随着我国铁路建设的快速发展,混凝土结构作为轨道工程、桥梁、隧道等基础设施的重要组成部分,其耐久性和安全性备受关注。混凝土表面涂层作为保护层,能够有效隔绝水分、氯离子、二氧化碳等侵蚀性介质,防止钢筋锈蚀和混凝土碳化。然而,在复杂环境荷载、紫外线辐射及机械磨损作用下,涂层可能出现开裂、剥落、粉化等缺陷,直接影响结构使用寿命。因此,开展铁路混凝土结构涂层检测对保障工程质量、延长服役周期具有关键意义。检测项目需覆盖物理性能、化学性质及环境适应性等多维度指标,通过科学评价为维护决策提供依据。
一、涂层附着力检测
附着力是衡量涂层与混凝土基体结合强度的核心指标,直接影响保护效果。检测常采用拉拔试验法(ASTM D4541)或划格法(GB/T 9286),通过专用仪器测量涂层剥离所需的最大拉力。铁路工程要求附着力不低于1.5MPa,在潮湿区域或重载区段需提高至2.0MPa以上。试验需在不同位置取点,避免局部缺陷导致数据偏差。
二、涂层厚度检测
涂层厚度直接影响抗渗性和机械强度。采用磁性测厚仪(ISO 2808)或涡流测厚仪进行无损检测,重点检测棱角、接缝等易薄弱部位。根据TB/T 2965标准,环氧类涂层干膜厚度应≥300μm,聚氨酯类≥200μm。检测时需按照网格法布点,单点允许误差±10%,整体平均厚度不得低于设计要求。
三、耐腐蚀性检测
通过盐雾试验(GB/T 1771)模拟海洋环境或除冰盐侵蚀,评估涂层抗氯离子渗透能力。将试样置于5%NaCl溶液中连续喷雾,观察720小时后的起泡、锈蚀情况。铁路涂层需达到9级(10级制)以上耐蚀等级。电化学阻抗谱(EIS)可量化涂层孔隙率,阻抗值>1×10^8Ω·cm²视为合格。
四、抗老化性能检测
采用氙灯老化试验箱(GB/T 1865)模拟紫外线、湿热循环作用,测试2000小时后的光泽度变化(ΔE≤3)和粉化等级(ASTM D659)。对于高速铁路露天结构,要求涂层保光率≥80%,抗拉强度保留率≥90%。傅里叶红外光谱(FTIR)可分析化学键断裂程度,预判材料老化趋势。
