电动车组牵引变流器用冷却装置检测的重要性
在电动车组(如高铁、地铁、新能源轨道车辆)的动力系统中,牵引变流器是电能转换与控制的核心设备,其长期高负荷运行会产生大量热量。冷却装置作为保障变流器稳定工作的关键部件,直接影响设备的效率、寿命及安全性。由于冷却系统需在复杂工况下应对温度波动、振动、灰尘等多重挑战,其性能检测成为确保整车可靠性的核心环节。近年来,随着牵引功率提升和智能化技术发展,冷却装置的检测项目已从基础功能性验证扩展到全生命周期性能评估,涵盖散热效率、密封性、耐久性、智能化控制等全方位指标。
核心检测项目及技术要点
1. 散热性能验证
通过模拟变流器满负荷运行状态,采用热成像仪与多点温度传感器监测冷却液进出口温差、散热片温度分布等参数,验证散热能力是否符合设计要求(通常要求温升控制在15℃以内)。同时需测试冷却装置在极端环境(如40℃高温或-25℃低温)下的散热稳定性。
2. 密封性与耐压测试
使用氦质谱检漏仪对冷却管路进行气密性检测,确保泄漏率低于0.5mL/min。通过高压泵施加1.5倍工作压力的液体循环测试,持续30分钟以上,检验管路接头、焊缝及密封件的抗压能力,防止运行中发生渗漏。
3. 振动与机械冲击测试
依据IEC 61373标准,在振动台上模拟车辆运行时的横向、纵向、垂向振动(频率范围5-150Hz,加速度达3g),持续2小时后检查冷却装置结构完整性。同时进行半正弦波冲击试验(峰值加速度10g,持续时间11ms),评估部件抗机械冲击性能。
