汽车同步带检测的重要性与核心项目解析
作为汽车传动系统的核心部件,同步带承担着精确传递动力、协调发动机配气机构与曲轴运转的关键作用。其性能直接影响发动机效率、燃油经济性及整体可靠性。随着汽车工业对零部件精度要求的持续提升,同步带检测已从简单的尺寸验证发展为涵盖材料特性、动态性能、耐久性等多维度的系统性评估流程。在高速运转、极端温度及复杂工况下,任何细微缺陷都可能导致传动失效,因此建立专业的检测体系对保障行车安全具有重要意义。
核心检测项目分类
1. 物理特性检测
采用三坐标测量仪对同步带进行全尺寸扫描,重点检测:
• 齿形轮廓精度(公差≤0.05mm)
• 节线长度偏差(要求≤0.3%)
• 带体宽度一致性(允差±0.5mm)
• 背胶厚度均匀性(波动范围<10%)
2. 材料性能测试
通过专业实验室设备验证材料特性:
• 氯丁橡胶/聚氨酯的拉伸强度(≥20MPa)
• 抗老化性能(70℃×70h热老化后强度保持率>80%)
• 齿面耐磨性(Taber磨耗试验<50mm³)
• 动态疲劳强度(100万次循环无裂纹)
3. 动态性能验证
在模拟工况测试平台上进行:
• 传动效率测试(目标值≥98%)
• 高速运转稳定性(6000rpm持续2小时)
• 温度适应性(-40℃~120℃工况模拟)
