力车轮胎模具检测的重要性与关键项目解析
力车轮胎模具作为自行车、电动车等非机动车辆轮胎生产的核心工具,其质量直接影响轮胎的成型精度、使用寿命和安全性。随着生产工艺的不断升级,模具检测已成为保障产品质量、降低返工率的关键环节。一套完整的检测流程需覆盖尺寸公差、材料性能、表面质量等20余项指标,通过科学化、标准化的检验手段确保模具满足严苛的工业要求。本文将从核心检测项目切入,详解力车轮胎模具质量控制的技术要点。
一、尺寸精度检测
采用三坐标测量仪对模具分型面、花纹沟槽深度、气孔位置等关键尺寸进行三维扫描,精度需达到±0.02mm。重点检测: 1. 胎冠弧度半径偏差 2. 加强筋分布对称度 3. 排气槽宽度一致性 4. 合模面平行度误差 通过数字比对技术生成三维偏差色谱图,直观呈现尺寸超差区域。
二、材料性能检测
使用洛氏硬度计(HRC标准)检测模具钢材表面硬度(标准值58-62HRC),通过金相显微镜观察材料微观组织是否存在碳化物偏析。同步进行: 1. 高温抗变形测试(模拟200℃硫化环境) 2. 冲击韧性试验(夏比冲击值≥35J/cm²) 3. 耐磨性评估(摩擦系数≤0.15) 确保模具在高温高压工况下的结构稳定性。
三、表面质量检测
