轴承油检测:保障设备高效运行的关键环节
在现代工业生产中,轴承作为旋转设备的核心部件,其润滑效果直接影响设备使用寿命和生产效率。而轴承油作为润滑系统的"血液",其理化性能的优劣直接决定了轴承的运转状态。专业化的轴承油检测已成为预防性维护体系中不可或缺的重要环节,通过科学分析油品质量,可提前发现潜在问题,避免突发性设备故障造成的经济损失。
核心检测项目解析
1. 粘度指标检测
采用旋转粘度计测量油品在40℃和100℃下的运动粘度,评估其温度适应性。粘度异常会导致油膜厚度不足或摩擦阻力增大,美国ASTM D445标准规定了精确的测试方法。
2. 水分含量测定
应用卡尔费休法(GB/T 11133)检测游离水和溶解水含量。当水分超过0.05%时,会加速油品氧化并引发金属表面点蚀,特别在高温高湿环境下需重点监控。
3. 污染度分析
使用激光颗粒计数器(ISO 4406标准)检测5μm、15μm等级颗粒物浓度。研究发现,80%的轴承早期失效与油液污染直接相关,严格控制NAS等级可延长轴承寿命3-5倍。
深度性能评估项目
4. 氧化安定性测试
通过旋转氧弹试验(ASTM D2272)测定油品抗氧化能力。运行2000小时后酸值(GB/T 7304)升高超过0.3mgKOH/g时,表明需立即换油。
