电池零部件检测的重要性与核心项目解析
随着新能源产业的快速发展,动力电池作为电动汽车、储能系统的核心部件,其安全性和可靠性受到广泛关注。电池零部件检测是保障电池性能、延长使用寿命及预防安全隐患的关键环节。据统计,超过60%的电池故障源于零部件质量问题,因此从材料到组件的全流程检测已成为行业标准。通过科学的检测手段,可精准识别电极材料缺陷、电解液泄漏、隔膜完整性等问题,为电池的制造工艺优化提供数据支撑。
电芯核心组件检测
电芯作为电池的"心脏",需进行多维度检测:电极片需通过X射线衍射仪分析材料晶体结构,确保能量密度达标;极耳焊接强度需承受25N以上的拉力测试;电解液纯度需用ICP-MS检测金属杂质含量,控制值需低于0.5ppm。近年新型激光粒度仪的应用,可将正极材料粒度分布偏差控制在±0.8μm以内。
隔膜性能检测体系
锂电池隔膜需通过穿刺强度(≥300g/25μm)、热收缩率(150℃/1h≤5%)等核心指标检测。采用Gurley法测试透气度时,标准要求每100cc空气通过时间在200-500秒区间。微孔结构的SEM电镜分析可发现0.1μm级缺陷,配合氦质谱检漏仪能检出10^-6 Pa·m³/s级泄漏速率。
外壳结构可靠性测试
