真空成型模检测项目全解析
真空成型模作为塑料加工领域的核心工具,其质量直接影响产品成型精度与生产效率。为确保模具性能符合设计要求并延长使用寿命,系统化的检测流程至关重要。真空成型模检测涵盖材料性能、结构尺寸、表面质量及功能验证等多个维度,需借助专业设备和科学方法进行全面评估。
一、尺寸精度检测
通过三坐标测量仪(CMM)或激光扫描设备,对模具的型腔深度、壁厚、定位孔间距等关键尺寸进行精密测量。需重点关注分型面配合间隙(通常控制在±0.05mm内)以及型面轮廓与设计图纸的吻合度,确保成型产品的几何公差符合ISO 2768标准。
二、表面质量检测
采用白光干涉仪或电子显微镜对模具表面进行微观检测,识别划痕、气孔、腐蚀等缺陷。表面粗糙度需达到Ra0.4-0.8μm标准,同时检查脱模斜度(建议1°-3°)的均匀性,避免因表面异常导致产品粘模或外观瑕疵。
三、材料性能测试
使用洛氏硬度计测量模具基体硬度(铝合金模具要求HRB 80-95,钢模需达HRC 45-52),并通过金相分析检测材料晶粒结构。对加热元件区域需额外进行耐温循环测试,确保在150-300℃工作温度下的稳定性。
四、真空系统检测
使用真空泄漏检测仪测量抽气速率(标准工况下应达到15-25 m³/h),通过压力衰减法测试系统密封性(5分钟内压力回升不超过10%)。需重点检查气路连接处的O型圈密封性能及真空阀响应时间(应≤0.5秒)。
五、功能性验证
进行实际成型试验时,需监测成型周期时间、温度分布均匀性(温差≤5℃)及脱模力数值(标准值需<500N)。通过试制样品的壁厚分布测试(使用超声波测厚仪),验证模具的成型一致性,要求厚度偏差控制在±5%以内。
真空成型模检测需建立定期维护制度,建议每生产5000模次或发现产品合格率下降2%时即启动全面检测。通过数据化管理平台记录磨损演变趋势,可实现预测性维护,将模具故障率降低40%以上。
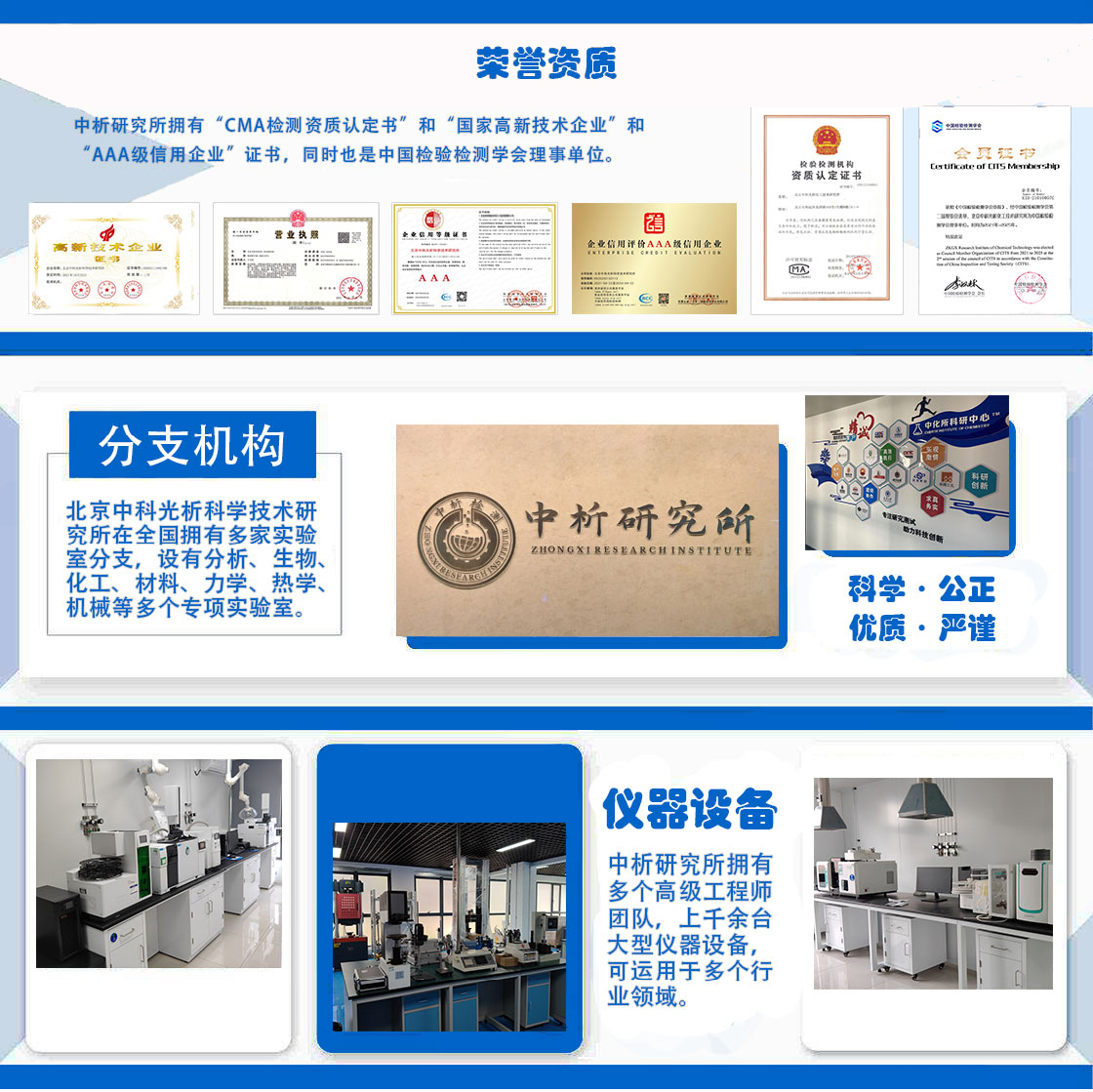
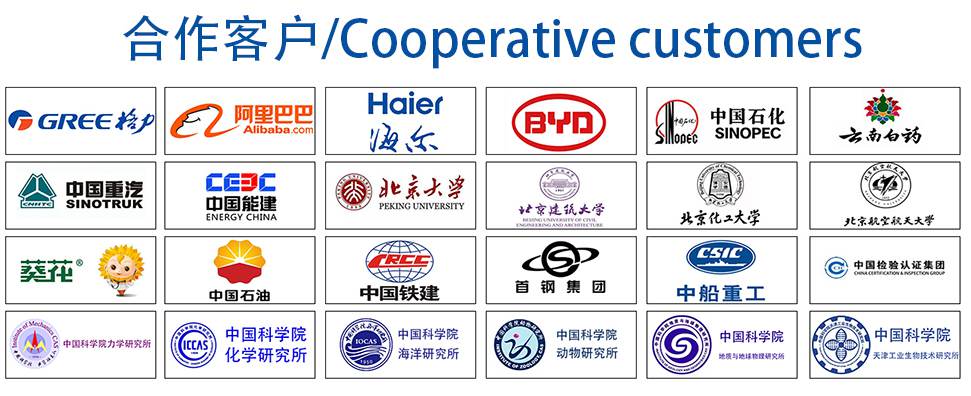