运用白光干涉仪检测型腔表面粗糙度(Ra≤0.8μm),通过工业内窥镜检查隐蔽部位是否存在机械损伤。特别关注: 1. 花纹块过渡区抛光质量 2. 电火花加工面重熔层厚度 3. 激光雕刻文字清晰度 4. 防粘涂层均匀性(厚度0.03-0.05mm) 表面缺陷可能导致轮胎脱模困难或产生飞边。
四、结构强度检测
采用有限元分析软件模拟模具在200吨合模力下的应力分布,配合应变片实测关键点变形量(应变量<0.1%)。着重验证: 1. 模套抗压强度(≥1200MPa) 2. 定位销剪切强度(安全系数≥3) 3. 楔形锁紧机构可靠性 4. 热膨胀补偿结构合理性 避免模具在长期使用中发生塑性变形。
五、使用性能验证
通过试模试验连续生产50模次轮胎,统计分析: 1. 脱模力变化曲线(波动值<10%) 2. 轮胎尺寸合格率(≥99.5%) 3. 模具温度场均匀性(温差≤5℃) 4. 排气效率(硫化气泡缺陷率<0.1%) 实际工况验证是检测流程的最终验收环节。
当前行业正推动智能检测技术的应用,如基于机器视觉的花纹比对系统、物联网模具寿命预测平台等,推动检测效率提升40%以上。规范的检测体系不仅能降低模具维护成本,更能为轮胎企业创造每套模具延长3-5万次使用周期的经济效益。
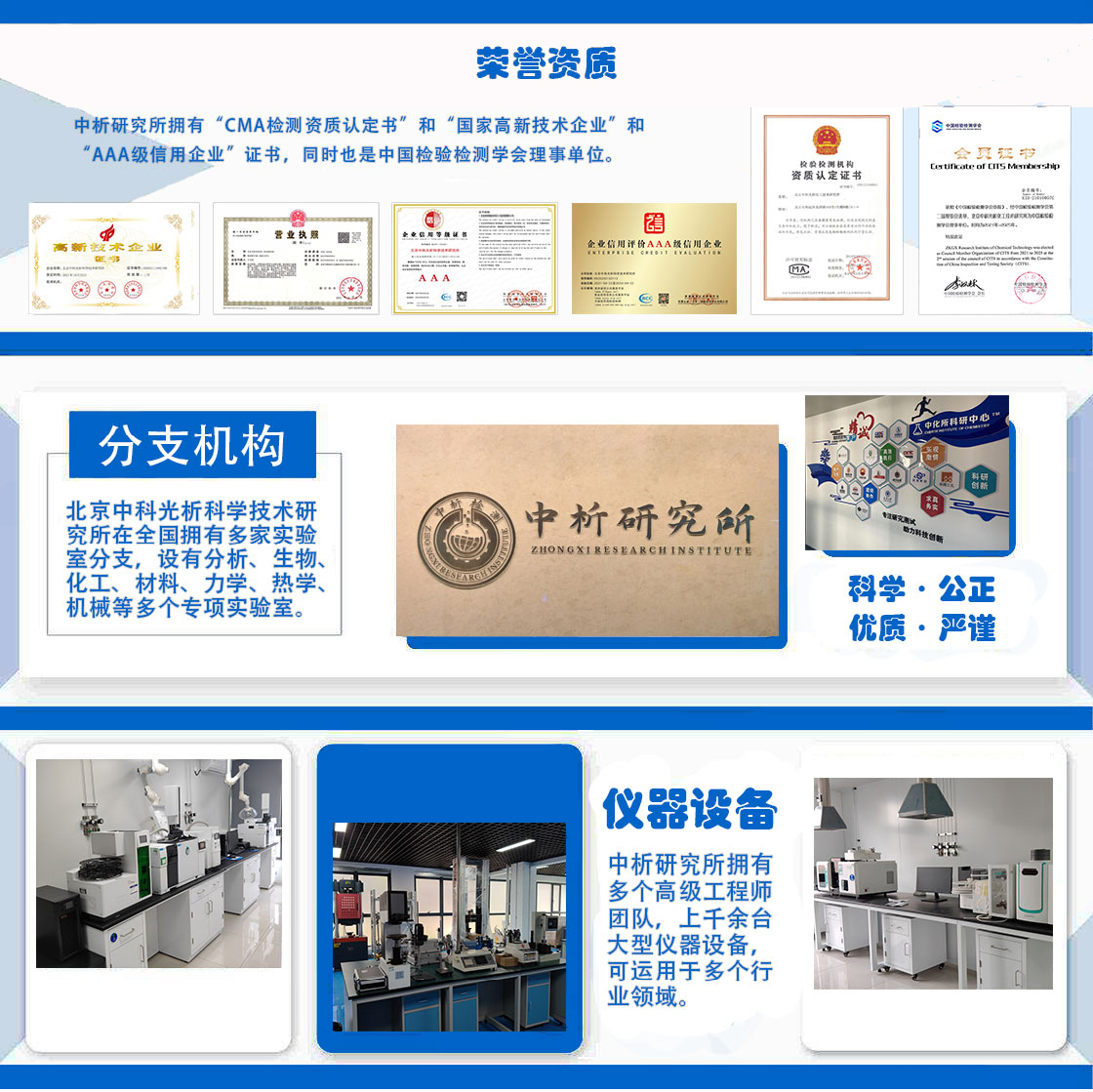
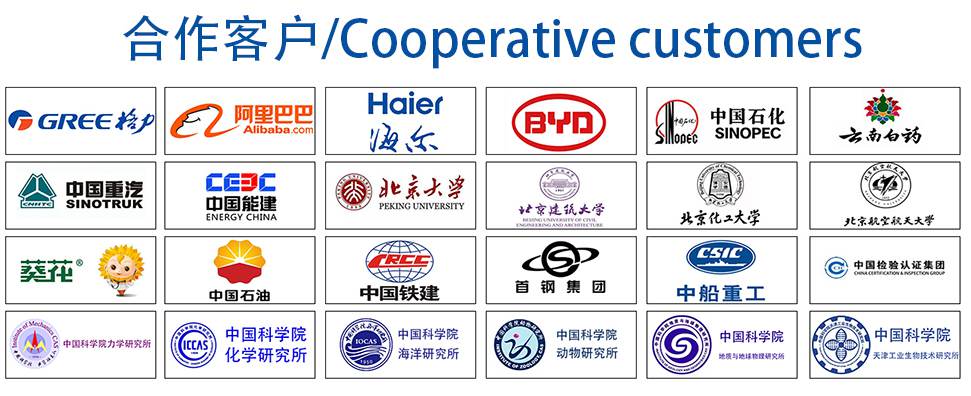