石油修井绞车检测的重要性
石油修井绞车是油田修井作业中的核心设备,主要用于起下钻具、管柱及井下工具,其性能和安全性直接关系到作业效率与人员安全。由于长期处于高负荷、高频率、恶劣环境(如粉尘、高温、腐蚀等)中工作,绞车的机械部件、制动系统、动力装置等易出现磨损、老化、变形等问题。若未定期进行专业检测,可能导致设备故障、作业中断,甚至引发安全事故。因此,通过系统化的检测项目对石油修井绞车进行全面“体检”,是保障设备稳定运行、延长使用寿命的关键措施。
石油修井绞车核心检测项目
1. 结构完整性检测
重点检查绞车底座、支架、滚筒等主体结构的焊接质量、裂纹及腐蚀情况。使用超声波探伤、磁粉探伤等无损检测技术,评估关键承力部件的疲劳损伤程度,确保整体结构无安全隐患。
2. 制动系统性能检测
包括刹车片的磨损量测量、制动力矩测试及制动响应时间分析。通过模拟重载工况验证制动可靠性,防止因制动失效导致的溜钻或游车失控事故。同时排查液压或气动制动系统的泄漏问题。
3. 动力传动系统检测
对绞车的发动机/电动机、变速箱、离合器、链条/齿轮传动系统进行功率输出测试和振动分析。检查轴承润滑状态、齿轮啮合间隙及传动效率,确保动力传输平稳且符合额定载荷要求。
