铸锻、焊接质量检测的重要性
铸锻和焊接作为现代工业制造的核心工艺,广泛应用于机械、汽车、航空航天、能源等领域。其质量直接关系到产品的安全性、可靠性和使用寿命。铸锻工艺涉及金属材料的熔融、成型及热处理过程,而焊接则是通过高温或压力实现材料的永久连接。若存在气孔、裂纹、夹渣、未熔合等缺陷,可能导致结构强度不足、疲劳失效甚至事故风险。因此,通过科学的质量检测手段及时发现并控制缺陷,是保障产品性能的关键环节。
铸锻质量核心检测项目
1. 化学成分分析
采用光谱分析仪、X射线荧光仪等设备,检测材料的元素含量是否符合标准(如GB/T 223),确保材料牌号和性能匹配设计要求。
2. 力学性能测试
通过拉伸试验、冲击试验、硬度测试(布氏/洛氏/维氏)等手段,评估材料的抗拉强度、屈服强度、延伸率及韧性,验证热处理工艺的有效性(依据GB/T 228、GB/T 229)。
3. 无损检测(NDT)
包括超声波检测(UT)定位内部裂纹、X射线检测(RT)识别气孔与夹杂、磁粉检测(MT)和渗透检测(PT)发现表面缺陷,覆盖铸锻件的三维质量评估。
4. 金相组织分析
通过显微镜观察材料微观结构(晶粒尺寸、相分布),判断是否存在过热、脱碳或偏析等异常,为工艺优化提供依据(参考GB/T 13298)。
