混动汽车节能试验检测的核心价值与技术挑战
随着能源结构调整和环保政策趋严,混合动力汽车(HEV/PHEV)凭借其燃油经济性与低排放特性,已成为传统燃油车向新能源车过渡的重要载体。根据中国汽车工程学会统计,2023年我国混动汽车市场渗透率已突破15%,其节能性能的可靠性直接关系到国家"双碳"目标的实现进程。在产业化快速推进的背景下,混动汽车的节能试验检测体系正面临从实验室标准工况向真实用车场景延伸、从单一能效评估向全生命周期碳足迹追踪的技术升级需求。
动力系统能效验证
整车能量流分析采用示功器与CAN总线数据采集系统,精确测量内燃机、电动机、发电机、动力电池之间的能量转换效率。在NEDC/WLTP测试循环中,需同步记录发动机启停频次、电机助力介入时机、电池SOC变化曲线等1200余项参数,通过热力学模型计算系统综合效率。某自主品牌PHEV车型测试表明,其混动系统在40-80km/h巡航工况下的能量利用率较传统燃油车提升38%。
能量管理策略评估
基于HiL(硬件在环)测试台架构建虚拟驾驶场景,验证不同驾驶模式(EV/HEV/SPORT)下的控制逻辑合理性。通过注入3000组涵盖城市拥堵、高速巡航、山地爬坡的测试案例,评估ECU对动力分配、变速箱换挡、能量回收的决策响应速度。某合资品牌测试数据显示,其智能能量管理系统可使综合油耗降低12%,同时将电池循环寿命延长至行业平均水平的1.3倍。
实际道路排放检测
