紧固件冷镦模具检测的重要性
紧固件冷镦模具是生产螺栓、螺母、螺钉等金属零件的重要工具,其质量直接影响产品的精度、强度和表面质量。随着工业制造对紧固件性能要求的不断提高,模具在生产过程中易因磨损、变形或材料疲劳而导致失效,进而引发产品缺陷或生产线停机。因此,冷镦模具的定期检测与维护成为保障生产效率和产品质量的关键环节。通过科学的检测手段,可及时发现模具潜在问题,延长使用寿命,降低生产成本,同时确保下游应用的安全性。
核心检测项目与技术要求
1. 尺寸精度检测
冷镦模具的型腔尺寸、冲头长度、凹模孔径等关键尺寸需使用三坐标测量仪(CMM)、投影仪或激光扫描设备进行高精度测量。检测时需参考设计图纸公差要求,重点关注模具工作部位的磨损量,若偏差超过允许范围,可能导致紧固件螺纹不匹配或头部成型不良。
2. 表面质量分析
通过金相显微镜、工业内窥镜或表面粗糙度仪,检查模具工作面是否存在裂纹、划痕、剥落或氧化现象。尤其是冷镦过程中受高应力区域(如冲头尖端、凹模内壁),需重点关注微观缺陷,防止因应力集中导致模具断裂。
3. 硬度与材料性能测试
