侧刃与导料装置在冲压模具中的重要性及检测要点
侧刃和导料装置是冲压模具中不可或缺的核心部件,其性能直接关系到冲压生产的精度、效率及安全性。侧刃主要用于控制条料的宽度或切除工艺废料,而导料装置则承担着引导材料精准进给的任务。在长期高频率的生产过程中,这两类部件容易因磨损、变形或安装误差导致功能失效,进而引发产品尺寸偏差、模具卡料甚至设备损坏等问题。因此,建立系统的检测项目并定期实施专业检查是保障模具稳定运行的关键环节。
侧刃检测项目及技术规范
1. 刃口几何精度检测:使用光学投影仪或三坐标测量仪对刃口直线度、角度及刃尖圆弧半径进行测量,确保与设计图纸公差一致。刃口直线度偏差需控制在0.01mm/m以内,角度公差范围±0.5°。
2. 表面磨损量分析:通过金相显微镜观测刃口表面磨损带宽度,当连续生产20万冲次后磨损带超过0.15mm时,需立即安排修磨或更换。
3. 装配垂直度校验:采用直角规配合千分表检测侧刃与下模座的安装垂直度,允许最大偏移量为0.02mm/100mm。
4. 材料硬度测试:使用维氏硬度计在刃口区域取点测量,硬度值应达到HRC58-62标准范围,确保抗磨损性能。
导料装置核心检测内容
1. 导轨平行度校准:利用激光对中仪检测上下导料板之间的平行度偏差,要求全长范围内不超过0.03mm,避免材料输送时发生偏移。
