压铸模作为现代制造业中金属零部件成型的核心工具,其质量直接决定了产品精度、生产效率及模具寿命。压铸模检测是保障模具性能的关键环节,涉及材料、结构、工艺等多维度分析。随着汽车、电子、航空航天等领域对高精度复杂零件的需求激增,压铸模检测技术正朝着智能化、高精度化方向发展。通过系统化的检测流程,企业可有效避免因模具缺陷导致的产品报废、生产线停机等问题,从而降低生产成本并提升市场竞争力。
1. 尺寸精度检测
通过三坐标测量仪(CMM)或激光扫描技术,对模具型腔、顶针孔位、分型面等关键部位的尺寸公差进行验证,确保与设计图纸的偏差控制在±0.02mm以内。重点检测合模后型腔的闭合间隙与配合精度。
2. 表面质量分析
使用表面粗糙度仪、金相显微镜等设备,检查模具工作面的划痕、气孔、裂纹等缺陷。针对氮化、镀铬等表面处理工艺,需额外检测涂层厚度(10-50μm)与结合强度,以评估抗粘模性能。
3. 材料性能测试
采用光谱仪检测模具钢成分(如H13钢的Cr含量5%),通过布氏硬度计测量硬度值(HRC48-52),并结合冲击试验机验证材料韧性,确保满足高压铸造的机械强度要求。
4. 热平衡检测
利用红外热像仪监测模具工作时的温度场分布,分析冷却水道效率。要求型腔表面温差不超过30℃,避免因局部过热导致缩孔或粘模缺陷。
5. 结构强度验证
通过有限元分析(FEA)模拟模具受力状态,配合应变片实测关键位置的应力值。模具在锁模力作用下(通常800-2500T)的最大变形量应小于0.1mm。
