化工用石灰石检测的重要性及核心指标详解
石灰石作为化工行业重要的基础原料,广泛应用于碳酸钙生产、电石制造、烟气脱硫剂制备等关键领域。其品质直接关系下游产品的性能稳定性和生产工艺的安全性。据统计,2022年我国化工行业石灰石年消耗量突破7亿吨,但约15%的原料因质量不达标导致生产异常或产品缺陷。因此,建立科学的检测体系对石灰石原料进行全维度质量把控,已成为化工企业保障生产安全、优化工艺参数、降低运营成本的关键环节。
一、化学成分检测项目
碳酸钙含量(CaCO3)作为核心指标,采用酸碱滴定法(GB/T 5762-2012)精确测定,要求工业级石灰石纯度≥90%;二氧化硅(SiO2)含量通过X射线荧光光谱仪分析,控制值需≤5%,避免影响反应活性;氧化镁(MgO)采用EDTA络合滴定法检测,当含量超过2.5%时可能引发设备结垢;氧化铝(Al2O3)和氧化铁(Fe2O3)总量应<3%以防止催化副反应。
二、物理性能检测体系
表观密度按ASTM C29标准进行振实法测定,优质石灰石应达到1.5-2.6g/cm³区间;莫氏硬度使用划痕法测试,标准硬度3级可确保破碎效率与运输稳定性;吸水率通过浸泡称重法测定,数值超过2%的原料需进行干燥预处理。粒径分布采用激光粒度仪分析,D50值控制在30-100μm可优化反应接触面积。
三、特殊杂质专项检测
