合成长丝用筒管检测的重要性与技术要求
在化纤生产领域,合成长丝用筒管作为卷绕丝线的核心载体,其质量直接影响纺丝效率和成品品质。随着高速纺丝技术的普及和差异化纤维需求的增长,筒管的尺寸精度、材质性能及表面质量成为生产链条中不可忽视的环节。通过对筒管系统化的检测,不仅能减少断丝、缠结等生产异常,还可延长设备使用寿命,降低企业综合成本。本文将从关键检测项目出发,深入解析筒管质量控制的技术要点。
一、尺寸精度检测
筒管的内径、外径、长度及锥度偏差需控制在±0.02mm以内,使用三坐标测量仪进行三维全尺寸扫描。特别注意法兰端面的平行度检测,偏差超过0.05mm可能导致卷装成型不规整。针对高速纺(6000m/min以上)专用筒管,需增加热膨胀系数测试,模拟实际工况下的尺寸稳定性。
二、材质理化性能分析
采用X射线荧光光谱仪(XRF)验证聚碳酸酯(PC)或增强尼龙(PA66-GF30)的材质成分,确保玻璃纤维含量偏差≤1.5%。通过熔融指数仪测定材料流动性,指标需符合GB/T 3682标准要求。硬度测试使用邵氏D型硬度计,标准值范围应控制在85-92HD之间。
三、表面质量检测
运用200倍工业显微镜观察筒管表面,要求无>0.1mm的注塑飞边或划痕。粗糙度检测采用接触式轮廓仪,Ra值需≤0.8μm。对静电纺丝工况,需额外进行表面电阻测试,指标应维持在10^6-10^8Ω范围内,防止丝线吸附。
四、力学性能测试