电池外壳需通过IP67防水测试、盐雾试验(500h无锈蚀)及跌落测试(1.2m高度自由跌落无破裂)。采用三维数字图像相关技术(3D-DIC)可实时监测外壳在挤压测试中的形变过程,配合200kN压力机模拟极端工况下的结构完整性。
BMS系统功能验证
电池管理系统(BMS)需通过CAN总线通讯测试、均衡电流精度测试(误差≤±2%)、过充/过放保护响应测试(动作时间<100ms)。在-40℃至85℃的温度循环测试中,系统采样精度需保持±5mV以内。最新的ISO 26262标准要求BMS达到ASIL-C级功能安全等级。
检测技术发展趋势
当前在线检测技术已实现0.1mm级极片缺陷实时识别,AI算法对电芯分容的匹配准确率提升至98%。同步辐射X射线成像技术可透视电池内部三维结构,量子级联激光光谱仪能实时监测电解液分解产物。未来数字孪生技术的应用,将实现电池全生命周期的虚拟化检测跟踪。
通过构建涵盖材料特性、机械性能、电气参数和环境适应性的检测体系,电池零部件的质量控制正从经验导向转向数据驱动。这不仅关系到单个电池的性能表现,更是整个新能源产业链安全发展的重要基石。
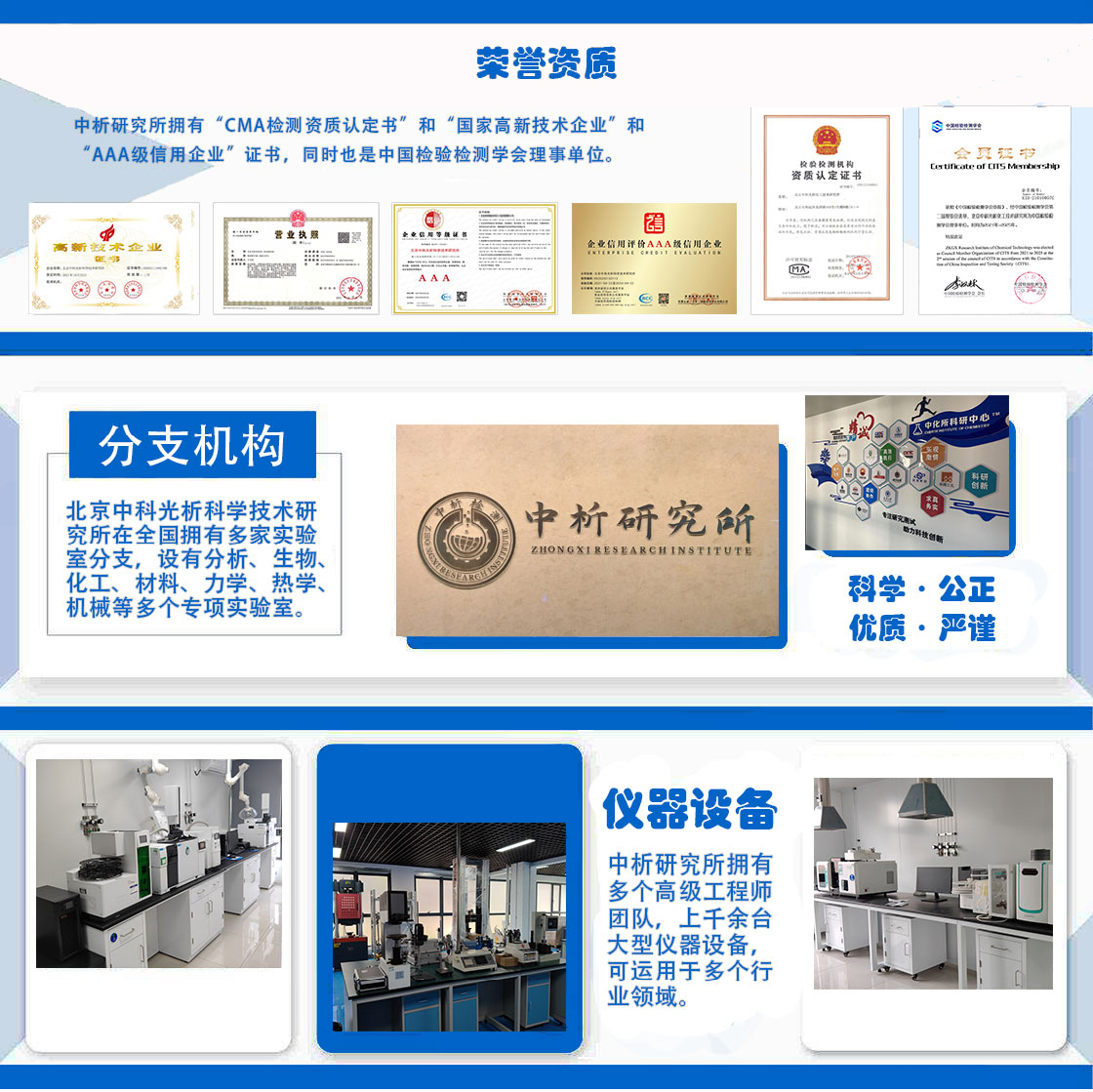
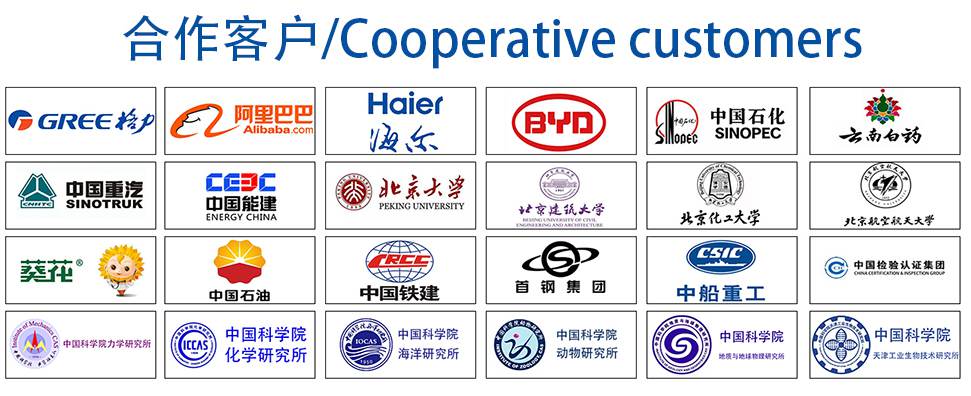