凹凸模检测:精密制造的核心质量保障
在冲压模具、注塑模具等精密制造领域,凹凸模作为核心成型部件,其加工精度直接影响产品尺寸、表面质量及生产效率。凹凸模检测是通过系统化测量手段对模腔轮廓、配合间隙、表面光洁度等关键参数进行量化评估的过程,涉及材料力学、几何计量、无损检测等多学科技术交叉应用。随着智能制造对公差控制要求日益严苛(部分行业要求达到±0.002mm),建立规范的凹凸模检测体系已成为保障模具寿命、降低报废率、规避批量生产风险的必要措施。
核心检测项目体系
完整的凹凸模检测体系包含七大核心维度:
1. 几何尺寸精度检测
使用三坐标测量机(CMM)对模腔轮廓进行三维扫描,比对CAD设计模型数据偏差。重点检测:
- 成型曲面曲率半径偏差(<0.005mm)
- 分型面平面度(≤0.01mm/m)
- 定位孔位置度(IT6级精度)
采用激光干涉仪校验模座平行度,确保装配基准面误差控制在0.003mm以内。
2. 表面质量检测
通过表面粗糙度仪测量Ra值(通常要求0.2-0.8μm),利用电子显微镜检测微裂纹、气孔等缺陷。特殊工艺模具需进行:
- 镜面抛光区域光泽度检测(>90GU)
- 皮纹蚀刻深度一致性检测(±0.015mm)
- 镀层厚度测量(铬层15-25μm)
3. 配合间隙检测
采用蓝丹着色法或电子间隙尺测量凹凸模合模间隙:
- 普通冲压模允许0.03-0.05mm均匀间隙
- 精密级进模要求<0.015mm
- 注塑模须保证型腔零贴合并预留排气槽(0.02-0.04mm)