通过万能材料试验机模拟筒管承载状态,径向压力需≥800N(Φ200mm规格)。跌落测试从2m高度自由坠落至混凝土基面,连续3次无结构性破裂。动态疲劳测试需完成10^5次装夹循环后,内孔变形量仍<0.03mm。
五、环境适应性验证
在恒温恒湿箱中进行(-20℃~120℃)温度交变试验,评估热应力变形量。耐化学试剂测试需浸泡于DMAC溶剂24小时后,质量损失率<0.5%。湿热老化测试(85℃/85%RH)500小时后,弯曲强度保留率需≥90%。
六、动平衡等级检测
使用G6.3级动平衡机在4000rpm转速下测试,剩余不平衡量应≤2g·mm/kg。对于超细旦纤维(<50dtex)专用筒管,需提升至G2.5级精度标准。振动加速度峰值不得超过0.8m/s²(按ISO1940标准)。
七、使用寿命评估体系
建立模拟纺丝站位的加速试验平台,记录筒管在连续卷绕-退绕500次后的性能衰减数据。关键考核指标包括内孔椭圆度变化(≤0.04mm)、表面磨损深度(≤2μm)、抗静电性能衰减率(<15%)等,综合评估产品使用寿命周期。
通过上述系统性检测体系的建立与实施,企业可有效把控筒管质量,提升纺丝工序稳定性。建议结合MES系统建立数字化质量档案,实现检测数据与生产参数的智能联动,为工艺优化提供数据支撑。
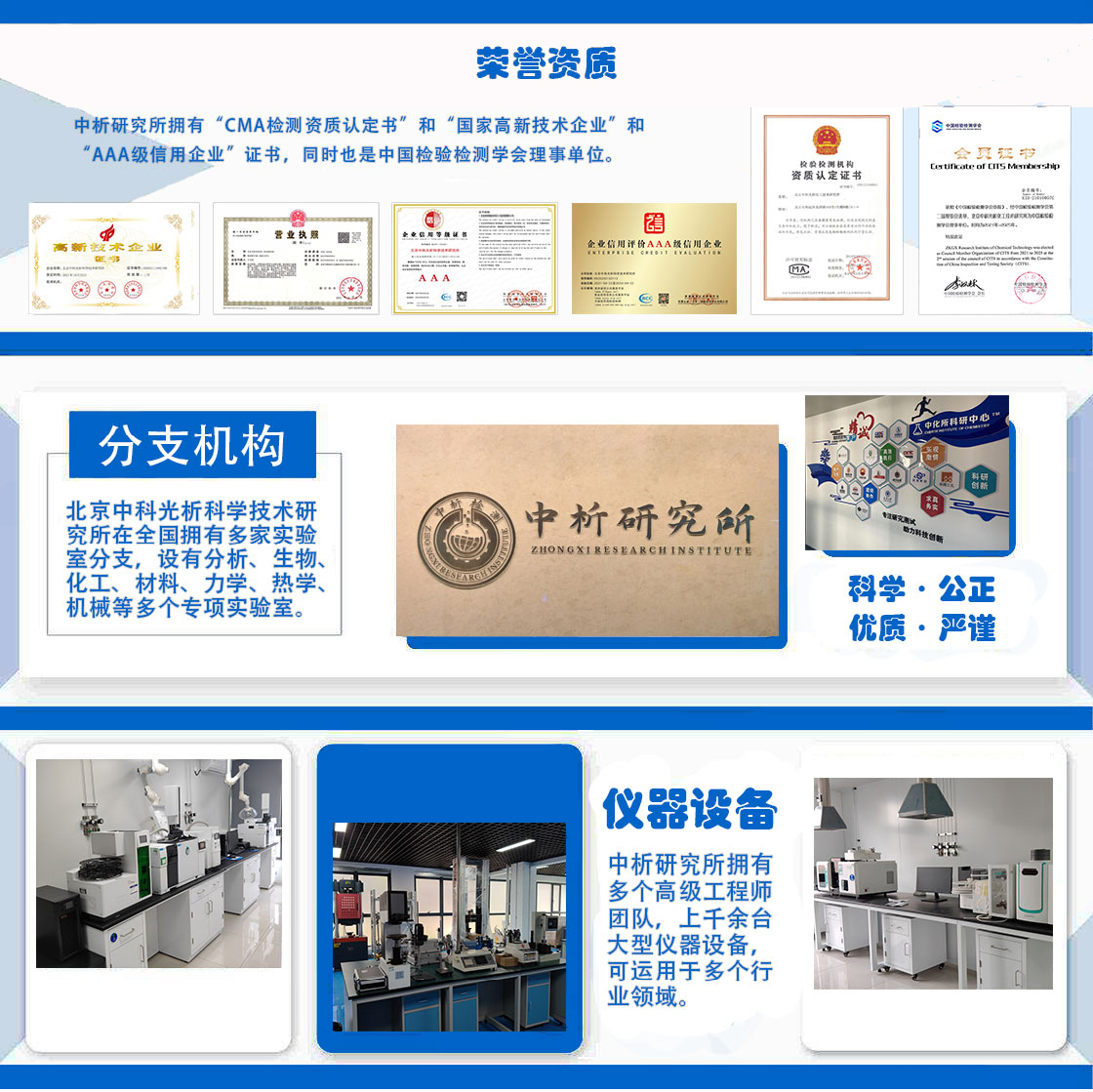
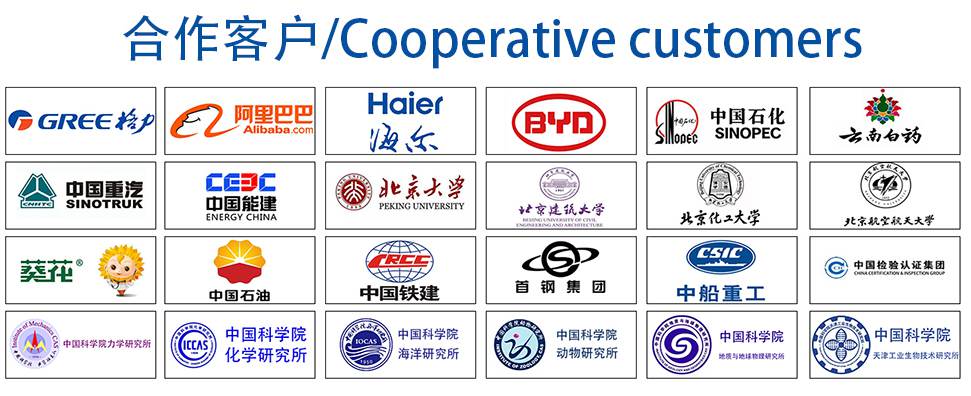