冲模检测的重要性及核心流程
冲模作为工业生产中金属冲压成型的核心工具,其精度与性能直接关系产品质量和生产效率。冲模检测是通过系统化的检验手段对模具尺寸、形位公差、表面状态及功能性进行全面评估的过程,旨在确保模具符合设计标准并满足批量生产的稳定性要求。随着制造业对精密化、自动化的需求提升,冲模检测已由传统的人工目测升级为数字化、智能化的综合检测体系,覆盖模具全生命周期管理。
冲模检测核心项目清单
1. 尺寸精度检测
使用三坐标测量仪(CMM)或激光扫描设备对模具型腔、刃口尺寸、导柱导套配合间隙进行微米级测量,比对设计图纸公差要求。重点关注冲头与凹模的匹配度、分型面平面度以及多工位模具的步距累积误差,确保冲压件尺寸一致性。
2. 表面质量分析
通过金相显微镜、粗糙度仪检测模具工作面划痕、龟裂、氧化等缺陷,评估表面粗糙度Ra值是否控制在0.4μm以内。针对TD处理、PVD镀层等特殊工艺需进行膜厚检测与附着力测试,防止剥落导致的产品拉伤问题。
3. 材料性能测试
采用洛氏硬度计(HRC)测定模具钢基体硬度,确认热处理工艺有效性。通过超声波探伤仪排查内部气孔、夹杂物等冶金缺陷,同时使用光谱分析仪验证材料成分是否达到SKD11、DC53等标称牌号要求。
