在玻璃制品生产过程中,玻璃模具的质量直接决定了产品的精度、外观和使用寿命。作为玻璃成型工艺的核心工具,模具的微小缺陷或尺寸偏差都可能导致成品出现气泡、划痕、变形等问题,甚至引发生产线停机。因此,玻璃模检测成为保障生产效率和产品质量的关键环节。通过系统化的检测流程,企业能够精准识别模具问题,延长模具使用寿命,同时降低废品率与生产成本。本文将围绕玻璃模具的核心检测项目展开详细介绍。
一、尺寸精度检测
通过三坐标测量仪(CMM)或激光扫描设备对模具的型腔尺寸、分型面精度、定位孔位置等关键参数进行测量,确保公差控制在±0.01mm以内,尤其关注模具闭合后的配合间隙检测,防止玻璃液泄漏或成型压力不均。
二、表面质量检测
采用工业显微镜、表面粗糙度仪及高清图像分析系统,检测模具工作面的划痕、麻点、氧化层脱落等缺陷。重点评估表面粗糙度(Ra值通常要求≤0.4μm),避免因表面不平整导致玻璃制品出现雾面或光折射异常。
三、材质成分与硬度测试
使用光谱分析仪检测模具材料的合金元素配比(如铬钼钒含量),结合洛氏硬度计测定表面硬度(HRC需达到50-55),确保模具具备足够的耐磨性和抗热疲劳性能。同时通过金相显微镜观察材料微观组织,排查晶粒粗大或夹杂物超标问题。
四、热变形与热传导性能检测
模拟实际工况进行高温循环测试(300-600℃),利用红外热像仪监测温度分布均匀性,通过应变传感器测量热膨胀变形量。同步检测模具的热导率,确保快速散热能力,避免局部过热导致玻璃粘模。
五、使用寿命预测与疲劳测试
通过高频次开合试验(超过10万次循环)评估模具的耐久性,结合超声波探伤检测内部裂纹扩展情况。建立三维有限元模型分析应力集中区域,预测模具在连续生产中的失效周期,为维护计划提供数据支持。
随着智能检测技术的发展,机器视觉、AI缺陷识别和在线监测系统正逐步应用于玻璃模检测领域。通过构建全生命周期的质量监控体系,企业不仅能提升检测效率,更能实现模具的预防性维护,为高质量玻璃制品的规模化生产奠定坚实基础。
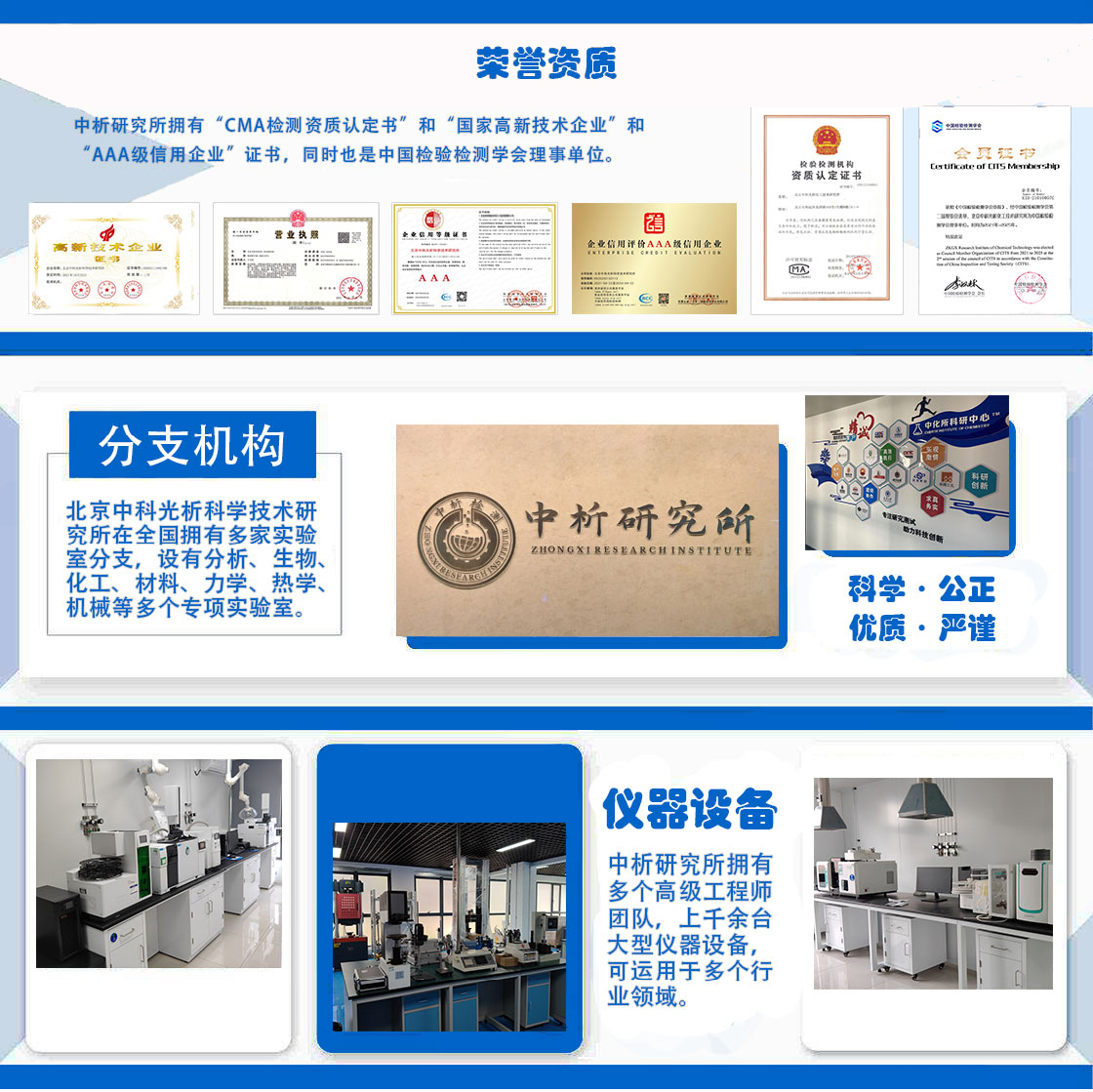
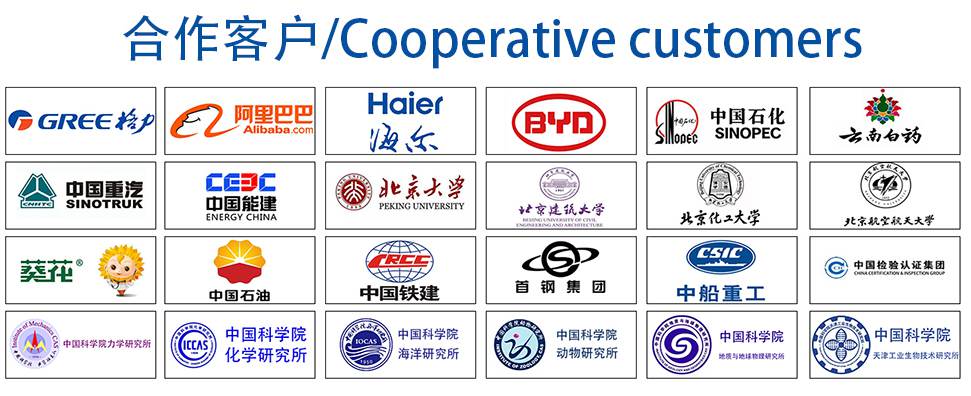