圈老化程度。使用加压测试仪在0.5-2MPa范围内进行保压试验,观察10分钟内压力降是否超过额定值(通常≤3%)。
2. 电磁线圈功能性测试
使用万用表测量线圈电阻值(常规值12-20Ω)并对比厂家标准数据。通过示波器监测PWM控制信号的波形完整性,检测占空比变化时线圈电流响应是否线性。
3. 压力响应特性检测
搭建专用测试台架,以0.1MPa/s速率逐步增加输入压力,记录输出端压力曲线。重点验证比例阀在20%-80%工作区间的线性度误差(应<5%),并检测阶跃响应时间(标准值≤50ms)。
二、进阶诊断与数据分析
1. 动态循环耐久测试
通过液压伺服系统模拟连续5000次以上工作循环,监测压力波动范围和滞后效应。当输出压力偏差超过初始值15%时判定阀体磨损超标。
2. 温度影响试验
在-40℃至120℃环境舱中测试阀体性能,确保高温下无卡滞现象,低温环境启动力矩不超过3N·m。关注密封材料在不同温度下的膨胀系数匹配性。
三、检测注意事项
检测前需彻底清洗阀体内部残留油液,避免污染测试系统。对于集成式电子比例阀(EHB),需使用专用解码器读取故障码并校准控制参数。测试过程中应严格遵循ISO 4925标准,使用精度等级≥0.5级的压力传感器,确保数据可靠性。
通过系统化检测可精准判断液压比例阀的工作状态,对存在轻微性能衰退的阀体可通过更换密封组件或调整预紧力恢复功能,而严重磨损件需整体更换。建议每2万公里或1年进行一次专业检测,有效预防制动系统失效风险。
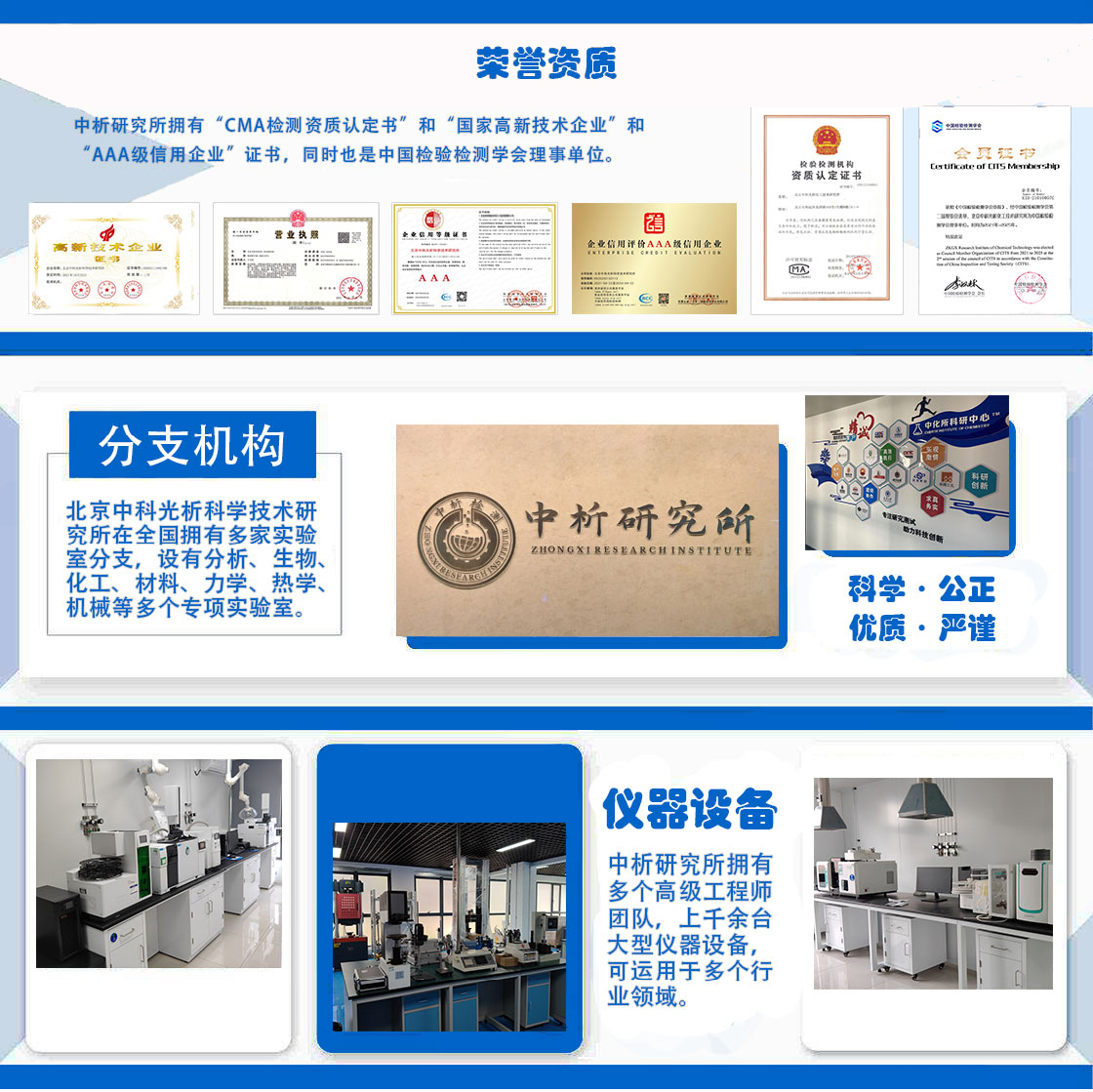
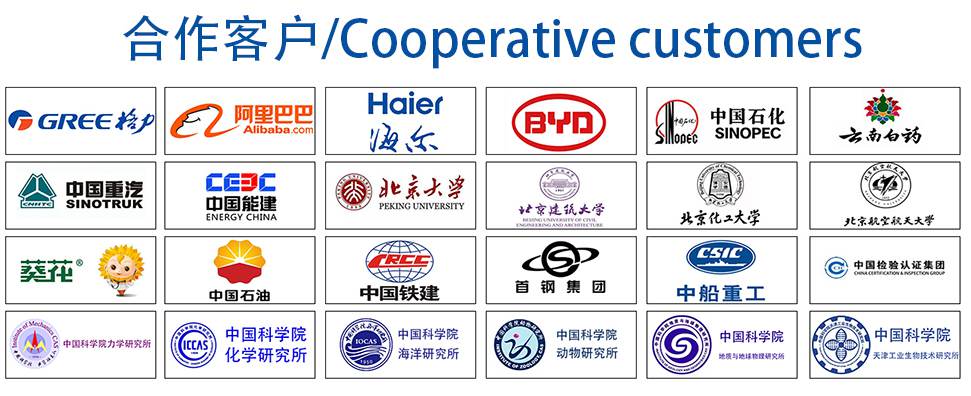