空气压缩机油检测的重要性与核心项目解析
空气压缩机油作为压缩机系统的"血液",其性能直接关系到设备运行效率、能耗水平及使用寿命。随着工业设备对可靠性要求的提升,定期开展空气压缩机油检测已成为预防性维护的关键环节。通过科学的检测分析,可及时发现油品劣化、污染物侵入等问题,避免因润滑失效导致的设备磨损、高温停机甚至重大故障,为企业节省30%以上的维修成本。
核心检测项目及技术要求
1. 运动粘度检测
采用GB/T 265标准,通过毛细管粘度计测定40℃和100℃下的运动粘度值。新油粘度应控制在ISO VG等级±10%范围,旧油粘度变化超过±15%需更换。
2. 酸值测定
依据GB/T 7304标准,检测油品中酸性物质含量。运行油酸值升高超过0.5mgKOH/g(与新油对比)时,提示氧化加剧,需考虑油品再生或更换。
3. 水分检测
执行GB/T 260蒸馏法,要求水分含量≤0.1%。水分超标会引发乳化、添加剂失效,需检查冷凝系统密封性并及时脱水处理。
4. 机械杂质分析
按照GB/T 511标准,使用溶剂稀释法测定固体颗粒含量。建议加装精密过滤器确保杂质含量<0.01%,当ISO清洁度代码超过18/16/13时应进行深度过滤。
5. 闪点测试
通过GB/T 267开口杯法检测,闪点下降值超过20℃时,表明油品遭受燃料稀释污染,需排查燃烧系统问题。
扩展检测与齐全分析技术
针对特殊工况可增加红外光谱分析(检测氧化产物)、原子发射光谱(监测磨损金属元素)、旋转氧弹试验(评估抗氧化性能)等项目。采用PQ指数分析可快速判断油品剩余使用寿命,结合在线油液监测系统可实现实时状态评估。
检测周期与标准建议
常规设备建议每运行2000小时或半年检测一次,关键机组应缩短至每季度检测。检测标准需结合ISO 6743-3A/B分类、设备制造商规范及实际工况综合确定。检测报告应包含历史数据对比、趋势分析及维护建议,为设备健康管理提供决策支持。
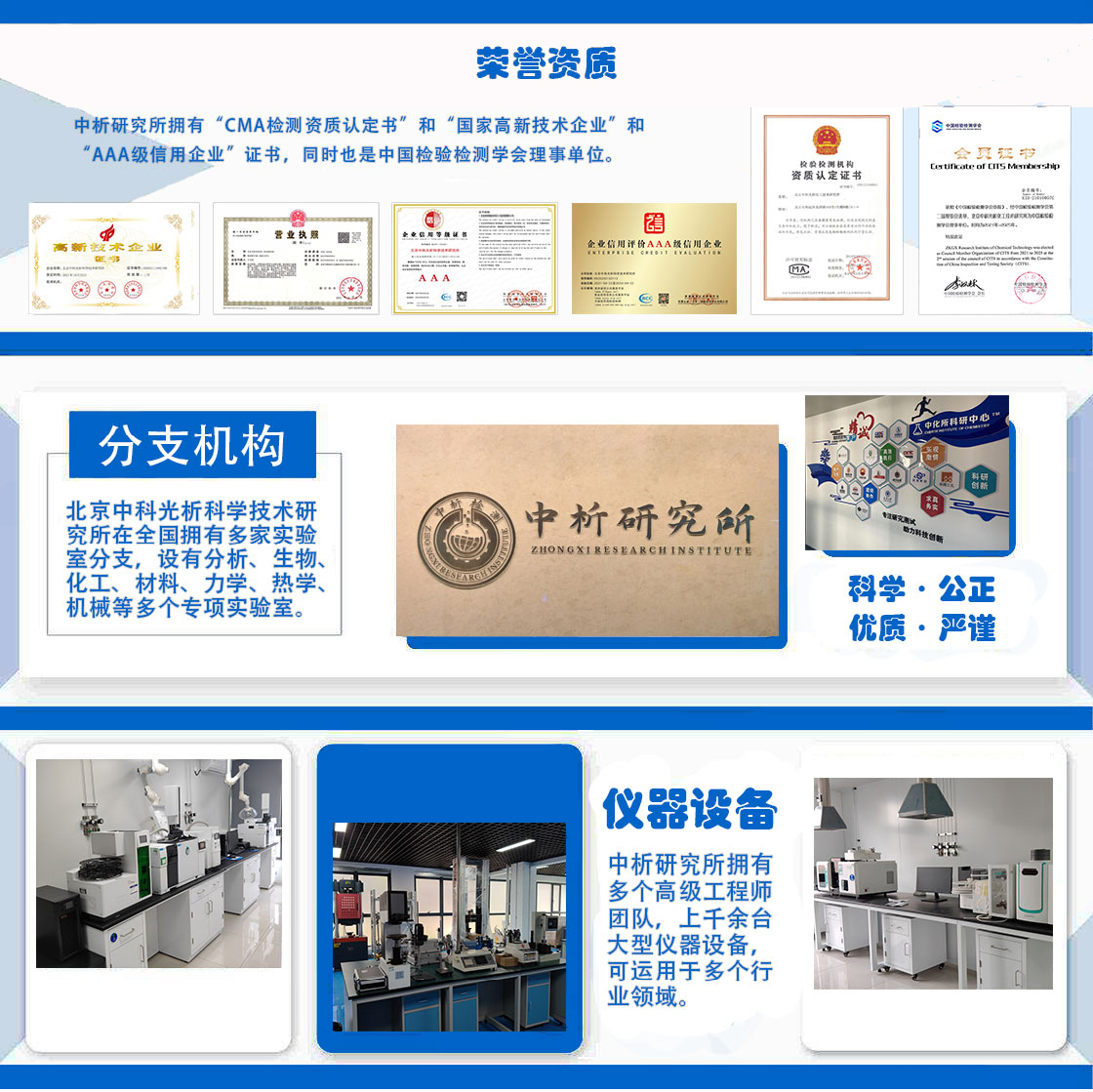
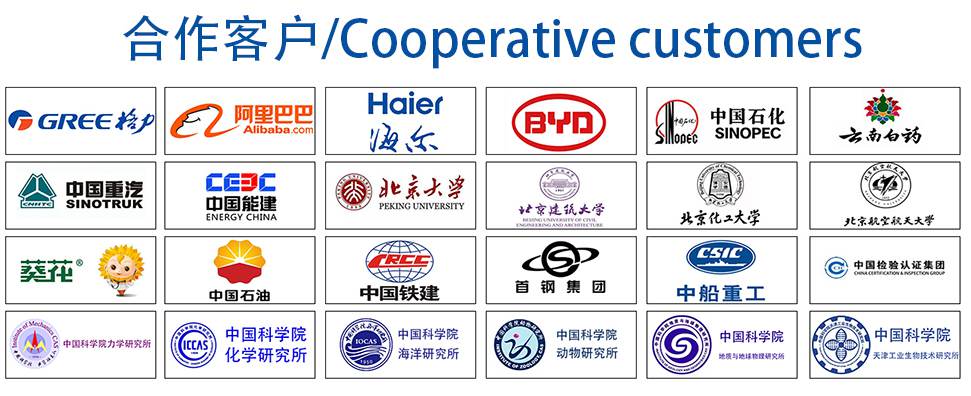