金刚石拉丝模检测的核心意义
金刚石拉丝模作为金属线材加工领域的核心工具,其质量直接影响线材的尺寸精度、表面光洁度及生产效率。随着精密制造行业对线材质量要求的提升(如电子元器件、航空航天导线等),拉丝模的检测已成为保障产品一致性和延长模具寿命的关键环节。其检测项目需覆盖几何精度、材料性能、表面状态等维度,确保模具从宏观到微观的全面性能达标。
检测项目一:孔径尺寸与形状精度
通过高分辨率三坐标测量仪或激光扫描仪,对拉丝模工作区(压缩区、定径区、出口区)的孔径进行纳米级测量。重点关注定径区直径偏差(允许误差±0.5μm)、椭圆度(≤0.3μm)及锥度变化,确保线材拉伸过程中的均匀受力。特殊线材加工还需检测异形孔结构(如矩形、六角形)的轮廓精度。
检测项目二:表面粗糙度与缺陷分析
采用白光干涉仪或原子力显微镜(AFM)对模孔内壁进行三维形貌分析,检测Ra值(通常要求≤0.05μm)和Rz值。同步检查微裂纹、崩缺、金刚石层脱落等缺陷,尤其关注压缩区与定径区交界处的应力集中区域。对于多晶金刚石(PCD)模具,还需评估晶粒分布的均匀性。
检测项目三:硬度和耐磨性能验证
使用纳米压痕仪测量金刚石涂层的维氏硬度(需≥8000HV),并通过加速磨损试验模拟实际工况。设置标准载荷下(如200N)的连续摩擦测试,记录模孔尺寸变化曲线,评估涂层结合强度和抗塑性变形能力。针对钨钢基体,需额外检测基材硬度(HRA≥90)与热膨胀系数匹配性。
