板料折弯模检测的重要性与流程解析
板料折弯模作为钣金加工中的核心工具,其精度和状态直接影响工件成型质量与生产效率。在长期使用过程中,模具可能因磨损、变形或材料疲劳导致性能下降,因此定期开展系统性检测是保障生产稳定性的关键环节。通过科学的检测手段,可以精准评估模具可用性,预测维修周期,避免因模具失效引发的批量性质量问题,同时延长模具使用寿命,降低企业综合成本。
核心检测项目清单
1. 模具材质检测
采用光谱分析仪验证模具材料成分是否符合设计要求,重点检测Cr、Mo、V等合金元素含量,确保材料具备足够的耐磨性和抗冲击性能。对于高频次使用的精密模具,需特别注意表面渗碳/氮化层的厚度均匀性检测。
2. 尺寸精度检测
使用三坐标测量仪对关键尺寸进行全尺寸扫描,包括:上下模闭合高度、V型开口尺寸、导向槽配合间隙等,允许公差需严格控制在±0.02mm以内。对于复杂曲面模具,需配合3D扫描技术进行三维形貌比对。
3. 表面粗糙度检测
通过表面轮廓仪测量模具工作面的Ra值,重点区域粗糙度应≤0.4μm。过高的粗糙度会导致板材表面划伤,同时影响脱模性能;而异常过低的数值可能掩盖细微裂纹缺陷。
4. 硬度检测
采用洛氏硬度计(HRC)多点检测模具工作面硬度,确保硬度值在58-62HRC范围内。特别注意硬度梯度的合理性,避免出现表面硬度过高导致的脆性断裂风险。
5. 角度与弧度检验
