埋地钢质管道环氧煤沥青防腐层检测的重要性
埋地钢质管道作为石油、天然气、供水等领域的核心输送设施,长期处于土壤、水分、微生物及化学介质的复杂环境中,极易发生腐蚀问题。环氧煤沥青防腐层凭借其优异的附着力、耐化学腐蚀性和机械强度,被广泛应用于管道外防腐保护。然而,由于施工工艺差异、环境侵蚀或材料老化,防腐层可能出现破损、剥离或厚度不足等问题,直接影响管道的安全性和使用寿命。因此,通过系统化的检测项目对防腐层进行定期评估,是保障管道运行安全的必要手段。
环氧煤沥青防腐层的主要检测项目
1. 外观检查
通过目视或高倍放大镜观察防腐层表面是否存在气泡、裂纹、针孔、褶皱或机械损伤等缺陷。对于重点区域(如焊缝、弯头、补口部位),需使用数码相机记录并分析异常形态,判断是否为施工缺陷或外部破坏导致。
2. 厚度测量
采用磁性测厚仪或超声波测厚仪,按SY/T 0447标准要求,每20米至少选取1个测量点,单点测量值需≥0.4mm(普通级)或≥0.6mm(加强级)。检测时需注意避免金属基底干扰,并确保仪器校准符合GB/T 4956规范。
3. 粘结强度测试
依据GB/T 5210标准,使用拉开法或划格法评估防腐层与钢管基体的附着力。合格粘结强度需≥4MPa(拉开法),划格法要求1级或2级(涂层无剥离)。测试前需清除表面浮锈及污染物,确保数据准确性。
4. 电火花检漏