• 抗跳齿能力(突加30%负载时的同步保持性)
4. 耐久性试验
依据SAE J1459标准执行强化测试:
• 交变载荷寿命试验(目标15万公里等效)
• 盐雾腐蚀测试(480h表面无劣化)
• 臭氧暴露试验(50pphm浓度下500h无龟裂)
• 油污耐受性(浸泡24小时后强度损失<15%)
5. 安装参数检测
通过激光对中仪确保装机质量:
• 张紧力检测(推荐值200-400N)
• 皮带轮平行度(偏差≤0.5mm/m)
• 预紧扭矩验证(依据厂家标准±10%)
• 运转轨迹监测(振幅<0.3mm)
检测技术发展趋势
当前行业正推进智能化检测系统的应用,采用机器视觉实现微米级缺陷识别,结合AI算法对振动频谱进行预测性分析。部分齐全实验室已实现72小时连续动态监测,同步采集200+工况参数,大幅提升潜在失效模式的检出率。
结语
系统的同步带检测不仅需要齐全的检测设备,更依赖完善的测试标准和经验丰富的技术团队。建议制造商建立全生命周期质量档案,结合定期维护检测数据,实现对传动系统可靠性的精准把控。通过严格执行上述检测项目,可将同步带故障率降低80%以上,有效延长发动机使用寿命。
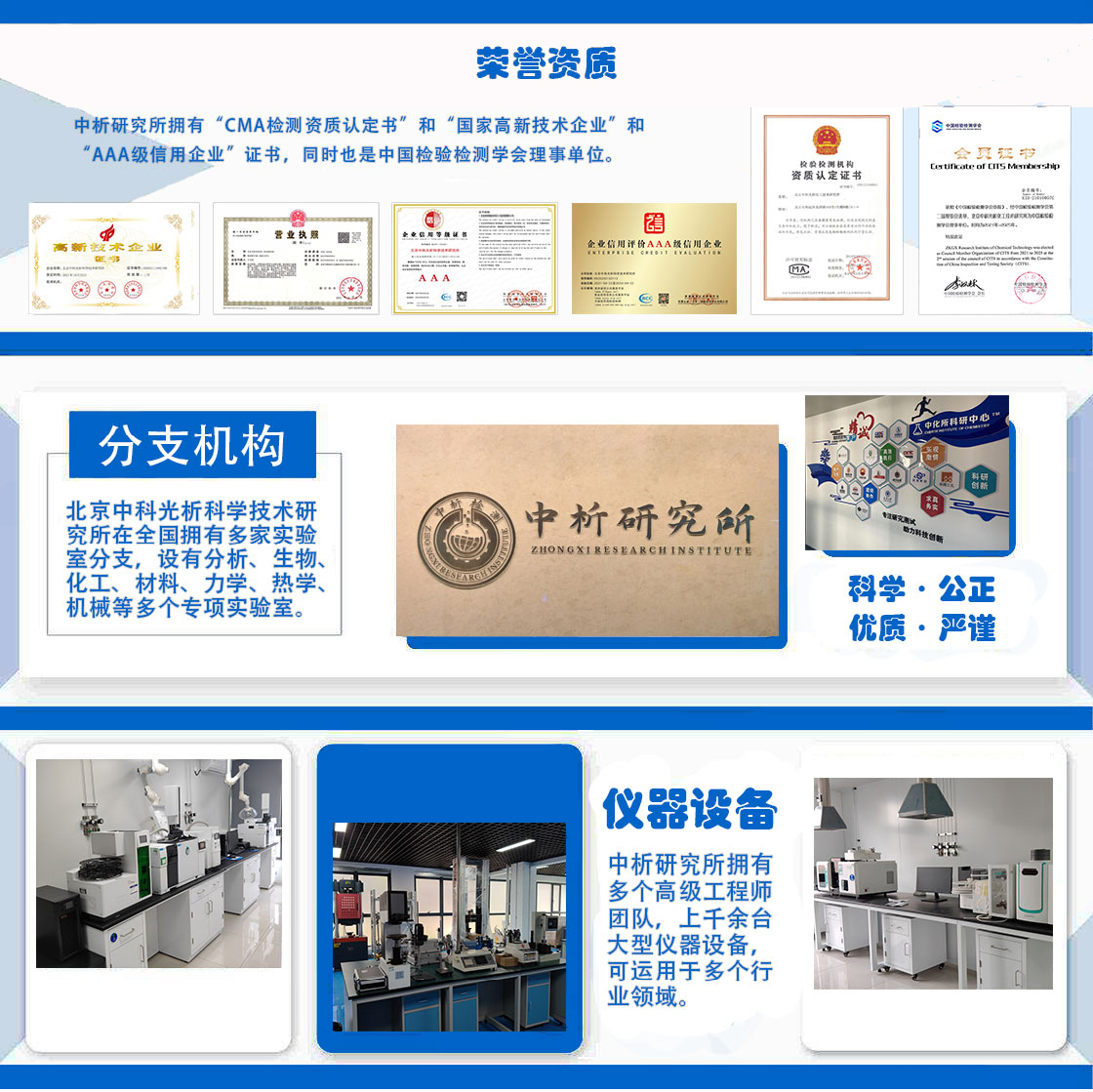
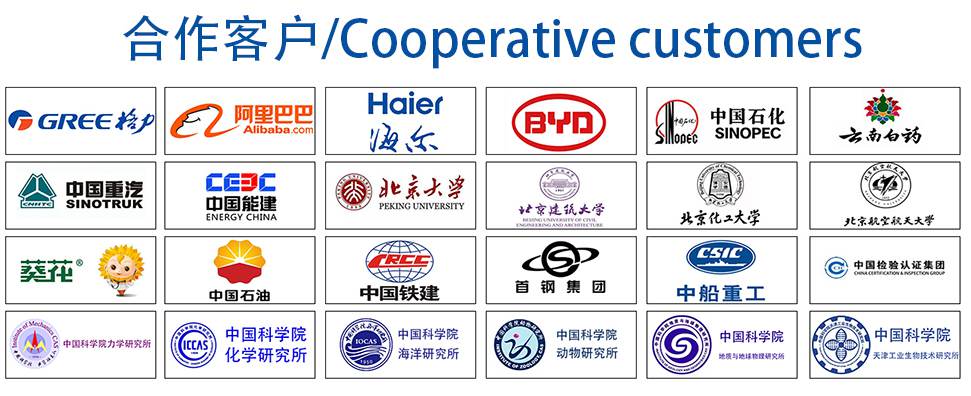