硫化物含量通过燃烧碘量法检测,严格限定S≤0.05%以防止设备腐蚀;磷含量使用分光光度法测定,超标的磷(P>0.03%)会导致催化剂中毒;重金属元素(Pb、Cd、Hg)采用ICP-MS法分析,参照HJ 781-2016标准限值管控;放射性核素按GB 6566标准进行γ能谱检测,确保内照射指数≤0.5。
四、矿物组成与结构分析
XRD衍射分析精确测定方解石含量(标准≥85%),同时检测白云石、石英等伴生矿物比例;扫描电镜(SEM)观察晶体形貌,柱状或菱面体结构具有更优的化学反应活性;比表面积(BET法)指标直接影响反应速率,优质原料应>2m²/g;孔隙率通过压汞法检测,理想范围在15-25%之间。
五、环境适应性检测指标
耐酸性测试采用pH=3硫酸溶液浸泡法,要求24小时质量损失≤5%;耐热性通过马弗炉程序升温试验,750℃煅烧2小时后的活性度应达300mL以上;抗压强度使用万能试验机测定,≥50MPa的原料可确保运输过程完整性;风化系数按ASTM D5240标准计算,要求>0.8以保证储存稳定性。
化工企业需建立包括抽样方案(GB/T 2007.1)、检测周期(建议每批次必检)、数据比对(与ASTM C25标准对照)在内的完整质量管控体系。建议选择配备XRD、ICP-OES等齐全设备的第三方检测机构,同时建立原料数据库实现质量追溯。通过科学的检测手段和严格的验收标准,可有效提升产品合格率3-5个百分点,降低原料浪费成本约12%,为化工生产提供可靠保障。
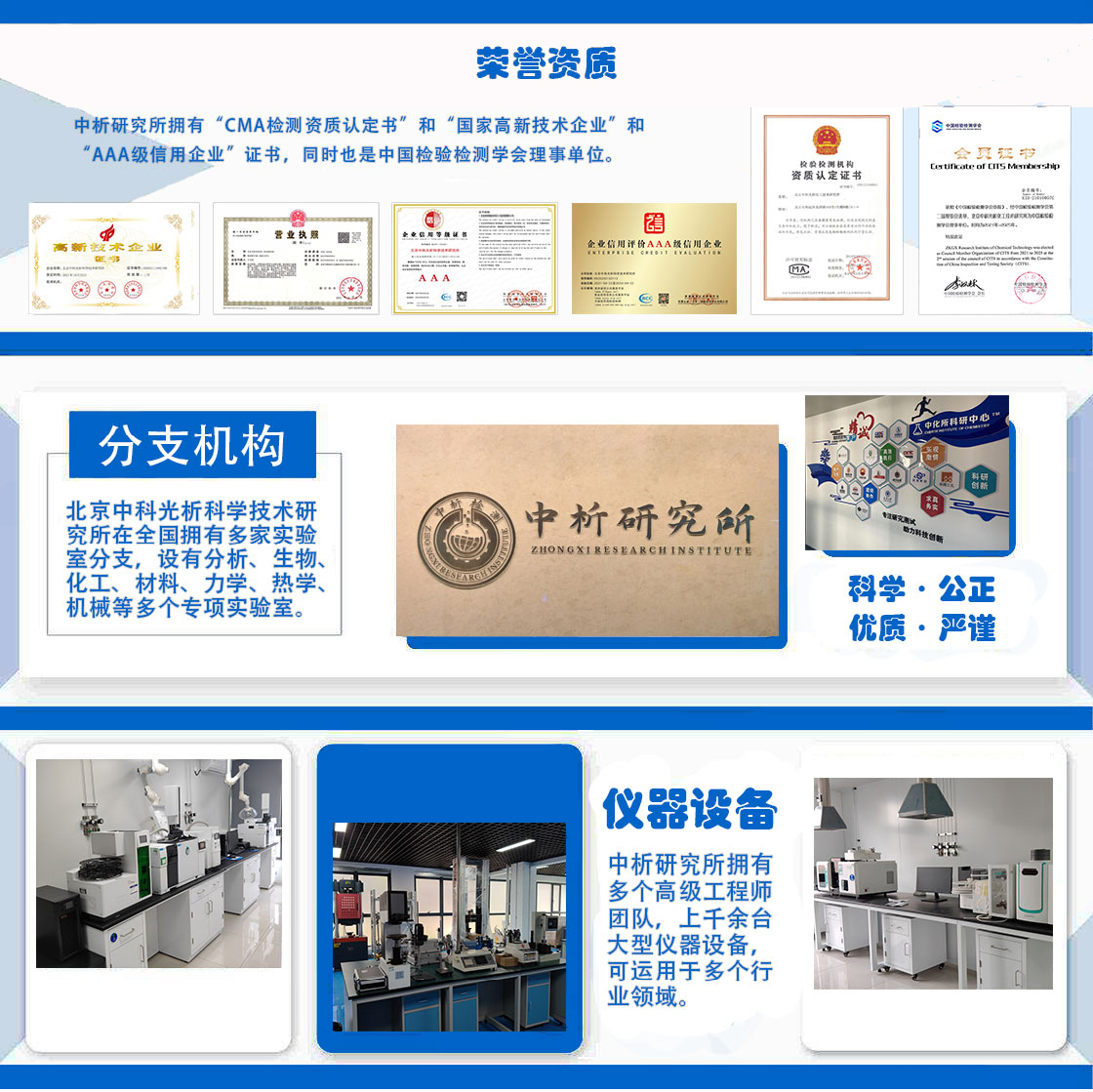
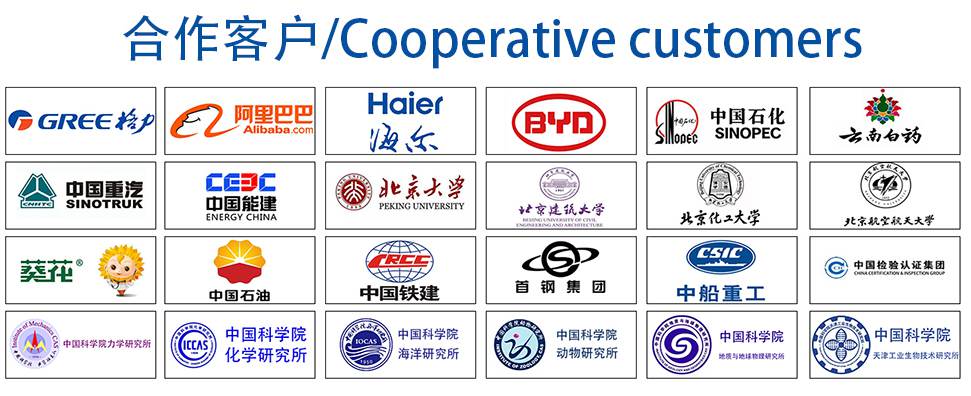