电机及控制器检测的重要性与核心目标
随着工业自动化、新能源汽车及智能装备等领域的快速发展,电机及控制器作为核心动力单元,其性能稳定性与可靠性直接关系到设备运行效率、能耗水平及安全性。电机及控制器检测是通过系统化测试手段,验证其设计参数、功能实现、环境适应性及耐久性的关键环节。检测不仅能够预防因部件故障引发的安全隐患,还能通过优化运行参数延长设备寿命,降低维护成本。在新能源领域,严格的电机能效检测更是实现节能减排目标的重要支撑。
电机检测的核心项目
电机的检测项目涵盖电气性能、机械特性及环境适应性三大维度:
1. 电气性能检测:包括绕组电阻测试、绝缘电阻测量(500V/1000V兆欧表)、耐压试验(1kV~3kV AC)、空载电流/功率检测以及负载工况下的效率分析。通过动态负载测试可获取转矩-转速特性曲线,评估电机输出能力的匹配度。
2. 机械性能检测:振动频谱分析(ISO 10816标准)用于识别轴承磨损或转子失衡问题;噪音测试(背景噪音≤30dB(A))可反映装配精度;温升试验(持续满载运行4小时)验证散热设计的有效性。
3. 环境适应性检测:高低温循环测试(-40℃~120℃)、湿热试验(湿度95% RH)、防护等级验证(IP54/IP67)及盐雾腐蚀测试,确保电机在极端条件下的可靠性。
控制器检测的关键指标
控制器作为电机的"大脑",检测需聚焦功能完整性与响应精度:
1. 控制精度验证:通过阶跃响应测试评估PID参数调节效果,PWM输出波形分析(示波器采样率≥100MHz)确保驱动信号无畸变,转速闭环控制误差需≤±0.5%。