5. 元素光谱分析
运用ICP发射光谱仪检测Fe、Cu、Si等磨损金属及添加剂元素含量。铁元素突增可能预示轴承滚道磨损,硅元素超标则提示密封失效或外部污染侵入。
6. 抗磨性能验证
四球试验机(GB/T 3142)测定最大无卡咬负荷PB值,优质轴承油的PB值应达到800N以上。某电厂案例显示,PB值下降30%后仅运行72小时即发生轴承烧结事故。
检测周期与实施建议
常规设备建议每运行2000小时或半年检测一次,关键设备应缩短至1000小时。建议搭建油液监测数据库,结合历史数据建立趋势分析模型。采用现场快速检测与实验室精密分析相结合的模式,既保证时效性又确保数据准确性。
通过系统的轴承油检测,企业可实现从"故障维修"到"预测性维护"的转变。某汽车制造厂的实践表明,实施标准化检测方案后,轴承相关故障率下降67%,年维护成本降低42万元。专业的油液检测不仅是技术手段,更是现代设备管理的重要战略工具。
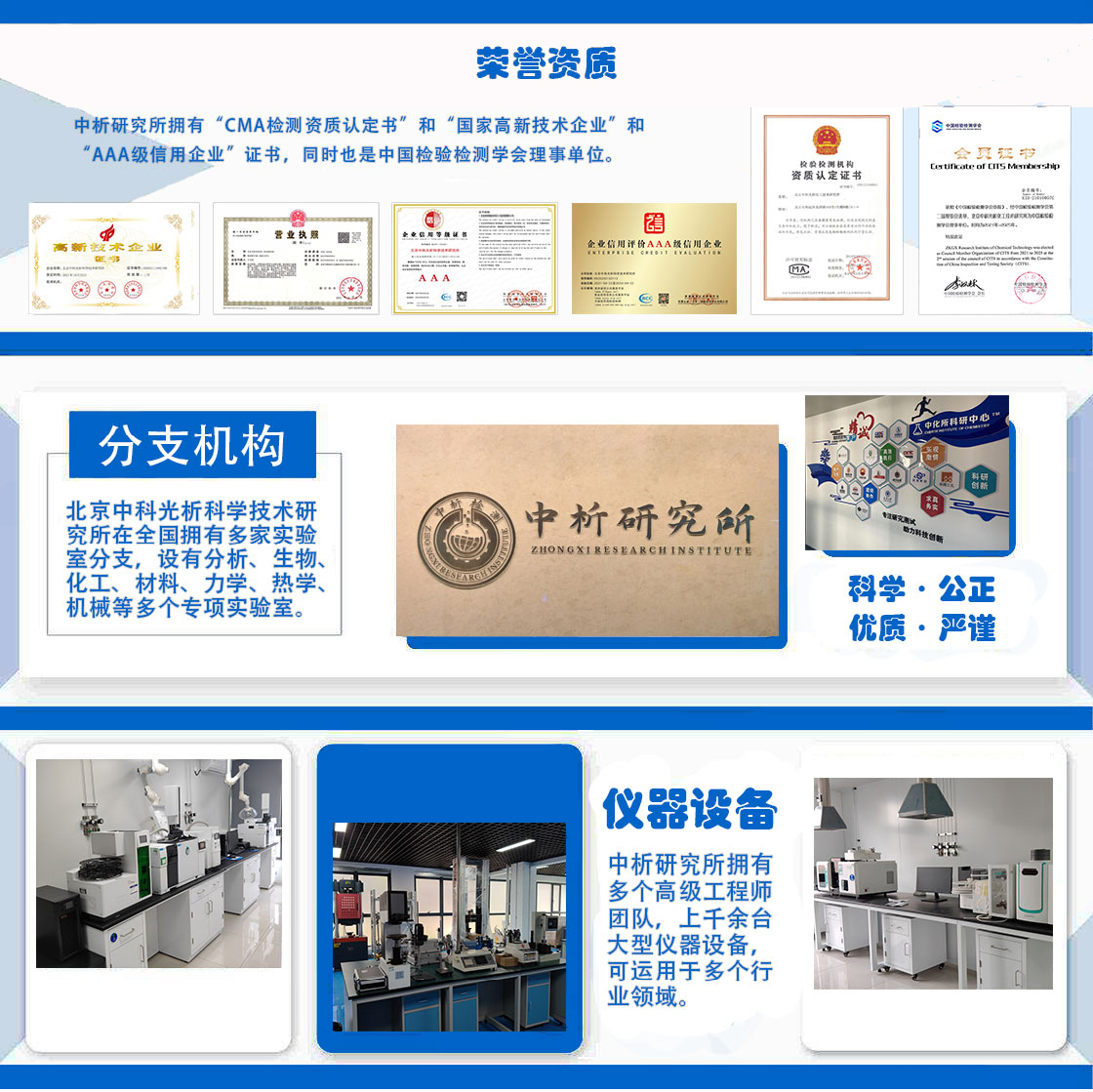
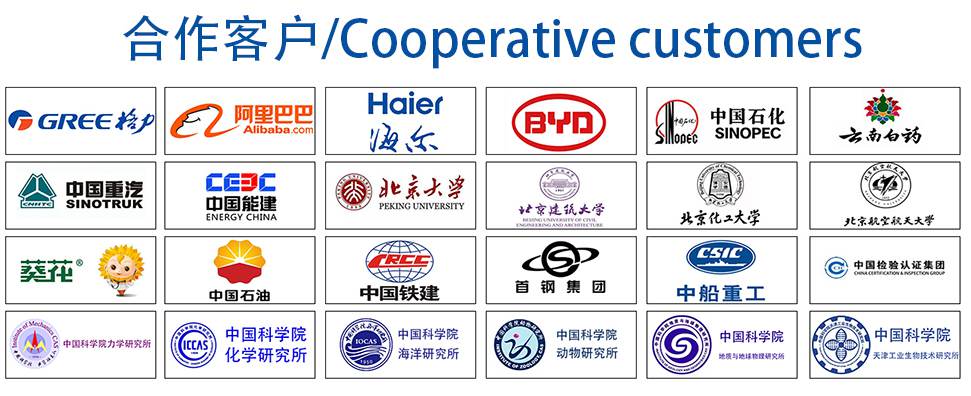