五、外观质量与缺陷检测
采用高清工业相机结合图像处理技术识别裂纹、鼓包等缺陷,最小识别宽度达0.1mm。红外热像仪可探测空鼓区域(温差>2℃视为异常),敲击法(ASTM D4580)辅助验证。根据Q/CR 549标准,单个缺陷面积不得超过10cm²,单位面积缺陷率应<3%。
六、涂层化学成分分析
通过X射线荧光光谱(XRF)检测重金属含量是否符合环保要求,气相色谱-质谱联用(GC-MS)分析挥发性有机物(VOC)是否超标。对于改性涂层,需验证纳米材料(如SiO2、TiO2)的分散均匀性,采用扫描电镜(SEM)观察微观结构,确保功能添加剂有效发挥作用。
检测方法选择与实施
实验室检测可精确控制变量,但需破坏取样;现场检测应优先选用便携式设备,结合无人机搭载传感器实现高空区域快速扫描。推荐采用"初筛+复检"模式:齐全行全覆盖无损检测定位问题区域,再针对性开展破坏性试验。数据需接入铁路BIM管理系统,建立涂层性能退化模型,实现预测性维护。
检测结果的应用价值
科学的涂层检测可提前6-12个月预警失效风险,指导维修窗口期规划。对比历史数据能评估防护体系整体劣化速率,为涂层材料选型优化提供反馈。对于高铁无砟轨道等精密结构,检测数据还可用于计算剩余寿命,支撑全生命周期成本管理。
在"交通强国"战略背景下,铁路混凝土涂层检测正朝着智能化、标准化方向发展。通过引入机器学习算法分析检测大数据,建立不同气候区、荷载条件下的涂层性能数据库,将进一步提升检测精度与效率,为构建安全、绿色的铁路网络提供坚实保障。
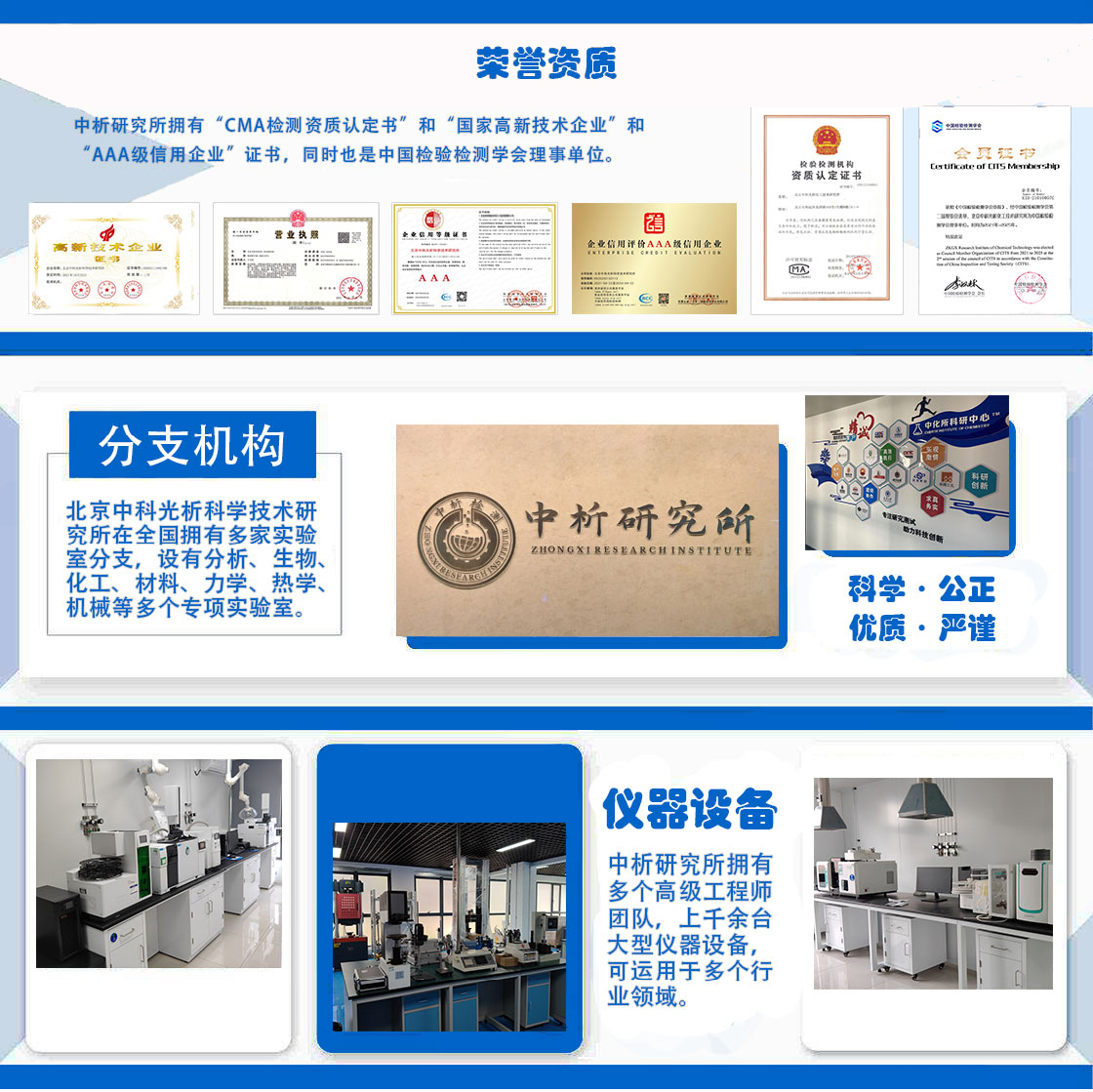
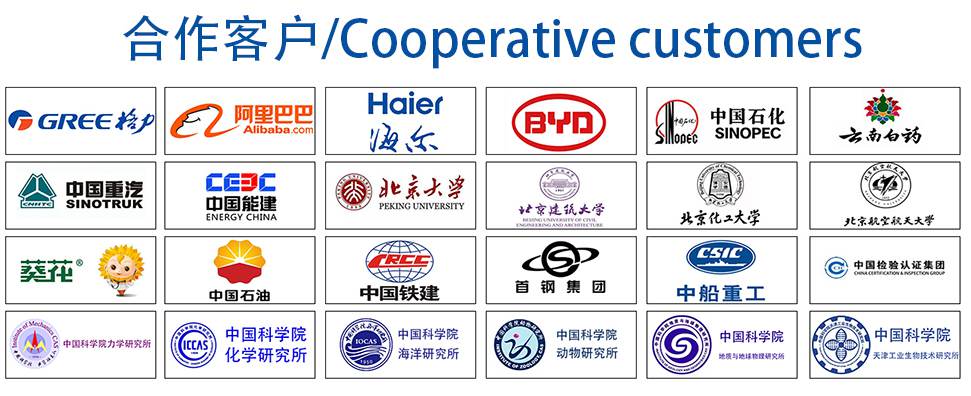