动车组供风单元检测的核心意义
动车组供风单元作为列车空气制动系统、悬挂系统及车门控制系统的核心动力源,承担着压缩空气生产、净化、存储与分配的重要职责。其性能直接关系列车制动响应速度、车厢平稳性及设备可靠性,是保障动车组安全运行的关键子系统。随着列车运行里程的累计和复杂环境的影响,供风单元内的空压机、干燥器、过滤器、管路及阀门等组件可能出现磨损、泄漏或效率下降等问题。因此,定期开展系统性检测项目,能够精准识别潜在故障,确保供风压力稳定、空气质量达标,为动车组全生命周期运维提供重要技术支撑。
供风单元核心检测项目分类
1. 气密性测试与压力保持检测
通过专业压力传感器与泄漏检测仪,对供风单元整体气路开展分段保压测试。重点检测空压机出口管路、干燥塔密封件、储风缸连接法兰等关键节点的泄漏率,要求静态压力降在30分钟内不超过0.05MPa。同步验证安全阀起跳压力是否符合TB/T 3050标准规定值。
2. 空气干燥效能评估
运用露点分析仪对干燥器出口空气湿度进行动态监测,确保压缩空气露点温度始终低于-40℃。检测时需模拟不同负载工况,记录干燥剂再生周期内的湿度波动曲线,比对JIS B 8392干燥设备性能规范。同时检查加热器工作状态与再生排气阀动作时序。
3. 压缩空气质量多维度检测