4. 材料耐腐蚀与老化评估
对散热器铝翅片、铜质管路等关键材料进行盐雾试验(5%NaCl溶液,35℃持续96小时),观察表面氧化与腐蚀情况。针对橡胶密封件开展热老化测试(150℃环境下保持70小时),检测硬度变化率是否超过20%的阈值。
5. 智能控制功能检测
在具备变频控制功能的冷却系统中,需验证温度-流量动态调节响应时间(通常要求<5秒)、故障诊断准确性(如流量传感器失效报警)及冗余冷却模式的切换可靠性。通过注入模拟故障信号,检测系统能否自动触发保护机制并上传状态代码。
行业标准与检测方法升级趋势
目前主流检测依据包括GB/T 25122.3-2018《轨道交通 机车车辆用电力变流器》、EN 50343(铁路应用-机车车辆电气设备环境条件)等标准。随着液冷技术普及和新型冷媒(如氟化液)的应用,检测体系正向以下方向延伸:①建立基于数字孪生的虚拟测试平台,实现热-流-力多物理场耦合仿真;②引入AI算法分析长期运行数据,预测冷却系统剩余寿命;③开发兼容氢燃料电池等新型动力源的检测规程。这些创新将推动冷却装置检测从被动式质量验证转向主动式健康管理。
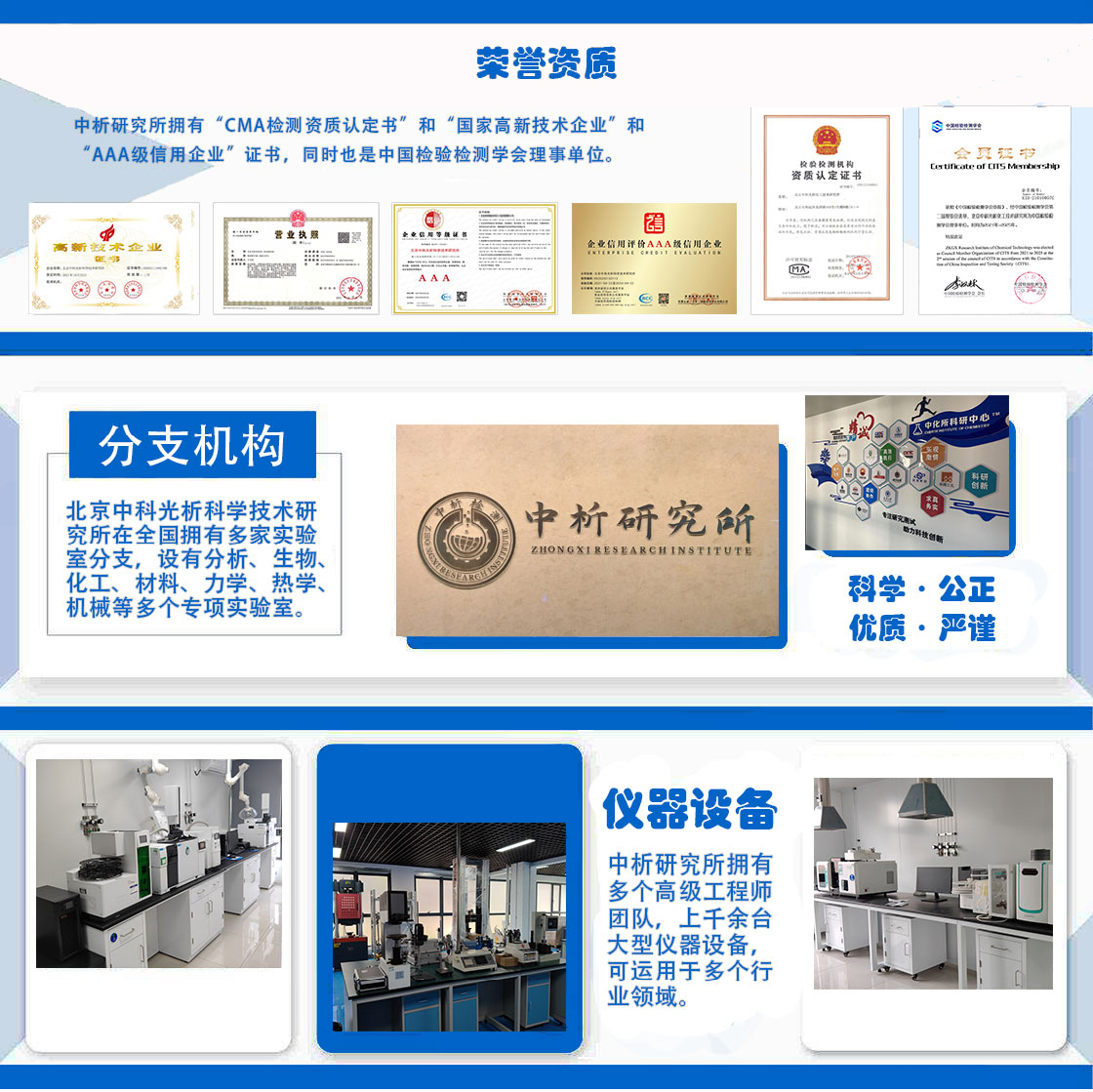
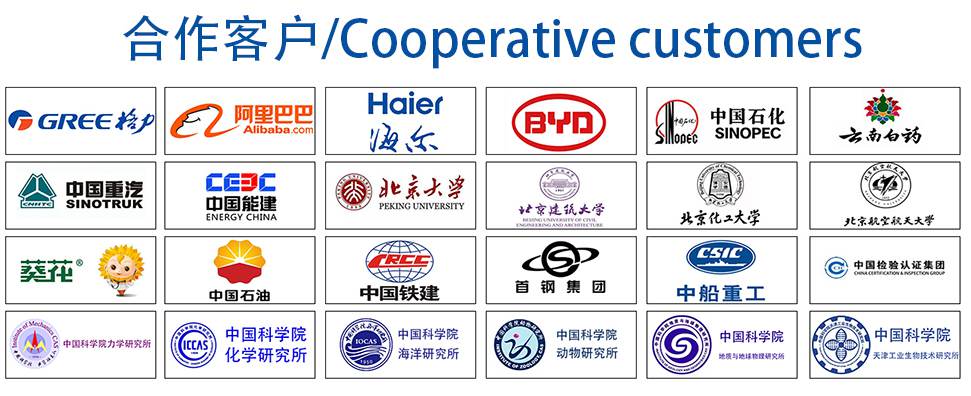