利用电火花检漏仪(电压范围2-5kV)对防腐层进行全覆盖扫描,通过检测电流变化判断是否存在针孔或漏涂缺陷。检漏电压需根据防腐层厚度按公式U=3290√T(T为厚度,单位mm)计算,避免过电压击穿完好涂层。
5. 绝缘电阻检测
采用直流电位差法或变频选频法,测量防腐层整体绝缘电阻值。根据SY/T 5918标准,绝缘电阻需≥10000Ω·m²(普通级)或≥15000Ω·m²(加强级)。高电阻值表明防腐层完整性强,可有效阻隔电化学腐蚀路径。
6. 耐化学性试验
针对特定工况环境(如酸性土壤、盐碱地),需在实验室模拟条件下进行耐酸碱、耐盐雾加速试验。按GB/T 9274标准,将试样浸泡于5%NaCl溶液或pH=3的H2SO4溶液中30天,观察是否有起泡、软化或剥离现象。
7. 补口与补伤部位专项检测
对管道焊接接口、修补区域的防腐层进行重点检测,包括热缩带搭接宽度(≥100mm)、厚度均匀性及粘结密封性。使用红外热成像技术可快速发现补口处潜在的空鼓缺陷,避免局部腐蚀风险。
检测结果的应用与维护建议
根据检测数据建立防腐层健康档案,对等级评定为“差”或“严重”的管段,需制定修复计划并加密监测频率。建议结合阴极保护系统参数(如电位分布、电流密度)综合评估整体防腐效果,同时推广智能爬行机器人、无人机巡检等新技术,提升检测效率与覆盖范围。
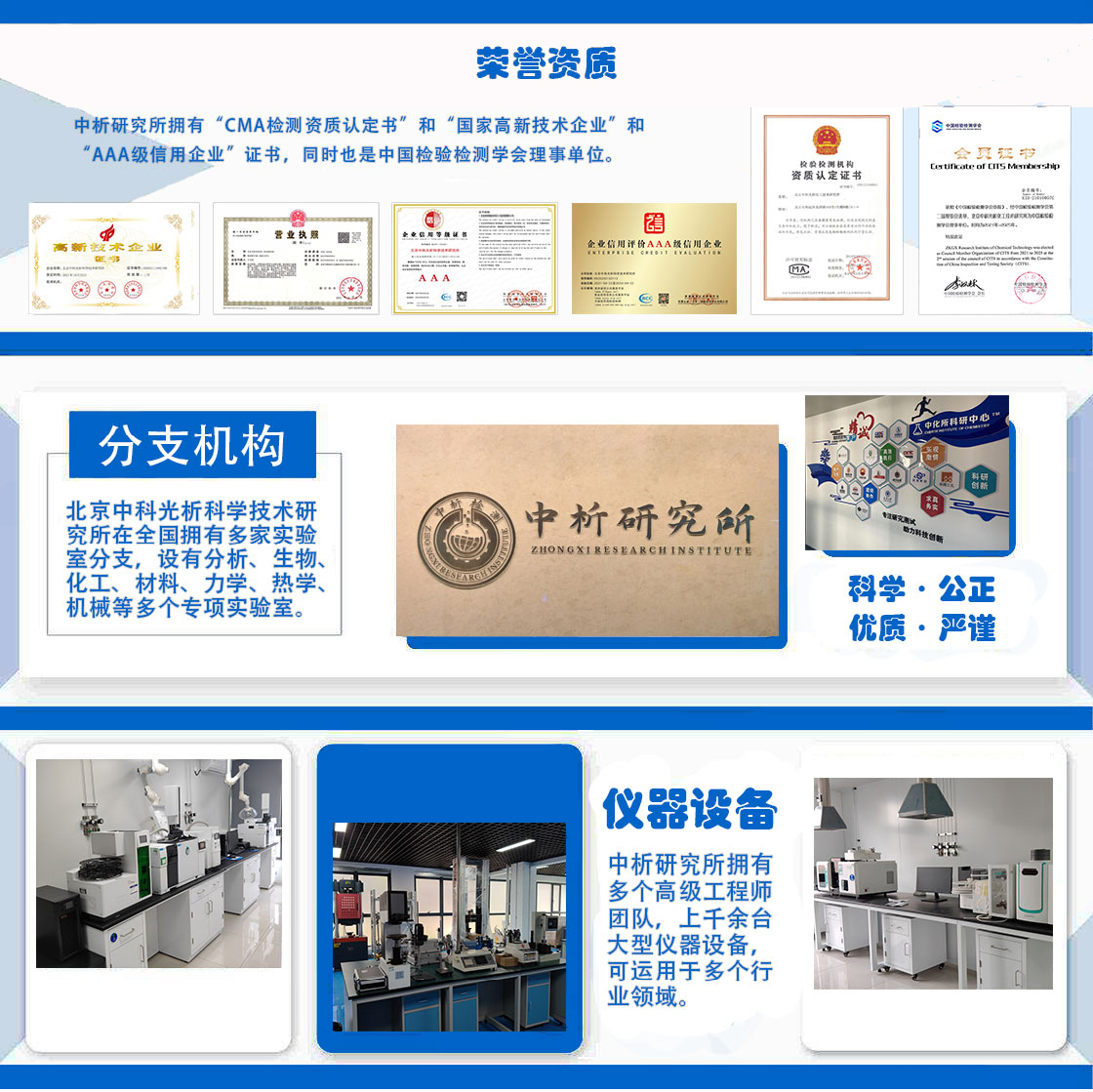
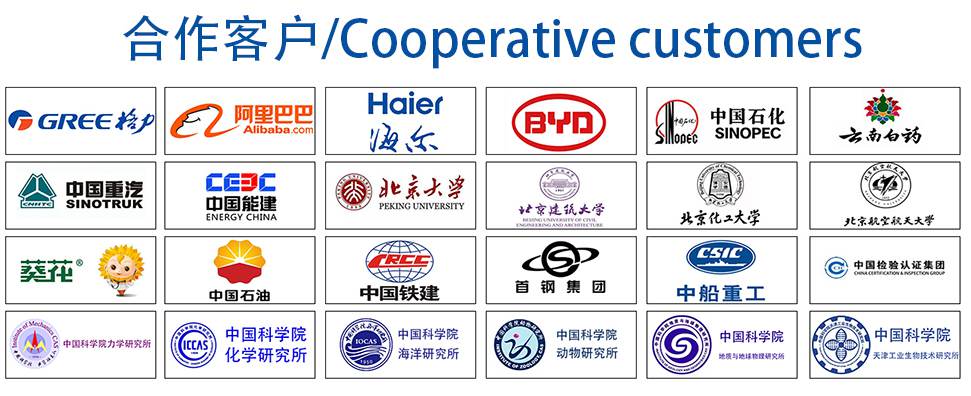