4. 控制系统与安全装置检测
验证电气控制系统的灵敏度和稳定性,测试过载保护、紧急停车、限位开关等安全功能的触发条件。检查仪表盘及传感器(如压力、转速、温度传感器)的校准精度,确保数据反馈准确。
5. 载荷试验与动态性能验证
在空载、半载和额定载荷下进行起升、下放操作,记录滚筒转速、钢丝绳排绳状态及设备振动数据。通过动态测试评估绞车在不同工况下的运行稳定性,并确认最大工作载荷下的安全余量。
6. 钢丝绳与辅助部件检查
测量钢丝绳的直径变化、断丝率和锈蚀程度,依据标准判定是否达到报废阈值。同时检查滑轮、吊钩、防碰装置等辅助部件的磨损及固定情况,消除潜在风险点。
检测周期与标准化管理
根据行业规范(如SY/T 6582《石油钻采设备用绞车》)要求,石油修井绞车需定期开展年度全面检测,并在大修后或重大作业前进行专项检测。所有检测数据应形成报告存档,并指导后续维护计划的制定。通过建立数字化检测档案,可实现设备全生命周期管理,提升油田作业安全管理水平。
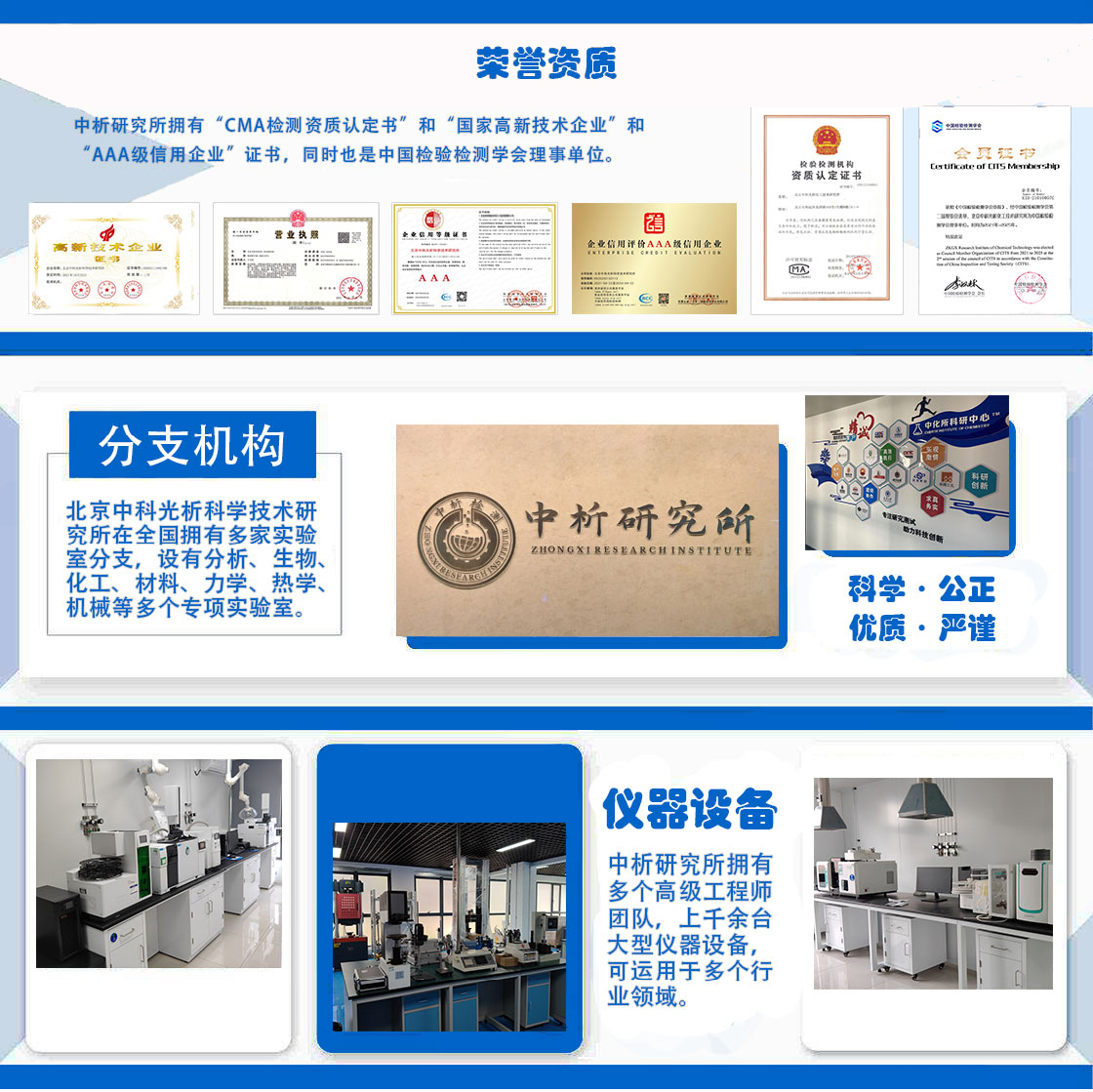
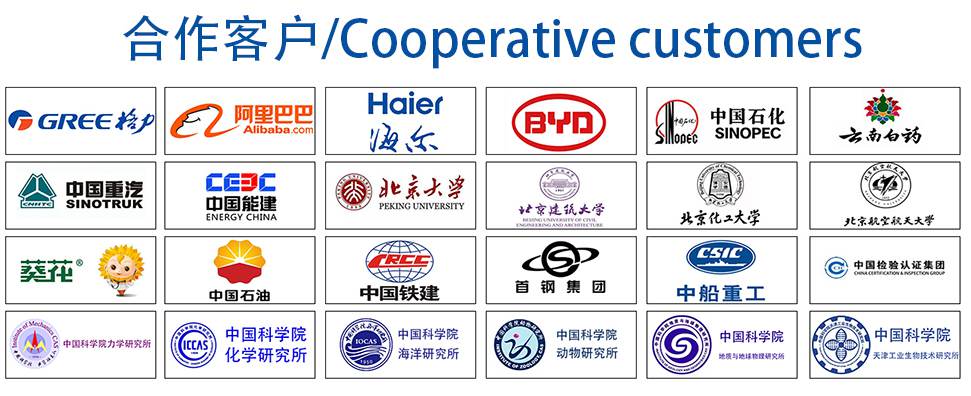