2. 保护功能测试:模拟过流(150%额定电流)、过压(120%标称电压)、欠压(70%标称电压)及过热(外壳温度≥85℃)工况,验证保护阈值触发时间(典型值≤50ms)。
3. 通讯协议兼容性:针对CAN、RS485等工业总线,检测数据帧传输成功率(要求≥99.99%)及故障码反馈机制,确保与上位机系统的无缝对接。
系统级联调与耐久性测试
在完成单体验证后,需进行电机-控制器联合测试:
1. 动态响应匹配度:通过加速/减速曲线(如S型加减速)测试,评估转矩波动范围(目标≤±5%额定转矩),检测转速超调量(应≤2%设定值)。
2. 持续运行耐久性:按照IEC 60034-1标准进行1000小时满载循环测试,监测效率衰减率(允许≤3%),同时记录关键部件(如IGBT模块)的温升趋势。
3. 能效等级评定:依据GB 18613或IE4/IE5标准,通过输入-输出功率差值计算综合能效,高效电机要求η≥94%(10kW级)。
智能化检测技术的发展趋势
当前检测技术正向自动化、数字化方向演进:基于边缘计算的在线监测系统可实时采集振动、电流谐波等特征参数;机器学习算法用于早期故障预警(准确率>90%);数字孪生技术通过虚拟调试降低实物测试成本。这些创新手段将推动电机及控制器检测进入精准化、预测性维护的新阶段。
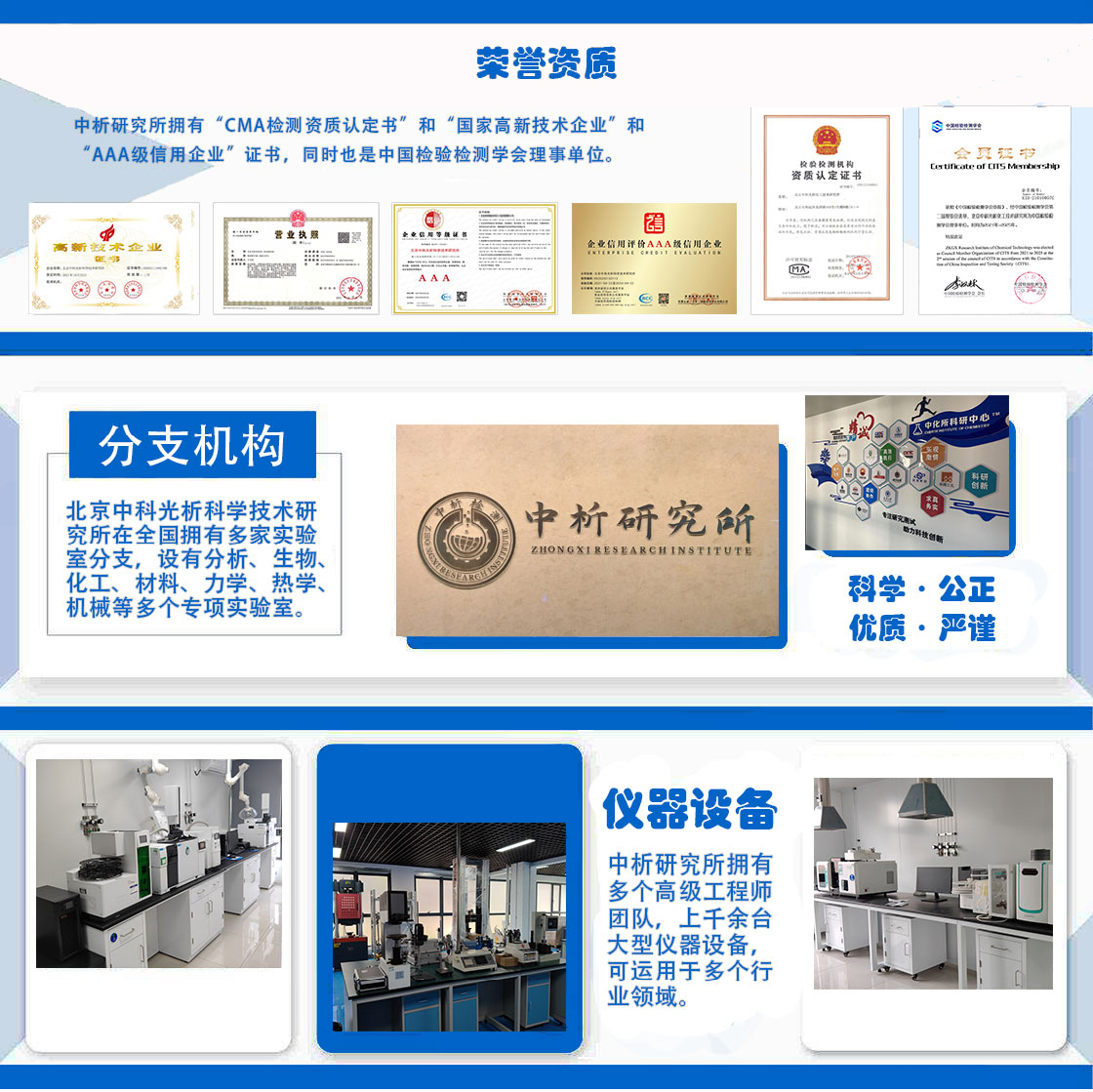
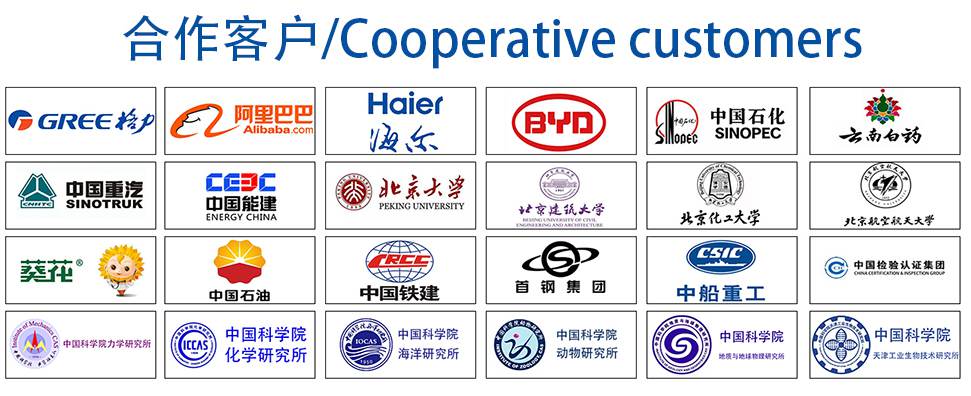