4. 动态配合检测
在模拟冲压工况下,通过高速摄像系统捕捉模具闭合过程,分析卸料板运动轨迹、弹簧复位精度及氮气弹簧压力曲线。使用压力传感器监测冲裁力波动,识别因模具间隙偏差引起的异常载荷。
5. 寿命评估与失效分析
定期统计模具维修频次与单次修模量,结合显微硬度梯度测试评估表面硬化层损耗情况。对崩刃、塌角等失效部位进行SEM电镜扫描,判定失效模式属于疲劳断裂、磨粒磨损还是粘着磨损,针对性优化模具材料或润滑方案。
智能化检测技术应用
当前主流检测方案已融合工业CT断层扫描、AI视觉识别等齐全技术。通过建立三维数字孪生模型实现虚拟装配验证,采用机器学习算法对历史检测数据进行趋势预测,显著提升缺陷检出率与模具维护前瞻性。
系统性冲模检测不仅能降低产品不良率,还可延长模具使用寿命30%-50%。建议企业建立包含首检、巡检、修模后复检的全流程质控体系,结合TPM管理模式实现模具全生命周期健康管理。
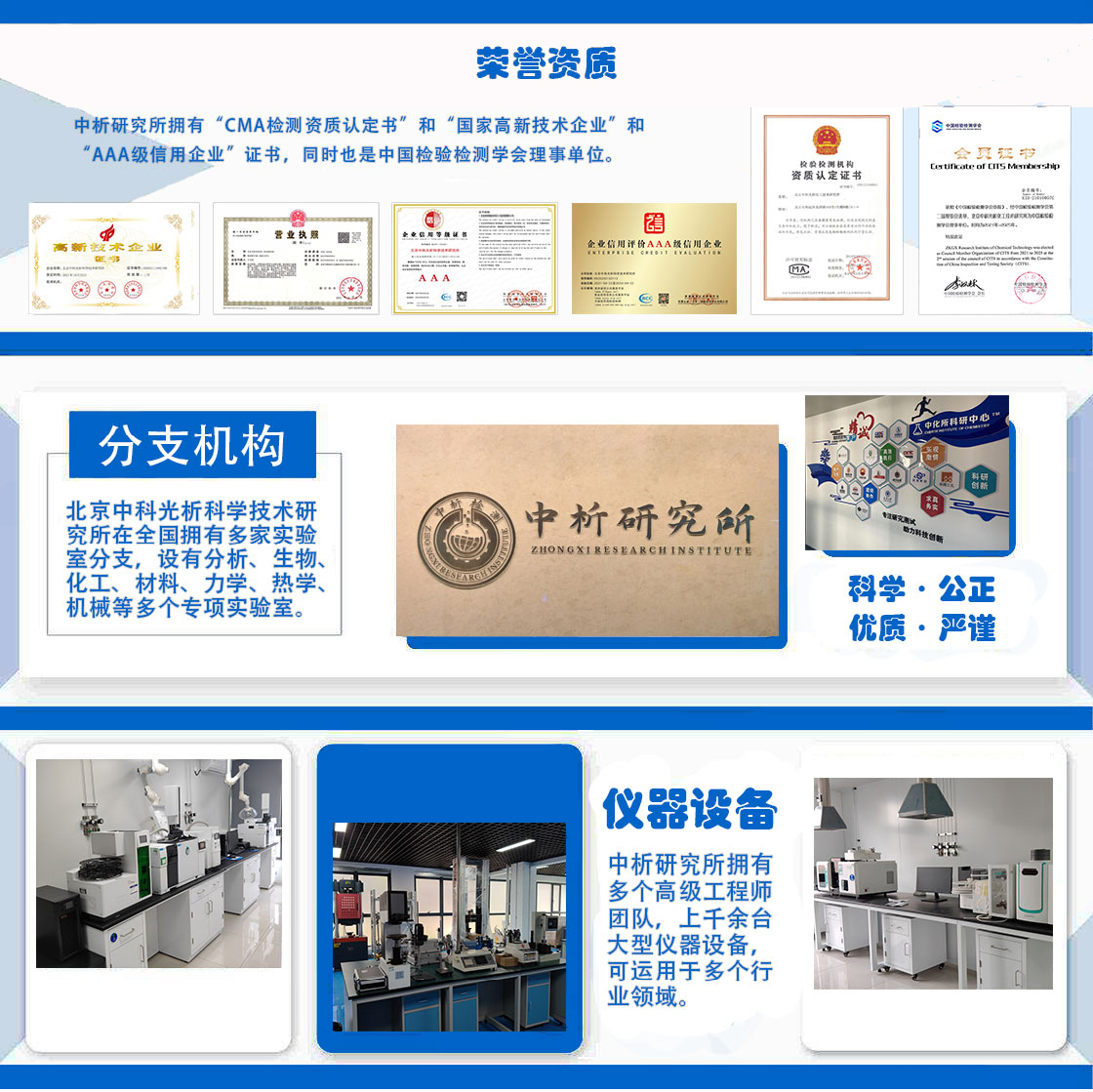
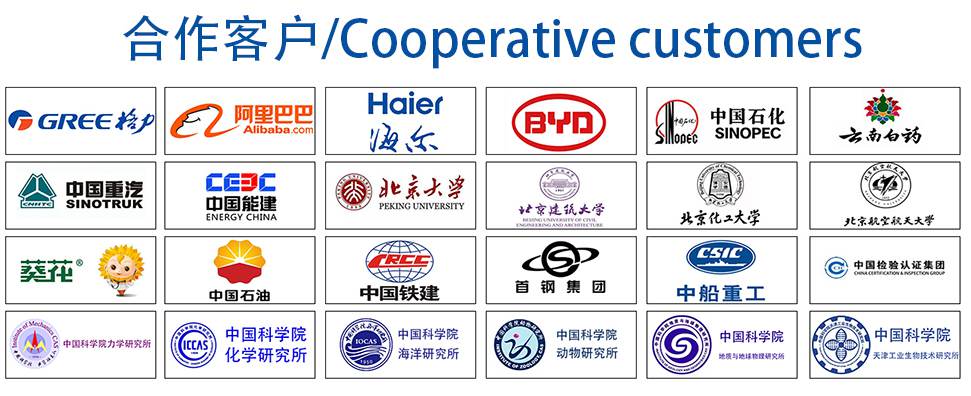