6. 导柱导套配合检测
使用塞规检测导柱与导套的间隙配合(H7/g6级),合模过程需保证导向平稳无卡滞。配合面粗糙度要求Ra≤0.8μm,直线度误差<0.01mm/m。
7. 冷却系统效能测试
采用流量计检测冷却水道通水量(≥15L/min),使用压力传感器验证无泄漏(测试压力1.5倍工作压力)。通过热循环试验评估冷却效率对生产节拍的影响。
8. 残留应力检测
应用X射线衍射法或盲孔法测量机加工后的残余应力分布,重点控制型腔表面的压应力值(建议范围-200至-500MPa),避免应力释放导致模具变形。
9. 模具寿命评估
通过模拟试验统计模具的疲劳寿命周期,记录型腔表面硬度下降曲线。优质模具应保证8-15万模次后仍符合生产要求,表面无龟裂或塌陷现象。
10. 生产适应性测试
在实际生产环境中进行试模验证,监测模具的脱模力(通常<5kN)、飞边产生率(<0.1%)等参数,确保与压铸机的匹配性及工艺稳定性。
建立完整的压铸模检测体系需结合ISO 8062、GB/T 9444等标准,采用自动化检测设备与大数据分析技术。建议企业每5000模次进行一次全面检测,并建立3D数字孪生模型实现预测性维护,最大程度延长模具使用寿命。
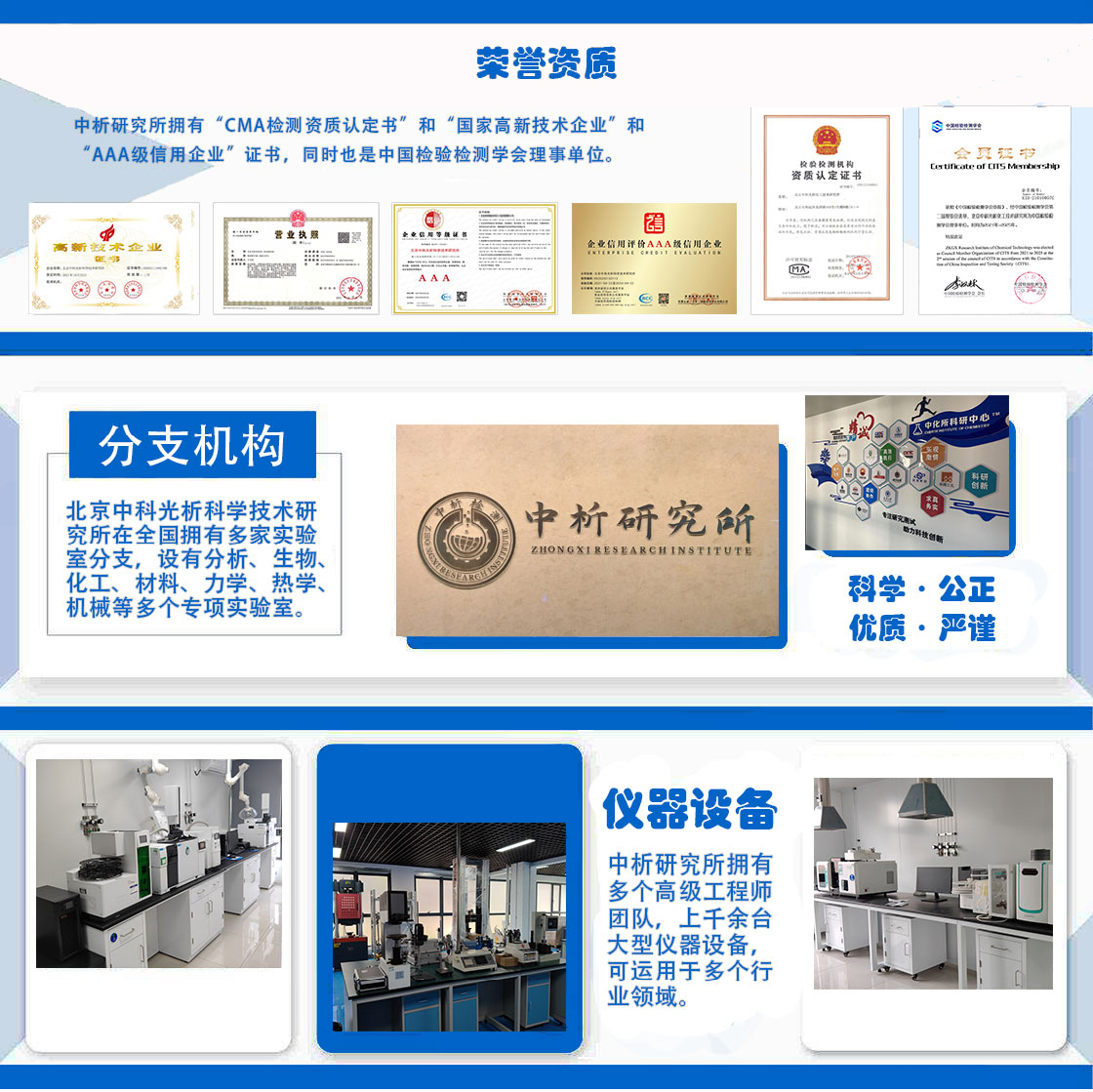
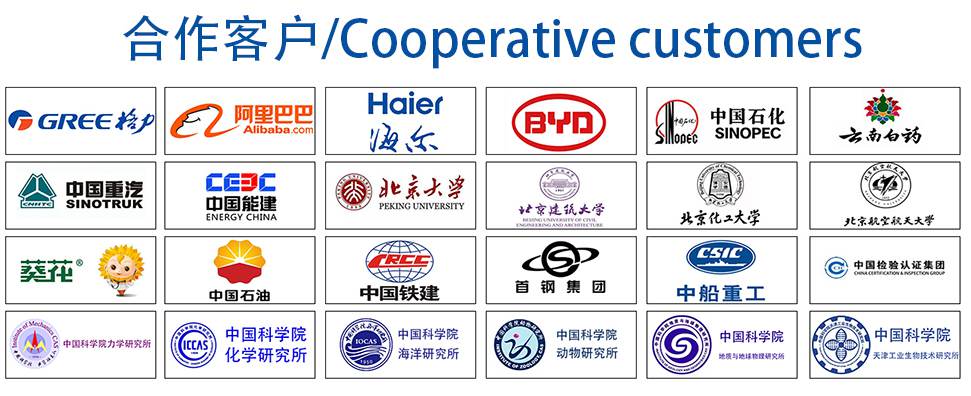