使用专用角度规和半径样板检测成型部位的几何特征,对于多段折弯模具需逐段验证角度过渡区的连续性。针对弹性回弹补偿设计,需通过试折验证实际成型角度与理论值偏差。
6. 导向机构检测
检查导柱/导套的配合间隙(应≤0.015mm),检测复位弹簧的压缩力衰减情况。对于液压式模具,需同步检测液压缸的同步精度和保压性能。
7. 刃口状态评估
使用20倍以上工业显微镜检查刃口是否存在崩刃、卷边等缺陷,测量刃口圆角半径变化。当圆角半径超过设计值30%时,需立即进行修复处理。
8. 装配精度验证
在专用检测平台上进行动态合模测试,使用激光位移传感器监测上下模的平行度误差(≤0.03mm/m),同时检测模具整体的水平度与紧固螺栓的预紧力均匀性。
9. 残余应力检测
采用X射线衍射法检测模具内部残余应力分布,重点分析应力集中区域。对于应力值超过材料屈服强度35%的模具,必须进行去应力退火处理。
检测周期与注意事项
建议每完成5000-8000次冲压进行预防性检测,在连续高强度使用时应缩短至2000次/次。检测过程需严格遵循温度补偿原则(20±1℃),检测后需建立完整的模具健康档案,包含3D数字孪生模型和维修履历记录。通过实施标准化检测流程,可使模具故障率降低60%以上,显著提升产线综合OEE指标。
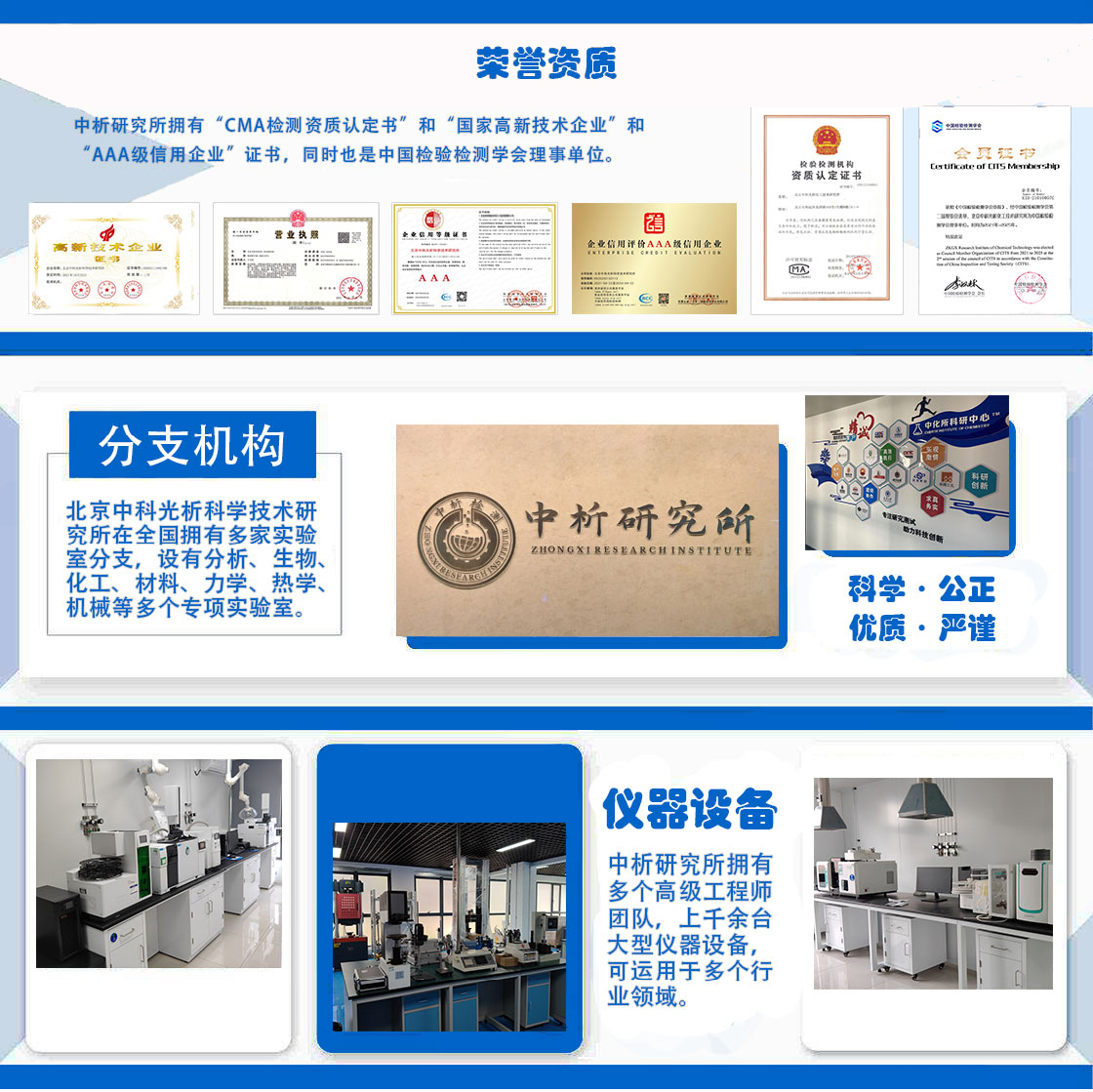
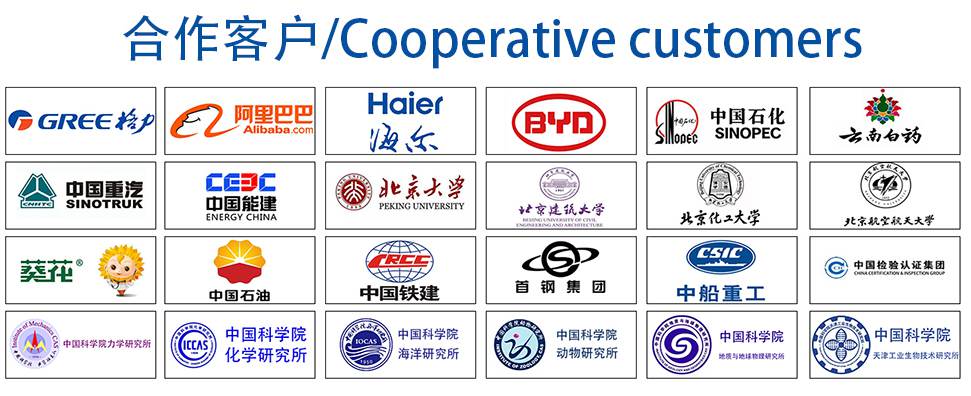