检测项目四:内孔几何参数动态监测
采用工业内窥镜与机器视觉系统结合的方式,在模拟拉伸过程中实时观测金属流动状态。通过高速摄像机记录线材表面划痕生成情况,反向推导模孔内壁的平滑度与过渡区角度合理性。对超细线模具(孔径<0.1mm)需采用X射线断层扫描进行三维重构分析。
检测项目五:热稳定性与耐腐蚀测试
在高温试验箱中模拟连续作业环境(通常设定300-500℃),检测孔径的热膨胀变形量(要求≤0.1%)。通过盐雾试验(72h)和酸碱腐蚀试验,评估模具在特殊工况下的抗腐蚀能力。对用于铜合金等活性金属加工的模具,需重点检查金刚石涂层与金属蒸汽的化学反应情况。
全生命周期质量管控体系
现代检测技术已形成从原料筛选到报废评估的全流程体系:使用XRD分析金刚石纯度(C含量≥99.9%),EDS检测结合层元素组成,超声波探伤排查内部缺陷。结合大数据平台对历史检测数据进行趋势分析,实现剩余寿命预测与预防性维护决策支持,使模具报废率降低40%以上。
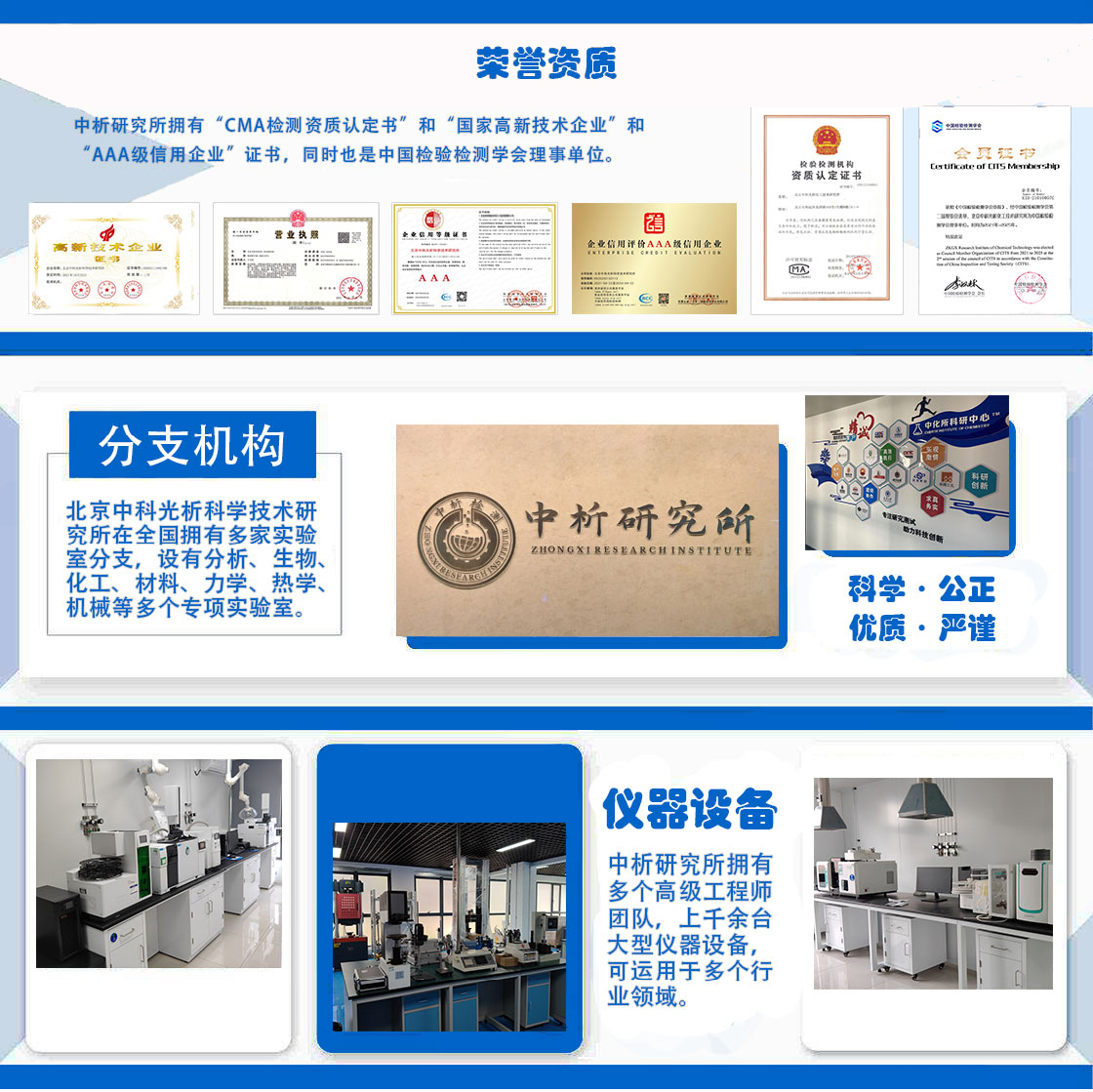
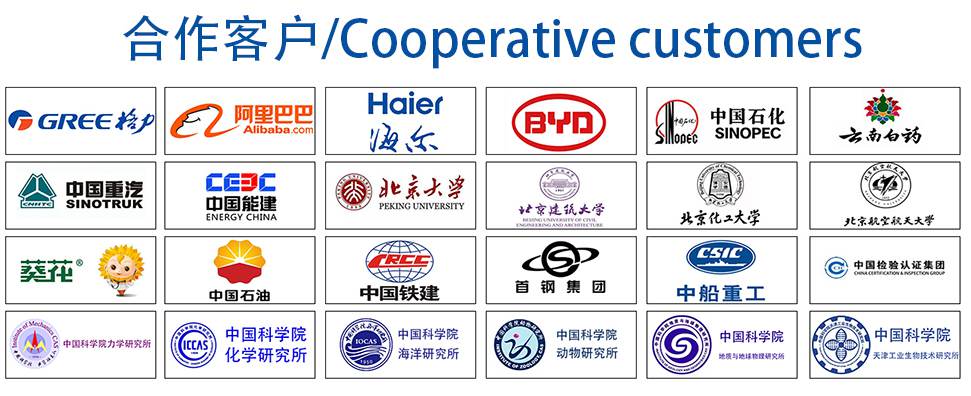