塑料异型材挤出模检测的重要性
塑料异型材挤出模是生产门窗型材、装饰条、密封件等复杂截面塑料制品的关键工具。其质量直接决定产品尺寸精度、表面光洁度及力学性能,进而影响终端产品的装配效果和使用寿命。随着行业对节能、环保及产品定制化需求的提升,挤出模的检测技术已成为保障生产效率与产品质量的核心环节。通过系统性检测,可避免因模具偏差导致的材料浪费、停机维修等问题,同时确保符合GB/T 8814-2020《建筑门窗用未增塑聚氯乙烯(PVC-U)型材》等国家标准及客户定制化要求。
核心检测项目及方法
1. 尺寸精度检测
使用三坐标测量仪(CMM)或激光扫描仪对模具流道、定型段截面进行三维数据采集,与设计图纸对比分析公差(一般要求±0.05mm以内)。重点检查定型模块的平行度、对称度及关键定位孔位偏差。
2. 表面质量评估
通过目视观察、金相显微镜或表面粗糙度仪检测模具型腔的抛光等级(通常需达到Ra≤0.2μm)。对电镀层厚度(建议镍层≥15μm)进行X射线荧光光谱(XRF)分析,确保耐磨性与脱模性能。
3. 结构强度与热变形测试
采用液压压力机模拟实际挤出压力(通常20-50MPa),检测模具在高温(180-220℃)下的抗蠕变能力。结合红外热成像技术,分析温度场分布是否均匀,避免局部过热导致的变形开裂。
4. 流量平衡性验证
通过熔体流动速率(MFR)试验机与模流分析软件(如Moldflow)模拟材料在流道内的填充状态,优化分流锥角度(建议30°-60°)和阻尼块设计,确保各区域出料速度一致性(偏差≤5%)。
5. 功能性耐久试验
在连续生产环境下进行寿命测试(通常要求≥50万米挤出量),记录模唇磨损量、定型块配合间隙变化等数据。定期进行腐蚀介质浸泡试验(如5%HCl溶液48h),评估模具材料的耐化学腐蚀性能。
智能化检测技术应用趋势
近年来,工业CT断层扫描、机器视觉在线监测系统及AI缺陷识别算法逐步应用于挤出模检测领域。例如,基于深度学习的表面缺陷分类模型可实现微米级划痕、气孔的自动判定,检测效率提升40%以上。同时,数字孪生技术通过实时同步模具工况数据,为预防性维护提供决策支持。
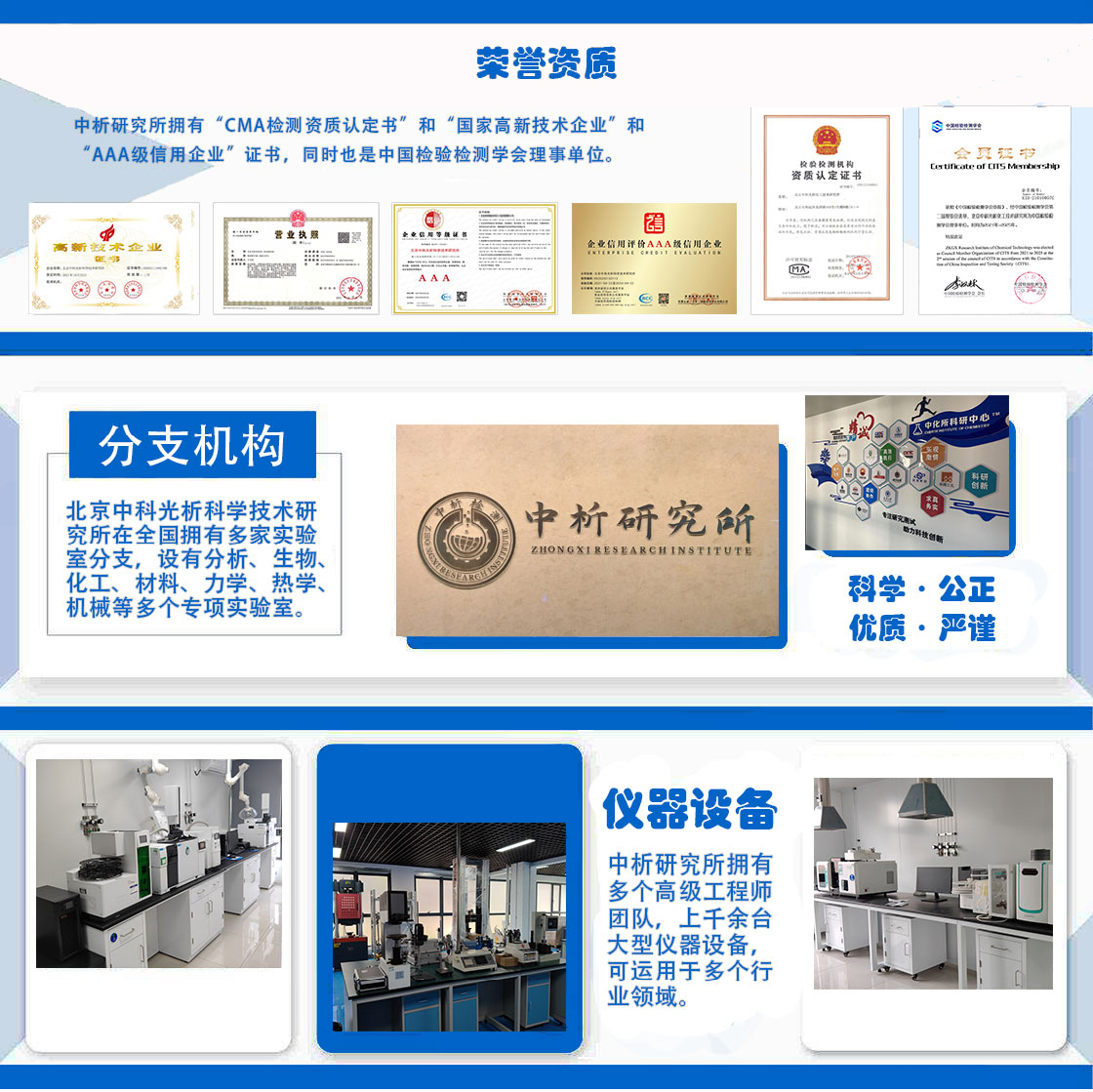
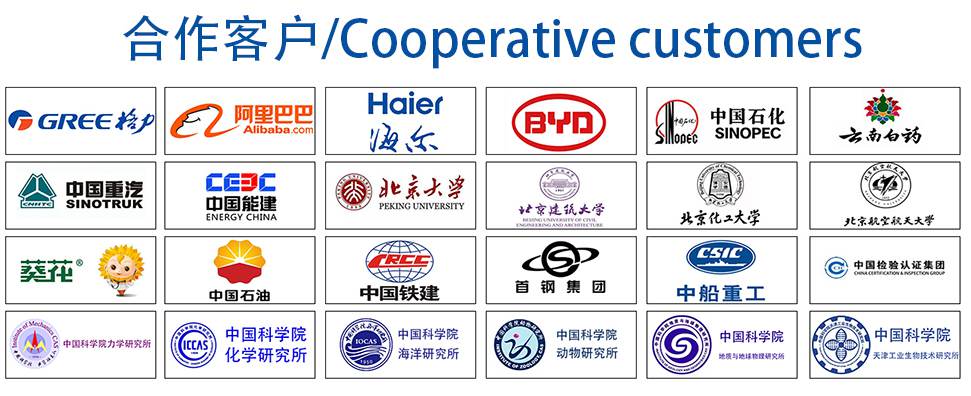