采用颗粒计数器与油分检测仪对供风单元输出的压缩空气进行采样分析,要求固体颗粒粒径>5μm的污染物含量≤1mg/m³,油蒸气浓度<0.1mg/m³。通过压差计监控三级过滤器的堵塞情况,当进出口压差超过0.15MPa时触发更换预警。
4. 空压机性能参数诊断
通过振动频谱分析仪与热成像设备,检测空压机曲轴箱、连杆轴承等运动部件的机械状态。记录电机电流曲线、排气温度及产气效率等参数,对照EN 1012空压机性能标准判断是否存在气阀磨损、活塞环失效或冷却系统效率下降等问题。
5. 智能控制系统功能性验证
对供风单元PLC控制器开展I/O信号测试,模拟压力开关动作、干燥塔切换指令等场景,验证逻辑控制程序的响应精度。通过HMI人机界面检查历史故障代码存储功能,确保双机冗余系统切换时间≤50ms,符合IEC 61375列车通信网络标准。
检测数据驱动的运维决策
每次检测需生成包含300+数据点的检测报告,采用趋势分析算法评估设备健康度指数。对空压机累计运行时间超过8000小时的单元,建议增加润滑油光谱分析;对露点值持续升高的干燥器,应启动分子筛更换程序。通过检测结果与TCMS列车控制管理系统的联动,实现供风系统故障的预测性维修。
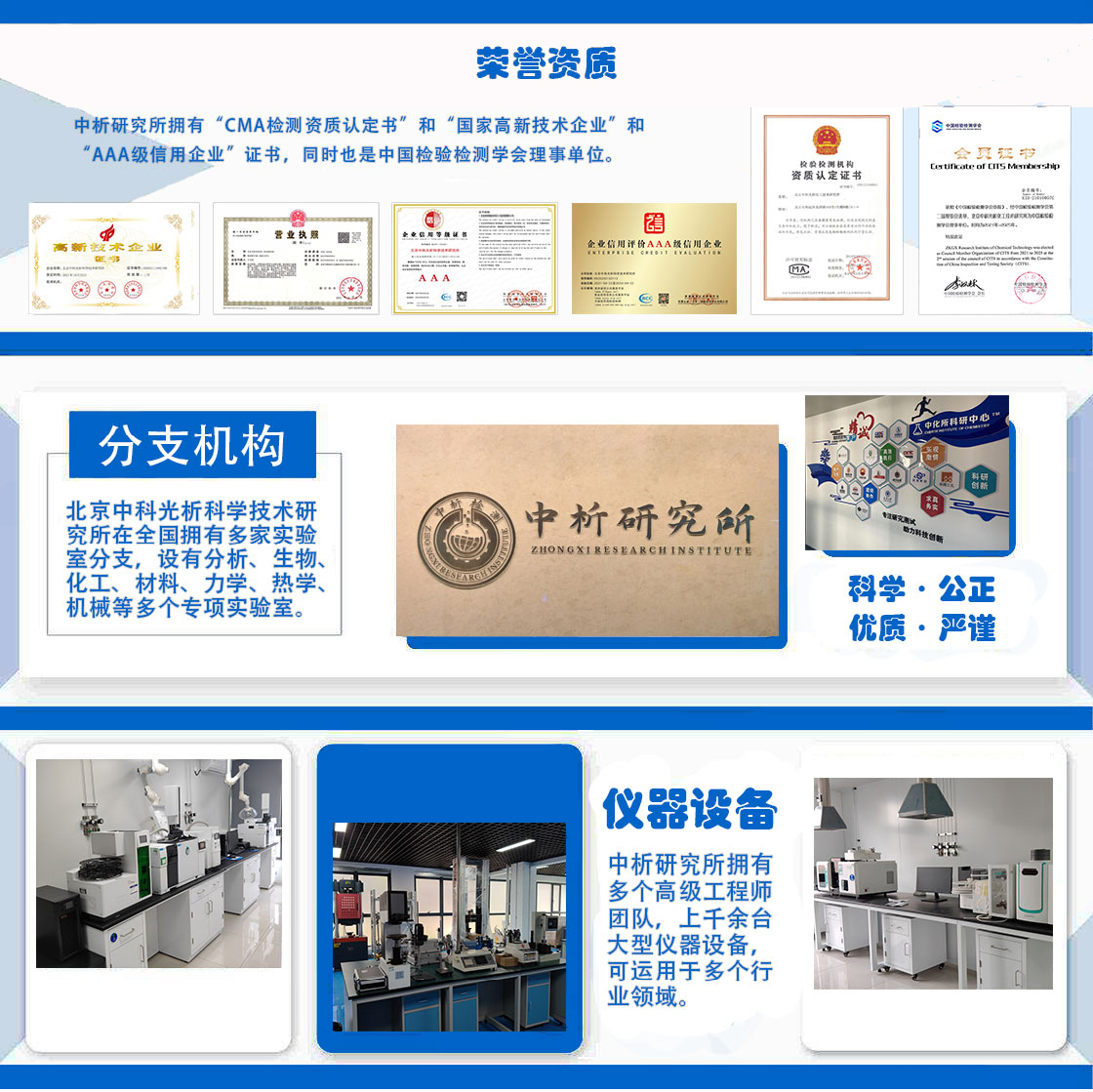
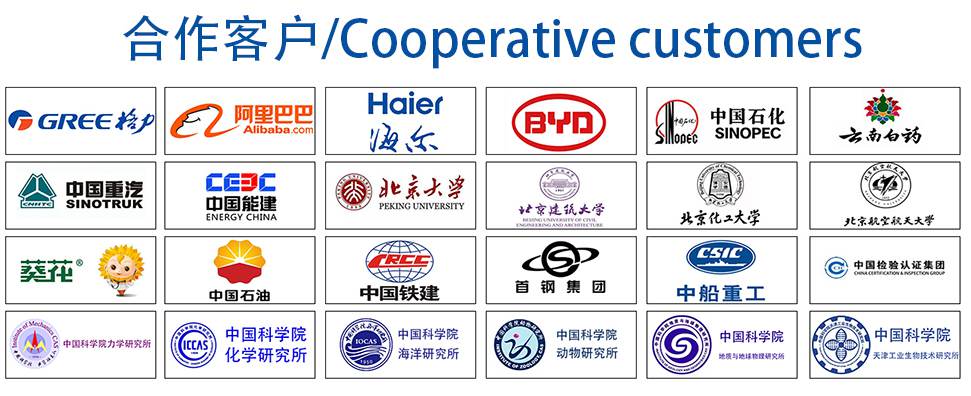