4. 材料性能检测
通过光谱分析仪验证模具钢成分(如SKD11含Cr11-13%、Mo0.8-1.2%),洛氏硬度计检测热处理后硬度(HRC58-62)。关键指标包括:
- 抗弯强度(>2000MPa)
- 冲击韧性(≥15J/cm²)
- 热传导系数检测(16-24W/m·K)
5. 动态性能测试
在模拟工况下进行:
- 连续冲压20万次后的尺寸稳定性测试
- 热作模具600℃环境下的抗蠕变试验
- 导柱导套配合磨损量测量(<0.003mm/10万次)
6. 无损探伤检测
采用工业CT扫描内部缺陷,磁粉探伤检测表面裂纹,超声波测厚仪验证镶件结合面密合度。特别关注:
- 冷却水道壁厚均匀性(公差±0.3mm)
- 焊接修复区渗透探伤
- 硬质合金镶件结合强度测试
7. 功能性验证检测
通过试模生产进行最终验证:
- 产品脱模斜度测量(1-3°)
- 飞边产生阈值压力测试
- 顶出系统平衡性检测(各顶杆行程差<0.02mm)
检测周期与数据管理
建议实施三级检测制度:
- 加工过程每工序进行自检(2小时/次)
- 半成品阶段全尺寸检测(8小时/套)
- 每5万冲次进行预防性检测
采用MES系统建立检测数据库,通过SPC统计分析预测模具寿命,典型数据包括尺寸变化趋势图、表面粗糙度衰减曲线、配合间隙扩大量模型等。
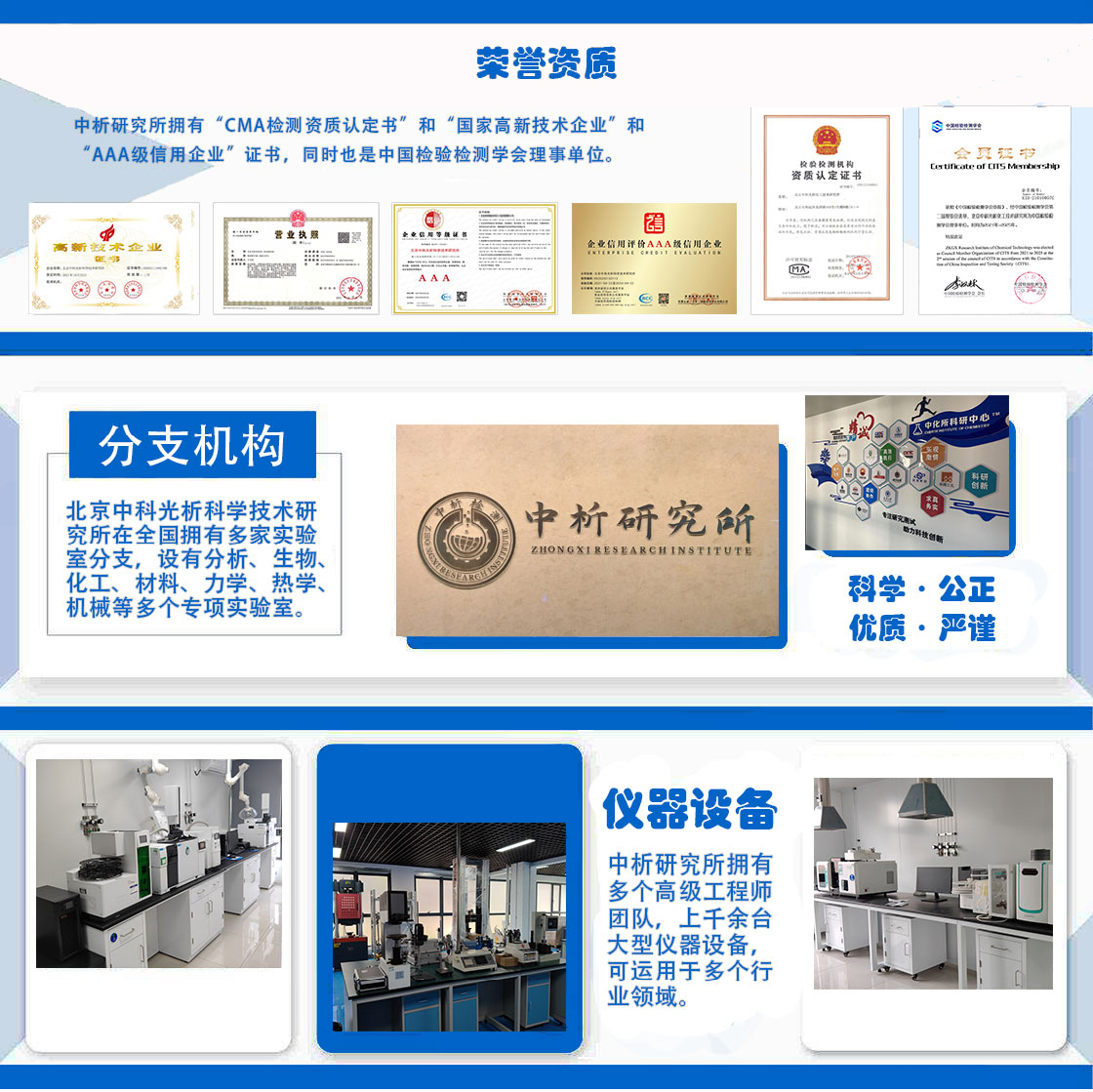
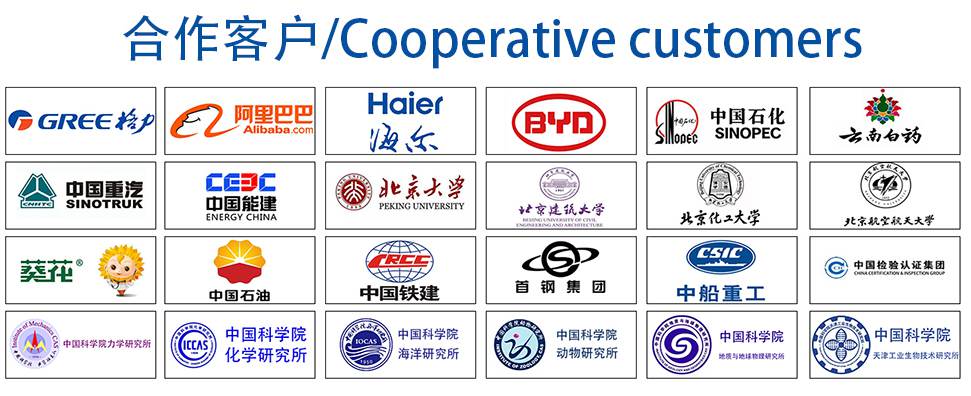