采用PEMS(便携式排放测量系统)开展RDE(实际驾驶排放)测试,在包含30%市区、50%市郊、20%高速的真实路况下,连续监测CO₂排放量及PN(颗粒物数量)。某检测机构数据显示,部分插混车型在电池亏电状态下的实际油耗较认证值偏差达25%,这推动着新版GB/T 19753标准新增低电量模式测试要求。
电池系统性能测试
在环境仓内模拟-30℃至55℃极端温度,进行2000次充放电循环试验,监测容量衰减率与内阻变化曲线。采用EIS(电化学阻抗谱)分析电极材料老化机理,同步验证BMS对热失控的防护能力。某动力电池企业测试表明,其新一代磷酸铁锂混动专用电池在45℃高温下的容量保持率达到行业领先的98.2%。
智能能量回收验证
通过底盘测功机模拟不同制动强度(0.1g-0.3g),测试CRBS(协同再生制动系统)的扭矩分配精度。使用激光位移传感器测量制动踏板行程与液压制动力关系曲线,确保机械制动与电制动实现毫秒级无缝衔接。某新势力品牌测试数据显示,其智能回收系统可贡献高达25%的续航里程提升。
当前行业正在推进虚拟标定(ViL)、数字孪生等创新检测技术,通过构建包含天气、路况、驾驶行为的数字模型,将传统检测周期缩短40%以上。随着C-NCAP将混动系统安全性纳入2024版规程,以及欧盟即将实施的全生命周期碳排放法规,节能试验检测正在从单一性能验证向多维综合评价体系演进,这对检测设备的智能化水平与工程师的跨学科能力提出了更高要求。
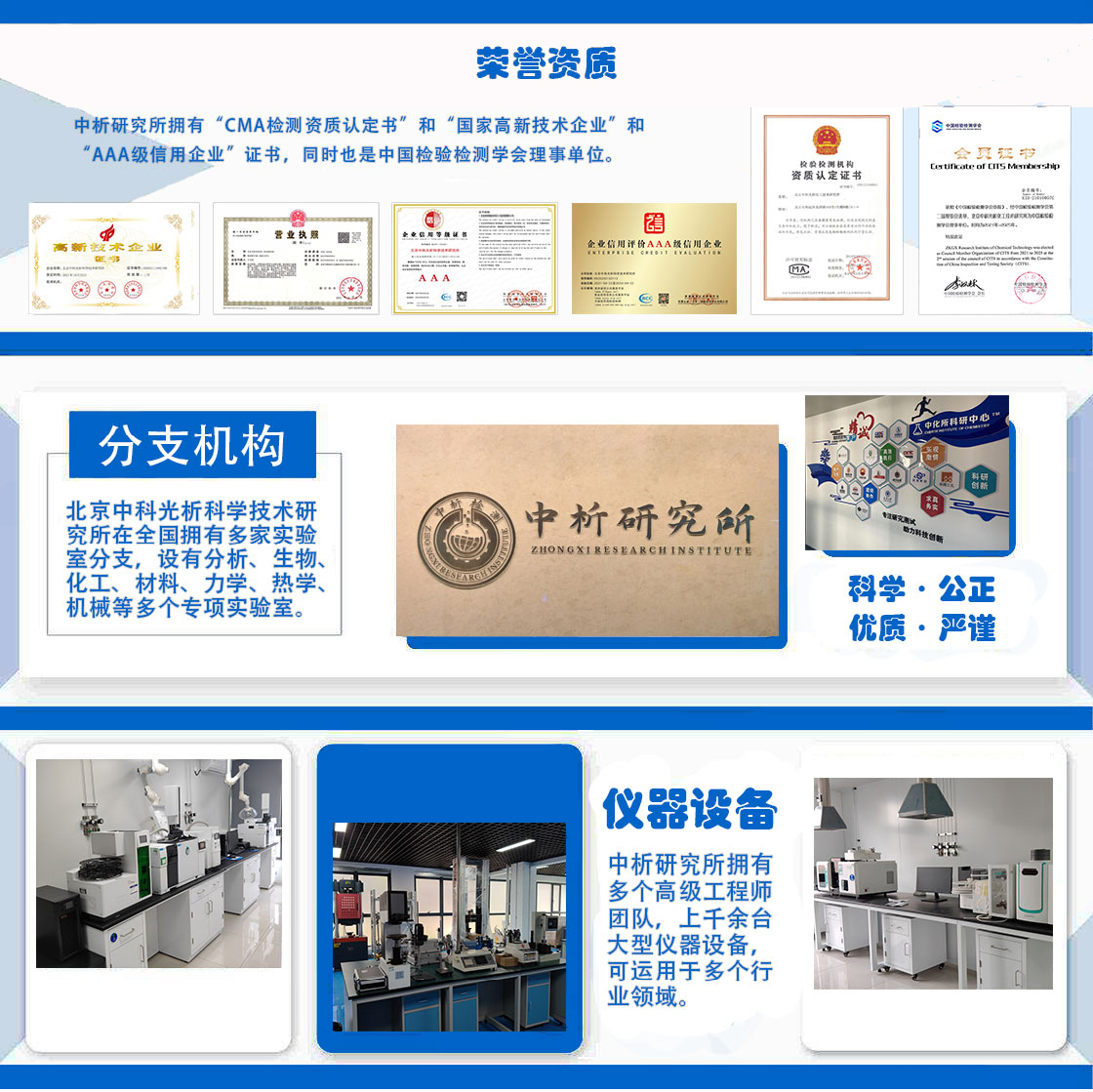
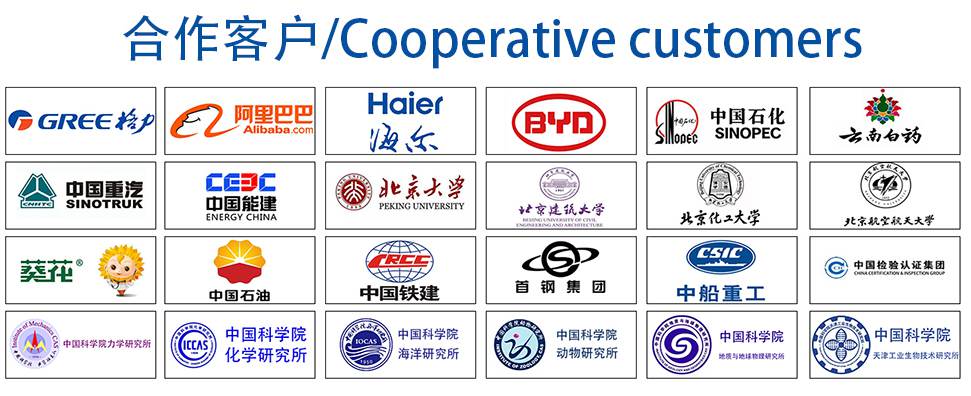