焊接质量关键检测内容
1. 焊缝外观检查
依据ISO 5817标准,检查焊缝表面是否平滑、无咬边、未焊透、焊瘤等缺陷,测量余高和宽度是否符合工艺规范。
2. 无损探伤技术
应用X射线(RT)、超声波(UT)、磁粉(MT)检测焊缝内部及热影响区的裂纹、气孔、夹渣等缺陷,满足GB/T 3323或AWS D1.1等行业标准。
3. 力学性能测试
对焊接接头进行拉伸、弯曲、冲击试验(GB/T 2651),评估其强度与韧性;通过硬度测试对比母材与焊缝性能差异。
4. 腐蚀与密封性试验
采用盐雾试验(GB/T 10125)、氦质谱检漏等方法,验证焊缝在恶劣环境下的耐蚀性及密封能力,确保长期使用可靠性。
综合质量管控趋势
随着智能制造的发展,数字化检测技术(如工业CT三维成像、智能视觉识别)与工艺仿真相结合,显著提高了缺陷检出率与检测效率。企业需结合产品特性,制定涵盖原材料、工艺参数、成品检测的全流程质量体系,并定期校准设备、培训人员,确保检测结果的准确性与一致性。
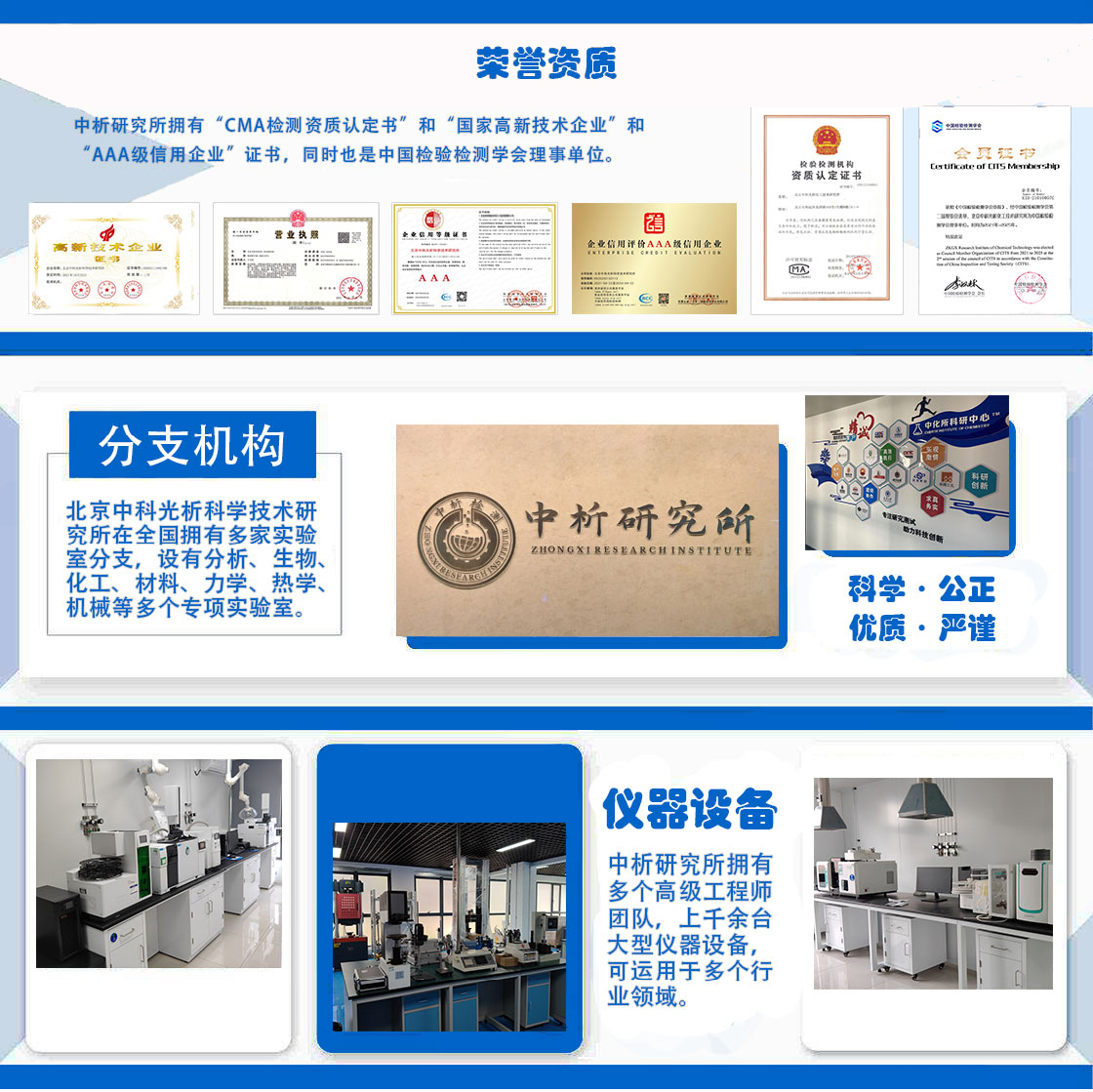
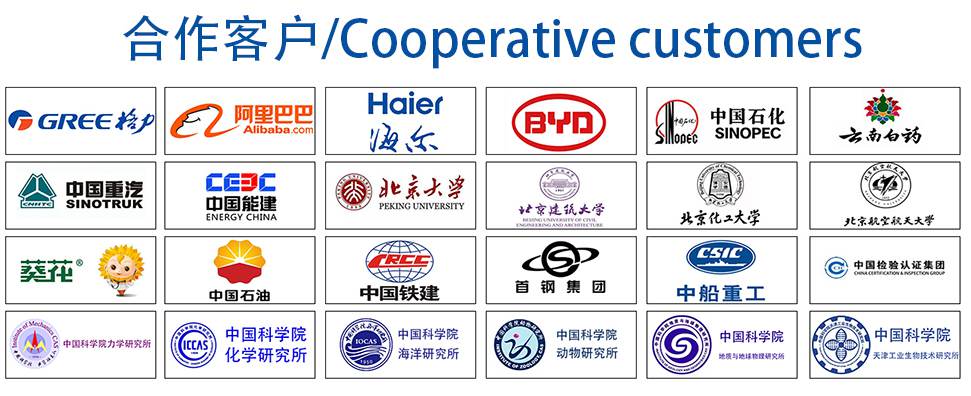