2. 导向间隙测量:采用塞规检测导料槽与条料间的配合间隙,常规材料厚度≤2mm时单边间隙应保持0.05-0.1mm,特殊材料按工艺要求调整。
3. 表面粗糙度评估:使用表面轮廓仪检测导料面粗糙度Ra值,标准要求≤0.8μm以减少材料摩擦阻力,预防划伤工件表面。
4. 定位销磨损检查:通过光学比较仪观测定位销直径磨损量,当磨损超过原始尺寸0.02mm时必须更换,确保送料定位精度。
综合性能联动检测方案
在进行单项检测的同时,还需实施动态模拟测试:通过试模运行观察材料行进轨迹,使用高速摄像机记录条料与导料装置的接触状态,配合应变片测量侧刃冲裁时的受力分布。该测试能有效发现静态检测难以捕捉的间歇性卡料、偏摆等问题。
检测周期与数据管理
建议每生产15万冲次或每周执行一次常规检测,关键参数需建立数字化档案。采用SPC统计过程控制方法对磨损数据进行趋势分析,当某参数连续三次检测值超过预警线时,应提前安排预防性维护,避免突发性故障影响生产计划。
通过实施上述系统化的检测项目,企业可有效延长模具使用寿命10%-25%,降低因侧刃崩刃或导料失效导致的废品率至0.3%以下,同时减少30%以上的非计划停机时间,显著提升冲压生产的综合效益。
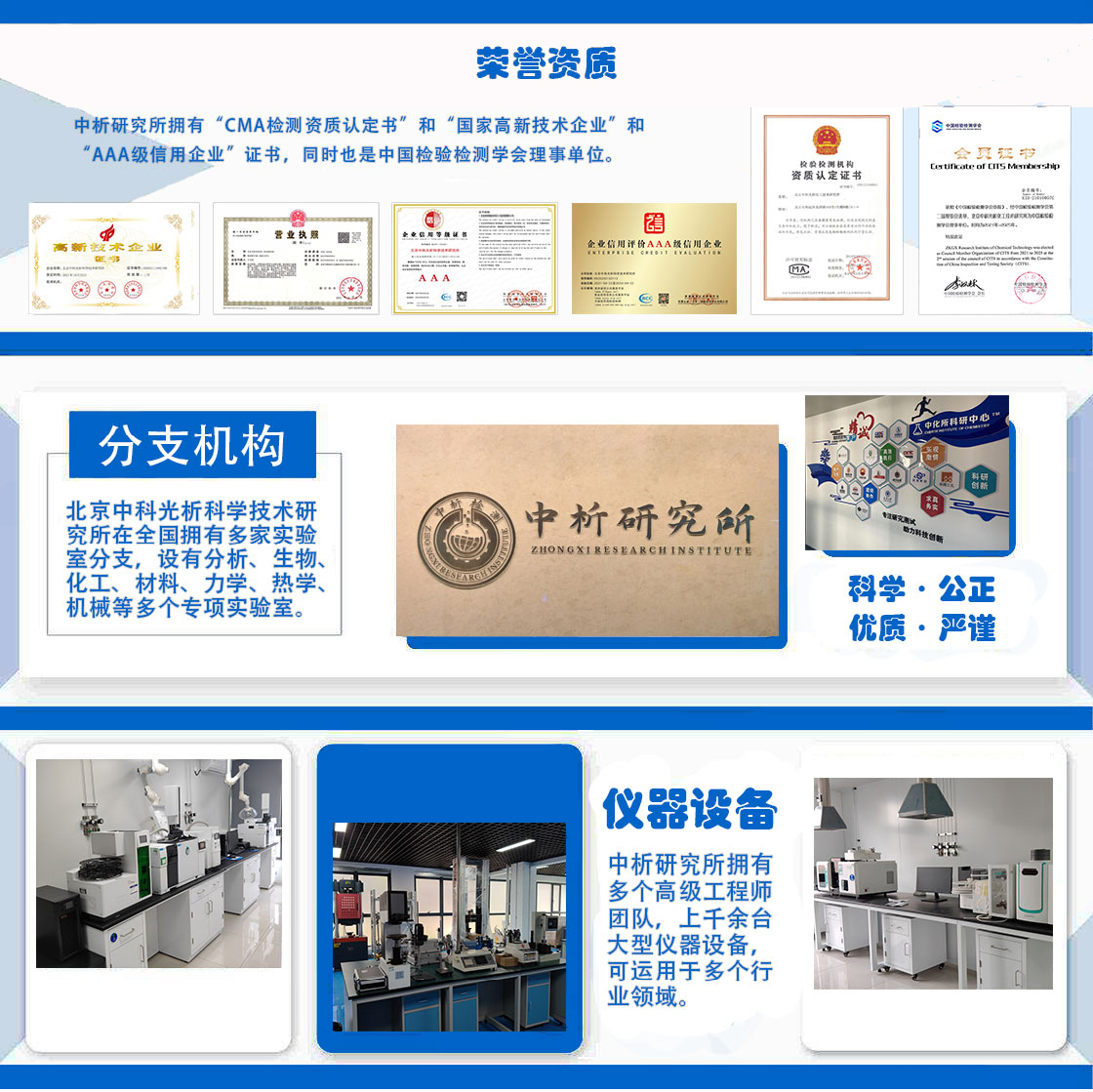
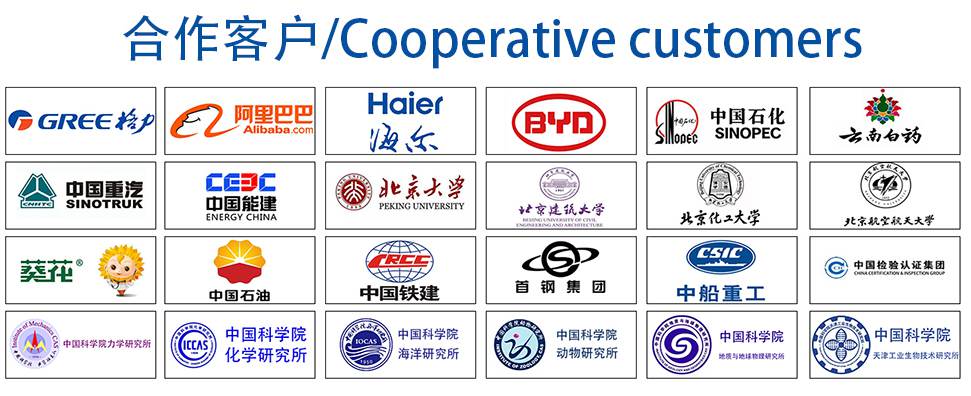