轮辋检测:确保行车安全的核心环节
作为汽车与地面直接接触的核心承载部件,轮辋的质量直接影响着车辆的行驶安全性和操控稳定性。轮辋检测是通过专业设备和技术手段对轮毂的各项性能参数进行系统性验证的过程,涵盖尺寸精度、材料强度、动平衡等20余项关键指标。随着汽车工业对轻量化、高强度材料的广泛应用,以及新能源车对轮辋载荷要求的提升,现代轮辋检测已形成涵盖原材料检测、成品验证、服役监测的全生命周期质量控制体系。
核心检测项目解析
1. 尺寸精度检测
使用三坐标测量仪(CMM)对轮辋的直径、宽度、偏距(ET值)、中心孔尺寸等关键几何参数进行微米级测量,确保与轮胎和车轴的匹配精度。其中轮辋边缘的径向跳动量需控制在±0.5mm以内,轴向跳动量不超过±0.3mm。
2. 材料性能检测
通过光谱分析仪验证铝合金轮辋的合金成分(如Si、Mg含量),采用万能材料试验机进行拉伸试验,确保抗拉强度≥310MPa,屈服强度≥250MPa。X射线探伤可检出铸造过程中产生的气孔、裂纹等内部缺陷。
3. 动平衡检测
在高速旋转试验台上模拟车轮转动,使用激光传感器检测不平衡量。乘用车轮辋要求不平衡量≤15g·cm,重型车辆需≤30g·cm。检测时需考虑配重块的合理分布方案。
4. 表面质量检测