使用洛氏硬度计或维氏硬度计测量模具表面及基体硬度,确保其符合设计要求(通常HRC 58-62)。同时,通过光谱分析或金相组织观察,验证模具材料成分(如高速钢、硬质合金)是否均匀,避免因热处理不当导致的脆性或韧性不足问题。
4. 装配精度与配合间隙
模具的冲头与凹模的配合间隙直接影响产品成型效果。使用塞尺或激光对中仪检测装配后的同轴度和间隙均匀性,确保公差控制在0.005-0.02mm范围内。过大的间隙会导致毛刺增多,过小则可能引发模具卡死。
5. 动态性能与寿命验证
通过模拟生产条件进行试模试验,记录模具在连续冷镦过程中的温度变化、振动数据及产品合格率。结合疲劳试验机测试模具的抗冲击性能,评估其剩余寿命。若模具单次修模后寿命显著下降,需分析是否为材料劣化或设计缺陷所致。
检测流程的优化方向
为提高检测效率,可引入数字化手段,如基于AI的图像识别技术自动判别表面缺陷,或通过物联网(IoT)实时监测模具工作状态。此外,建立模具检测数据库,记录每次检测结果与维修记录,为预防性维护提供数据支持,最终实现智能制造与成本控制的协同发展。
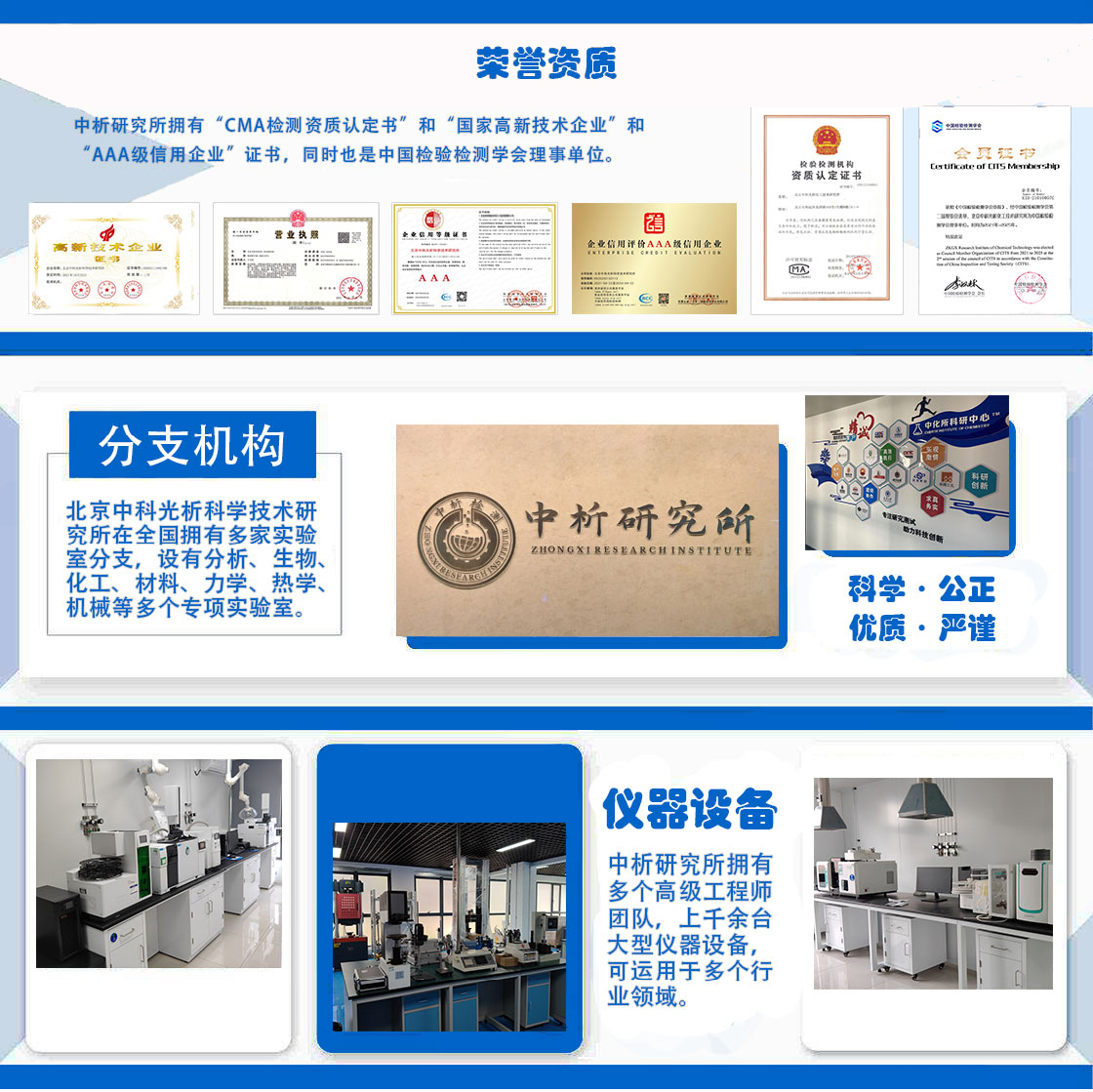
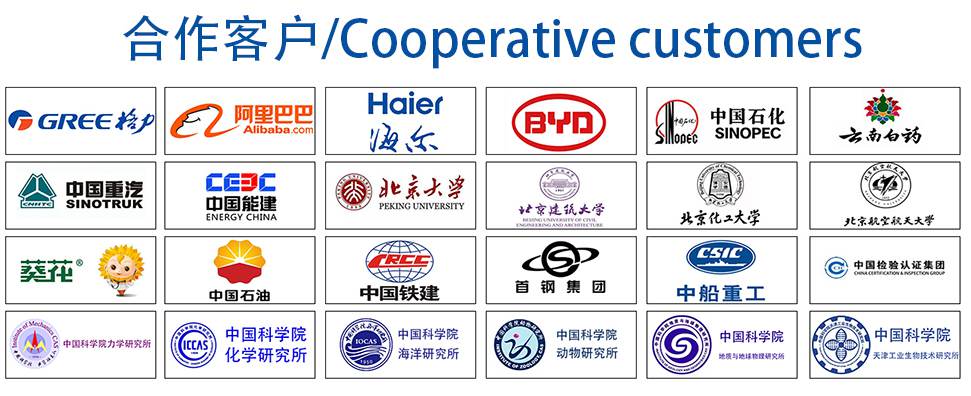