采用工业内窥镜检测轮辐背面等隐蔽区域,运用光泽度计测量漆面光泽度(60°角测量值应≥85GU)。盐雾试验需通过96小时中性盐雾测试,涂层无起泡脱落现象。
特殊工况专项检测
5. 冲击试验
依据JWL标准进行13°冲击试验:将轮辋固定在专用台架上,用527kg重锤从230mm高度进行径向冲击,检测后轮辋不得出现断裂或泄露。
6. 弯曲疲劳试验
在液压伺服试验机上模拟车辆转弯时的侧向载荷,要求铝合金轮辋承受10^6次循环载荷后无结构性损伤,试验载荷根据轮辋规格可达2000-5000N·m。
7. 气密性检测
采用氦质谱检漏法精确检测轮辋与轮胎结合面的密封性能,泄漏率需≤1×10^-5 Pa·m³/s。对于真空胎轮辋,需额外进行20kPa负压保持测试。
智能化检测新趋势
当前行业正在推广基于机器视觉的自动检测系统,可实现轮辋表面缺陷的AI识别,检测速度可达120件/小时。激光三维扫描技术能构建轮辋的数字化双胞胎,实现全尺寸数据的云存储和可追溯管理。建议生产企业每季度进行第三方检测,并建立轮辋质量数据库进行预防性维护分析。
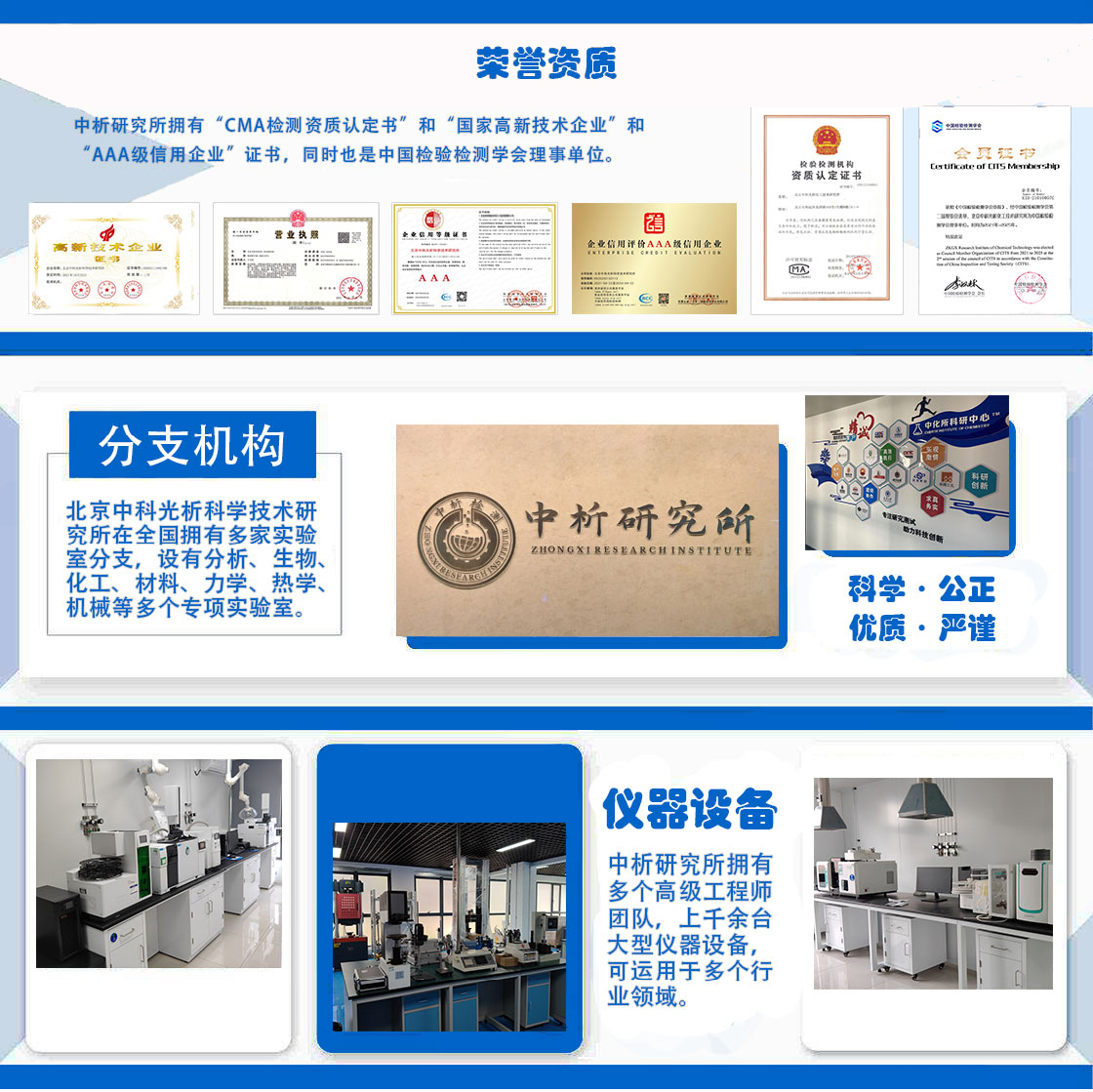
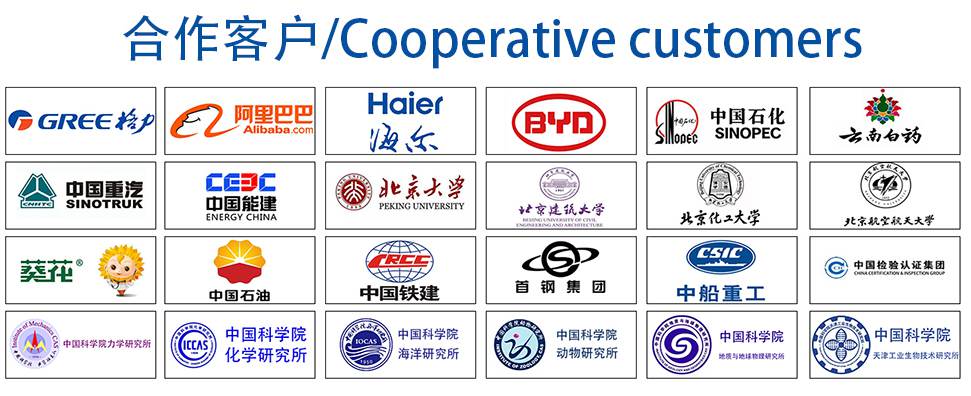